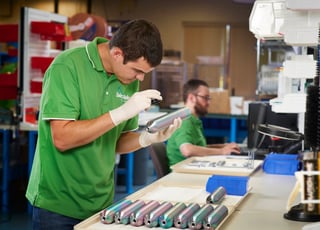
We discuss SilcoTek's CVD coating process and how quality is built into our company.
How SilcoTek Builds Quality into CVD Coatings
In this blog post you will learn:
- How SilcoTek's quality system is used to improve CVD coating quality.
- Get tips on employing quality tools in manufacturing operations.
- Understand SilcoTek's customer service philosophy and how it influences our quality system.
|
Our Goal: Zero Disappointments
At SilcoTek, we base our success on delivering an outstanding Plus 1 customer service experience coupled with exceptional coating quality. Our goal is to coat your parts perfectly the first time without altering them in any way aside from adding our high performance treatments to the surface. We call this effort Zero Disappointments, or Zero D, and our entire quality system is based around this basic yet critical principle.

How to build quality into a coating process?
It can take years to fully integrate quality principals into a process and, most importantly, teach, convince, and instill quality thinking into the entire manufacturing team. This includes support staff as well as line technicians. Building quality can be done in steps. Here's an example of the process.
First you need to learn about quality systems & what quality instruments you need to deploy and where. Tools like statistical process control, inspection systems and criteria, sampling and short term goals and long term goals are all important. Then there are the audits, lots and lots of audits; internal audits, ISO audits, customer audits, industry certification audits, etc.
After installing quality monitoring systems you're likely to have all the bells and whistles but you likely won't have a high performance quality system. And you certainly won't have the results you were hoping for. What's missing? People!
Process quality control with limited tools but employed and operated by dedicated people will likely outperform a complex system employing the latest technology but operated by people who don't buy into the idea of continual improvement.
The easy part of quality is installing tools, the hard part? Getting buy-in and building enthusiasm in the entire company. It can take months to set up the process measures, it can take years to get the team to accept and embrace the system.
Signs your production team is successful:
- Team members regularly call out quality problems and float solutions by the team
- Team members coach each other on improvements
- Team members anticipate problems and work to avoid the issue & improve processes.
- Team members tell you in no uncertain terms when an initiative is not working
Coaching the entire organization to support and grow the quality organization is essential and involves a lot of "soft skills" not suited to some people. It takes both leadership and excellent managerial skills to evolve a quality system. One without the other does not work. 
SilcoTek has invested tirelessly into improving and evolving our quality system. Our people are committed to the idea of continual improvement and Zero Disappointments. Here are some examples of how our team coordinates and employs quality tools using both technology and dedicated people.
SilcoTek quality control mechanisms are designed to meet our goal of Zero Disappointments
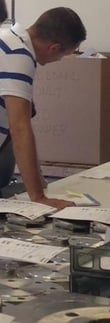
Incoming Inspection - Upon arrival to our facility, parts are visually inspected and photographed for traceability. Technicians search for any damage that may have occurred in transit or that the customer may otherwise be unaware of. For new parts or questionable substrates, we use a handheld x-ray fluorescence (XRF) analyzer to confirm that the substrate material is compatible.
If we find anything out of the ordinary, our customer service group immediately contacts the customer for their disposition on how to proceed with the coating process. At this stage, parts with special instructions for fixturing, handling, surface preparation, etc. are given custom traceable routings to ensure proper processing.
Surface Preparation - SilcoTek's surface preparation process is critical to a good coating (learn just how critical in this whitepaper). From this point forward, all parts are glove-handled to ensure that even fingerprints do not contaminate the surface. Automated cleaning and surface preparation systems minimize variation in surface quality. Statistical Process Control (SPC) is employed at critical steps in the process.
The surface prep team visually inspects parts to ensure 1) that no incompatible substrates or assemblies were overlooked at receipt and 2) the parts are free of any residue that would negatively impact the coating.
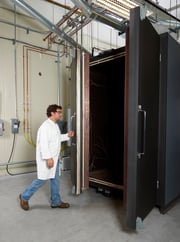
Coating - Parts are fixtured and loaded into the CVD deposition systems. The automated coating process has evolved over the years to optimize coating quality. Deposition system performance is monitored for deviation to established performance specifications. The most thorough inspection occurs after the CVD coating process. Once parts have cooled and are removed from the oven, they are moved to the inspection queue.
Final Inspection - Quality control technicians perform a thorough visual inspection, this time focusing on the output quality of the coating. QC technicians are checking to ensure the parts are free of visual defects, and everything meets the expectations we set with the customer from the beginning. This includes paying special attention to critical and machined surfaces, weld joints, tortuous pathways, etc.
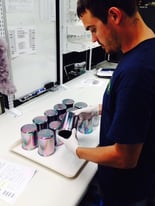
Certification - Once parts pass inspection and are packaged, they are certified compliant to the specification and/or other requirements as stated on the purchase order. SilcoTek's coatings are compliant with other regulatory requirements such as REACH and RoHS32, as well as company-wide management system standards such as ISO 9001.
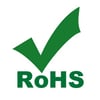
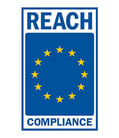
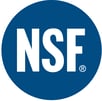
SilcoTek's coatings do not require MSDS/SDS sheets and are compliant with many important standards including:
- RoHS 3
- REACH
- California Prop 65
- NSF
- USP Class VI
- SDS Exempt
Click here to view relevant coating compliance statements, SilcoTek also follows the Copy Exactly! protocol for semiconductor customers.
Making the Grade
SilcoTek's coating process is designed to make customers say "wow" when they see how their newly upgraded parts look and perform. We involve the customer from the beginning to ensure our process is optimized to meet their expectations. If it isn't, we work with them to produce the best coating possible for their application.
Want to learn more about how SilcoTek can improve the performance of your products? Click here to view our process overview. You can also subscribe to our email and blog or follow us on LinkedIn.
