First, contact us!
Request a quote and provide drawings or photos as necessary. Send parts to SilcoTek for coating service.
After receiving drawings or a part description we’ll send you a coating quote. Our team will respond within one business day to your coating quote request, we may ask for any additional information needed to issue an accurate quote. We’ll also give you shipping instructions along with an RA# for shipping your parts to our coating facility. After receiving the quote, the customer will disassemble the part as needed and ship the items to be coated to our coating facility. Because our chemical vapor deposition process requires dedicated specialized equipment and processing, coating is only applied at our facility.
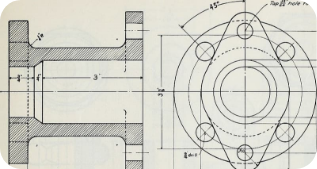
Getting the Order
Receipt, review and order acknowledgment.
Once received, your parts are inspected to ensure we got everything you sent. We also photograph the parts for verification and traceability. If there are any questions or “red flags” before coating, our Customer Service Representative will contact you to review your order and any potential concerns with processing. Substrates are verified and if listed on our material compatibility chart as “not treatable” will either be returned directly to you or along with your compatible parts after coating. Once everything is confirmed, our customer service team sends you an order acknowledgment email with our ship by date.
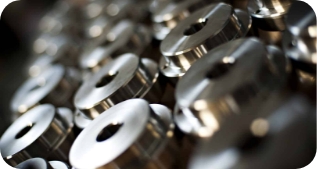
Expedite Program
SilcoTek takes special care to collaborate with all our customers and provide exceptional service that exceeds your expectations. Our manufacturing process is designed to expedite every order that we process. For those customers who are in a crunch and need faster turn around times, we now offer a 2-tiered expedite program! Customers who need to expedite their lead time by 3-4 business days can take advantage of our expedite coating service. To improve lead times by 5 or more business days, customers can utilize our priority coating service. It is important to note that while we hope to accommodate every expedite and priority processing request to assist customers who require improved lead times, there will be times that we must decline due to high order volumes at our facility. It is critical to us that no customer who accommodates SilcoTek’s standard coating process lead times ever experiences longer turnaround as a result of honoring expedite requests.
While our ultimate goal is to reduce S.T.A.G. (ship time average goal) as much as possible, parts occasionally need to be re-worked to ensure the coating meets our specifications and high expectations for quality. Rest assured we understand the urgency of your parts and will do everything we can to coat them quickly and with the top-notch quality you’ve come to expect from us. Visit our FAQ page for any additional information related.
Starting the Process
Surface Preparation
SilcoTek uses proprietary surface preparation methods in order to ensure the best coating possible. It is important to know that any surface imperfections like scratches, rough surfaces, or widely varying surface characteristics, will be highlighted by the coating process, not hidden. That’s why creating a pristine, contaminant free surface prior to coating is critical for optimal results and good visual appearance. Unfortunately metal working and machining processes can impart contamination throughout the part surface that is hidden to the naked eye, so be sure to help us understand everything your parts have been exposed to prior to sending them to us for coating.
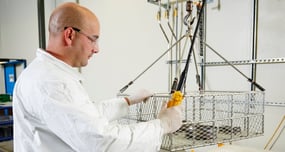
Applying the Coating
Chemical Vapor Deposition Coating Process
After a thorough surface preparation, our technicians load customer parts into a vacuum vessel corresponding to the size of the parts. This vessel is placed in a large oven and connected to the raw material - gas - then heats to temperatures near 400° C. Throughout this process, a proprietary blend of gas enters the vessel and starts a reaction which diffuses the treatment into the molecular lattice of the substrate, forming the ultra-thin SilcoTek coating that so many have come to recognize and trust.
With our process, 100% of your parts are coated, even if the design is complex or the pathways are tortuous.
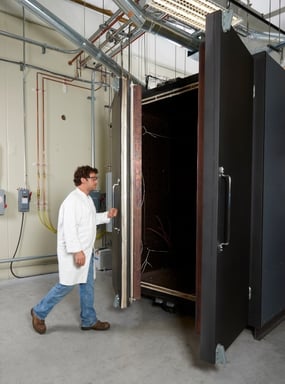
Quality inspection
Once the coating process is complete, your parts are unloaded and moved to the inspection area. SilcoTek Technicians then visually inspect parts to ensure conformal thickness and proper aesthetics and then review coating run data to verify all process parameters meet specification. Parts that pass inspection are issued a coating certification adherent to ISO 9001.

Packaging and Shipping
After the parts have passed inspection, we package them so that they are secure and won’t be damaged when traveling to the field, plant or back to the factory. Customer packaging is only re-used for return shipping upon request. If, at receipt, incoming packaging is deemed inadequate for secure shipping, SilcoTek will use new packaging to ensure coated parts are returned safely. If shipping out of the United States, our international customer support specialist will work closely with you to arrange logistics efficiently.
Once the parts are ready to go, we send you one last email to confirm that they are shipping by your preferred method. They’re now coated, to spec, and ready to make what was impossible possible!
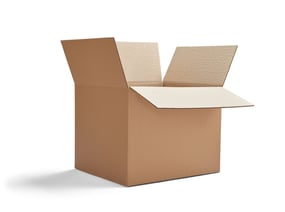