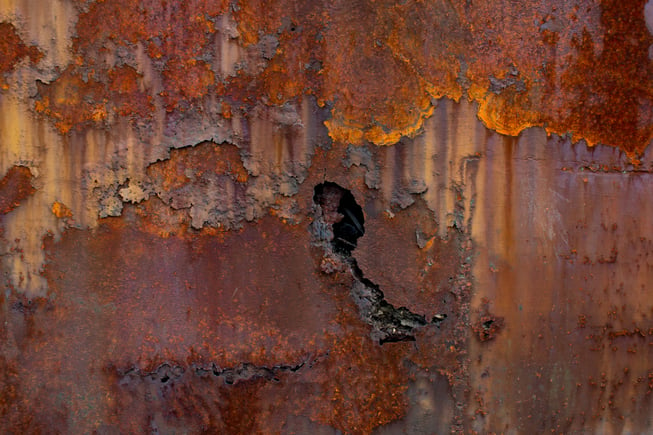
Our customers rely on SilcoTek coatings to tackle challenging corrosion issues. Given the infinite variety of environmental conditions, we encourage thorough evaluation of our recommended coatings in specific applications. While definitive test data for every unique scenario is unlikely, extensive studies in a range of common corrosive environments have shown that our Siltride, Silcolloy, and Dursan coatings deliver significant protection benefits when applied to appropriate substrates.
Despite consistent performance across various conditions, customers often ask: “Will a thicker coating make my part more corrosion resistant?” The answer, as with many corrosion-related questions, is nuanced. Simply put: it depends.
Thicker Coatings and Corrosion Resistance
Rather than pursuing thicker coatings, SilcoTek focuses on refining coating quality and consistency to maximize corrosion resistance with thinner layers. This approach provides both durability and improved performance, leveraging the unique properties of our coatings. In general, thicker coatings can enhance corrosion resistance by extending the diffusion barrier, reducing the interaction between corrosive agents and the substrate. However, increasing SilcoTek's CVD coating thickness may introduce challenges such as:
- Film stress: Thick films are more prone to cracking and delamination.
- Surface failure: Stresses may develop at critical points within the coating.
- Particle generation: Thicker coatings increase the likelihood of particles detaching.
- Demensional limitations: Mechanisms may restrict the feasible thickness.
- Prolonged deposition: Extended processing can alter metallurgical properties.
To address the idea that thicker coatings would enhance corrosion resistance, we conducted experiments evaluating the impact of coating thickness on corrosion resistance within our typical production ranges. Below is a comparison of Silcolloy and Dursan coatings, tested at both lower and higher thickness levels. Coupons were immersed in 6M hydrochloric acid at room temperature for up to 168 hours, following ASTM G31 guidelines.
Coating |
Thickness Range (nm) |
Corrosion @ 24 Hours (MPY) |
Corrosion @ 168 Hours (MPY) |
SL1000 (thin) |
250–320 |
1.93 |
65.5 |
SL1000 (median-high) |
750–1200 |
0.94 |
30.8 |
Dursan (thin) |
300–350 |
1.18 |
52.1 |
Dursan (median-high) |
650–900 |
1.50 |
21.5 |
In addition, a newer SilcoTek coating, Siltride, has been added to our arsenal since this experiment was conducted. Siltride shines as a coating for corrosion protection. The graphs below show it seriously outperforming uncoated coupons.
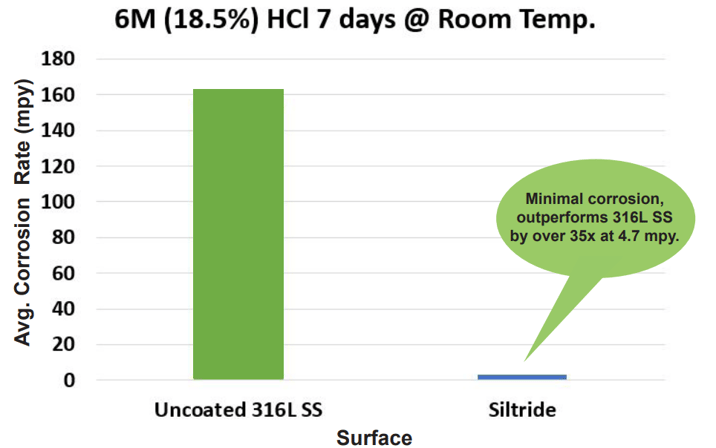
6M (18.5% HCl) 7 days at room temp. - Coupons were immersed in 6M HCl for 7 days at room temp (ASTM G31). This test shows an aggressive environment testing the limits of Siltride. In these conditions, Siltride performed well with minimal corrosion while considerably outperforming uncoated 316L SS.
50% H2SO4 1 Week - Coupons were immersed in 50 wt% H2SO4 for 168 hours at room temp (ASTM G31). When measuring the average corrosion rate (mpy), Siltride showed a nearly 7x improvement over uncoated 316L SS.
Instead of focusing on developing thicker coatings, we are innovating by creating superior corrosion-resistant materials that retain all the advantages of our ultra-thin coatings. These include exceptional adhesion, flexibility, conformity, and the ability to penetrate high aspect ratios, ensuring optimal performance and protection without compromising on the unique benefits of a thinner design.
Add Passivation for Increased Corrosion Resistance on Stainless Steel
As another alternative to thicker coatings for corrosion resistance, SilcoTek now offers citric acid passivation as a premium surface preparation step before applying our game-changing coatings. Passivation enhances the surface chemistry and inherent corrosion resistance of stainless steel by removing free iron that causes rouging, rust, and undesirable surface interactions.
While passivation is not required before SilcoTek’s coating processes, surface cleanliness is critical to coating success. Passivating stainless steel parts before coating creates an optimal coating surface and increases the corrosion resistance and overall performance of coated parts.
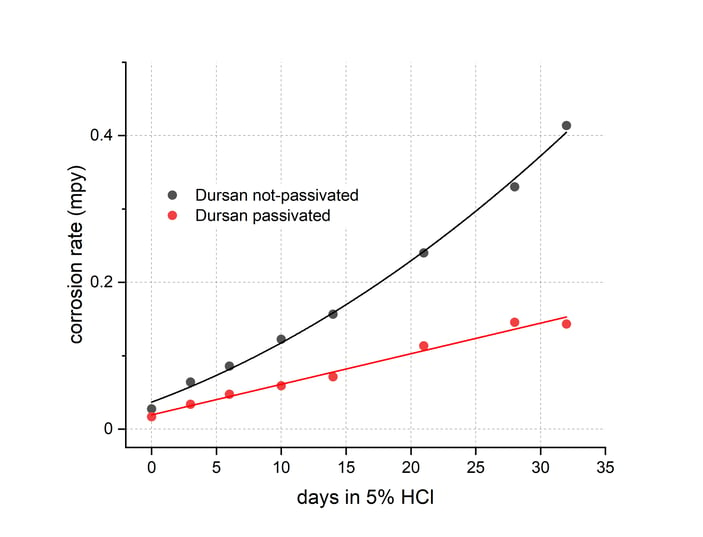
Reach out to our coating experts to discuss your application. We will work with you to determine the best coating!