*
Well we're just about done with our series on how to calculate the cost of inert coatings. First we bored you to death with factors to consider when estimating coating costs. Next we piled on with a brain searing discussion on estimating coating cost benefits. Now it's time to party because we're pulling it all together by doing a sample cost calculation.
But first I'll need to ask forgiveness. I did not run a model estimating the cost of every factor imaginable for every industry. (I have a life you know...) My example cost calculation is based on a few situational and basic assumptions which I applied to a handy dandy spread sheet and voila, a cost benefit analysis. Interested in running a cost estimate of your own? You too can have this dandy calculator for the low TV introductory price of $19.95 (Ginsu knives not included...) OK, the calculator is free just click the box below if you really want to run a coating cost model...
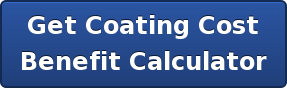
Here are assumptions and background for the model.
Background
A small contract lab is having trouble running sulfur analysis on their GC. The lab tech is having some nagging problems with sulfur loss. Nothing too bad, the tech spends maybe 10 minutes a day massaging results. Runs are slow and once a day the tech needs to rerun the low level sulfur test which takes about 45 minutes. The lab has 10 gas chromatographs running sulfur, most clients are in the local Houston, TX market. The alert lab tech discovered a fitting seems to be adsorbing and desorbing the sulfur sample, distorting results as the day progresses. The analyst searched on line for a sulfur inert surface and discovered SilcoTek® coatings. After spending a few minutes on line and contacting our Technical Service Team, the analyst was convinced SilcoNert® 2000 was the answer to his problem. Off to the lab supervisor and purchasing to buy the coating. But a wrench was thrown into the process. The supervisor and purchasing agent are under strict cost controls and are not sure they want to spend the time and money for coating the fitting.
Enter the spreadsheet.**
After some gnashing of teeth, the analyst went back to the drawing board. Further exploration of the SilcoTek® website revealed a blog post on the cost benefit of our coatings. The sample spreadsheet provided some insight into ways to justify a coating purchase. After evaluating and quantifying the cost and benefits of the coating, the analyst discovered that the cost of the coating was more than justified. In fact the total return on investment was an impressive $51,000. After presenting the results, the team partied like it was 1999. (I can dream can't I?)
The assumptions:
Note that not all factors were evaluated, some were not justified relative to the cost of purchasing one fitting. You'll want to include more factors as the job scope or risk increases. Assumption details are listed in the comment section of the cost calculation spreadsheet. Some of the criteria can be seen as splitting hairs and have some overlap. Depending on the granularity of the project details, some factors can be ignored or combined into broader estimates. For simple calculations, it's best to base estimates on simple cost factors like yield, sales increase, labor cost, material cost etc. But for a major projects that can span years for evaluation and process integration, you'll want to thoroughly check all cost/benefit factors (and probably more than listed, depending on your industry).
Estimating Cost And Benefit***
In summary, factoring in estimated and actual cost, the total for acquiring the coated fitting (including the fitting) will be about $562 give or take... The benefit? A whopping $51,000! OK, you say, you're making this up, so the return on investment is going to look fabulous any way you slice it. There may be bias in this model, but I invite you to run your own numbers using any reasonable assumption and you'll see that the coating cost is well justified. The big saving here is the net productivity gain by avoiding one test failure. That 45 minute saving allowed the company to run 1 more test per day, a total of 260 tests per year; a real increase in capability at minimal cost to the company. The best part of the equation? The sales increase was the result of a test yield improvement, so no additional labor or materials were needed, so the $51K will be going directly to the bottom line! I love a good cost reduction victory!
Want to reign victorious over your bottom line? Check out our coatings or read our case studies. Better yet, become a case study!

*Image Credit: Daily Mail
** Image Credit: Open Clipart
*** Image Credit: Clipartbest.com