This week, we wanted to get back to some of the basics of SilcoTek's coating technology. Why can coated parts from SilcoTek display different colors? Let's delve deeper into the reasons behind specifying a range of thickness for Chemical Vapor Deposition (CVD) coatings rather than a specific value and what causes color variations.
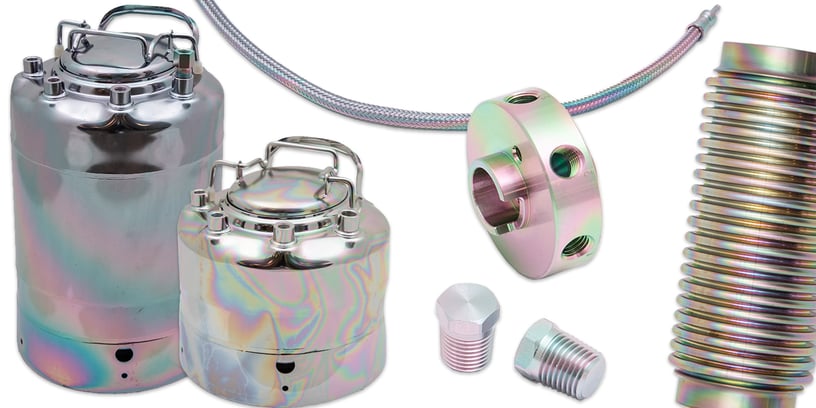
Why are SilcoTek Coatings so Colorful?
The colors of SilcoTek’s coatings are the result of light absorption and/or refraction through the thin film of the coating on a substrate. A slight variation in the thickness of the coating (a few nm) can result in observable changes in color. This process of light absorption and/or refraction gives our coatings their signature rainbow appearance.
Even though visual inspection is a crucial step in our quality control process, SilcoTek's coatings are certified based on quantifiable thickness measurements taken with SilcoTek’s F20 thin-film analyzer. It is a bench top tool that can be configured to measure thin film thicknesses (30Å to 350 mm), optical constants such as refractive index, extinction coefficient and transmittance. It is primarily used by SilcoTek as a quick, accurate and non-destructive way to measure surface thicknesses and to assure consistent coating quality. The analyzer relies on the refraction of light as it passes through a thin surface, reflects off the base surface, and then passes through the coating again. The instrument measures the change due to refraction and correlates that change to thickness standards. The base material, the surface roughness, and coating refractive index can play a big part in the effectiveness and reliability of this measurement technique.
Coating Families
There are currently 3 coating categories, or families, that we offer: Silicon, Silicon Oxide, and Silicon Oxynitride. Each family includes different chemistries that result in different looking coatings. In the Silicon family, we have SilcoNert®, Silcolloy®, and SilcoKlean®. The Silicon Oxide family includes Dursan® and Dursox®. Siltride® is currently the only coating we have in the Silicon Oxynitride family.

In the Silicon Oxide family, Dursan’s light refraction properties (seen above) correlate with a coating thickness between 400 and 1600 nm. The refraction properties of the Dursan coating process are more subtle than SilcoNert (below), making it easy to distinguish between the two.
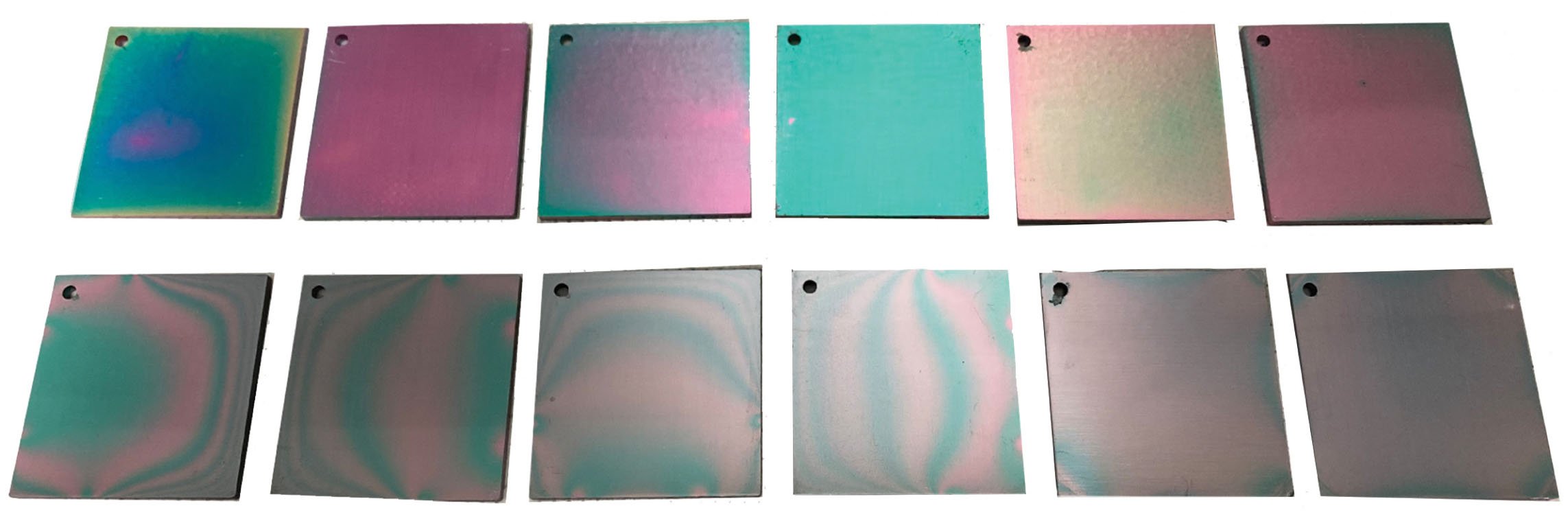
In the Silicon family, SilcoNert’s light refraction properties above correlate with a coating thickness between 100 to 500 nm (from right to left: thin to thick). The light spectrum produced by the SilcoNert coating process is more vibrant than Dursan and includes deep blues, purple, green, and gray. The coupons shown above are highly polished, resulting in a bright color spectrum. Rough and unpolished steel surfaces will subdue the colors.
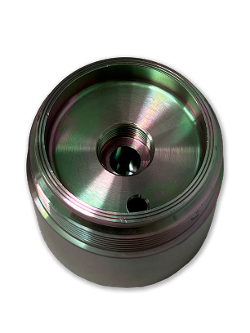
In the Silicon Oxynitride family, Siltride's coating thickness specification is between 500 and 2,000 nm. As shown in the images above, Siltride exhibits a vibrant purple and green coloration.
A few things to note regarding the coating appearance:
- As long as the coating meets our specification, the coating thickness (and therefore color) has no impact on surface properties such as inertness, hydrophobicity, and anti-fouling.
- One surface property that can be affected by coating thickness is corrosion protection. SilcoTek has written a white paper on this relationship that can be found here.
- All of SilcoTek’s coating processes have specified acceptable thickness ranges:
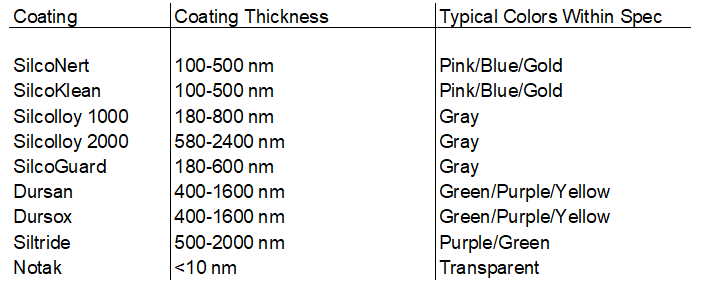
Coating Thickness Range and Color Variation
Variability in Coating Process
CVD is not unique to SilcoTek, but the investments and improvements SilcoTek has made to control process parameters like gas temperature, pressure, flow rates, and reaction kinetics to produce in-spec outputs across thousands of unique customer parts every day does make us different than other coating service providers. Daily variation in parts we receive from customers for coating means we have to modify our methods for each unique batch to produce coatings within specification. Given this inherent variability, specifying a precise thickness for CVD coatings would be impractical and very expensive to achieve for the typical customer who is not sending high OEM production volumes of parts for us to coat. Later, we discuss how we are capable of producing consistent thicknesses economically for these high-volume scenarios.
Complexity of Substrate Surfaces
The surfaces onto which CVD coatings are applied can vary significantly in their geometry, roughness, and composition. For instance, a substrate with a smooth, polished surface will likely receive a more uniform coating compared to one with a rough or irregular surface texture. Additionally, internal features such as blind holes or narrow channels within the substrate can present challenges in achieving uniform coating thickness. Thus, specifying a range allows for accommodating such variations in substrate surfaces.
Optimization of Process Parameters
CVD coating processes often involve a delicate balance of process parameters to achieve the desired coating properties while minimizing defects and variability. Parameters such as temperature and gas flow rates need to be optimized to ensure adequate coating coverage and adherence without causing issues such as delamination or excessive thickness variations. Specifying a range of thickness provides flexibility in adjusting these parameters to optimize coating quality and performance.
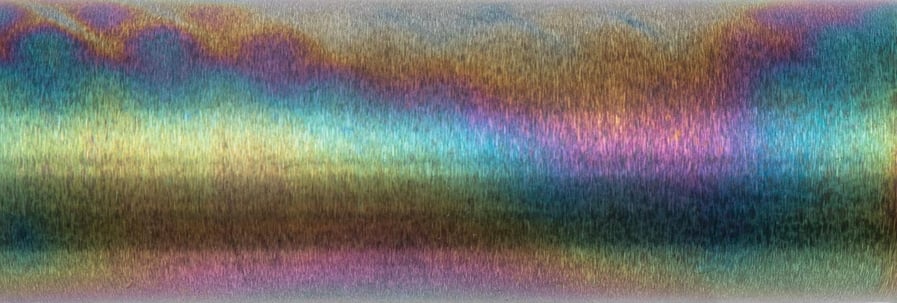
Color variation such as what is shown above is common for thin film coatings at sub-micron thickness. Typically, these nanometer-scale variations in thickness do not have any negative performance impact. However, SilcoTek has and continues to invest heavily into process engineering and quality efforts in an effort to produce more consistent film thicknesses, thus reducing color variation. Coatings with color variation as shown above may be a result of an underlying substrate issue, or parts processed in a small batch without dedicated tooling designed to mount the parts in the optimal fashion.
Practical Considerations and Cost-Efficiency
While it may be theoretically possible to deposit CVD coatings with extremely precise thickness control, doing so would likely entail significant time, effort, and cost. The equipment and process modifications required to achieve such precision could be prohibitively expensive and may not justify the marginal improvements in coating performance for many applications. Therefore, specifying a practical range of thickness balances the need for performance with considerations of cost-efficiency and feasibility.
Quality Assurance and Consistency
By specifying a range of thickness, manufacturers can establish quality control measures to ensure that coatings consistently meet or exceed performance requirements. Quality assurance protocols, including in-process monitoring and post-coating inspection, can help detect and mitigate variations within the specified range, thus ensuring consistent product quality and reliability.
Can SilcoTek Produce Coatings with Consistent Colors?
Yes, SilcoTek is able to achieve much more consistent thickness outputs (and therefore, colors) by receiving standardized batch sizes of customer parts and manufacturing custom-designed tooling in-house for mounting parts in a repeatable manner. This is costly and more challenging at low part quantities, but is achievable and more economical for production volumes, although very slight color variation is still possible. For example, SilcoTek developed a highly controlled, specialized coating process for the sintered stainless steel filters or “frits” shown below used in liquid chromatography columns. SilcoTek coats thousands of these frits at one time in controlled batches with custom tooling built by SilcoTek’s engineering team designed specifically to produce an optimal coating on frits. Certain specialized applications may require extremely precise control of thickness with virtually zero allowable variation, in which case SilcoTek can work closely with customers to develop a specialized process. However, customers should be aware that this can substantially increase coating costs.
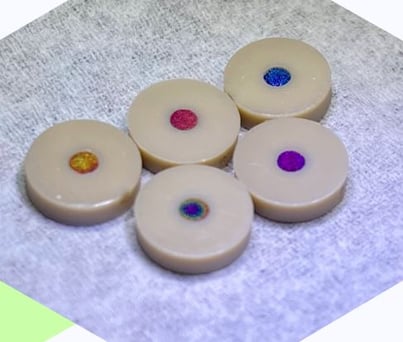
In summary, specifying a range of thickness for CVD coatings allows for practical considerations, process optimization, and quality assurance while accommodating the known variability in the coating process and substrate surfaces. It strikes a balance between performance requirements, cost-efficiency, and manufacturing feasibility, ultimately ensuring consistent and reliable coating performance across different applications.
Have questions about our coating's appearance or thickness?
We'd love to hear from you!