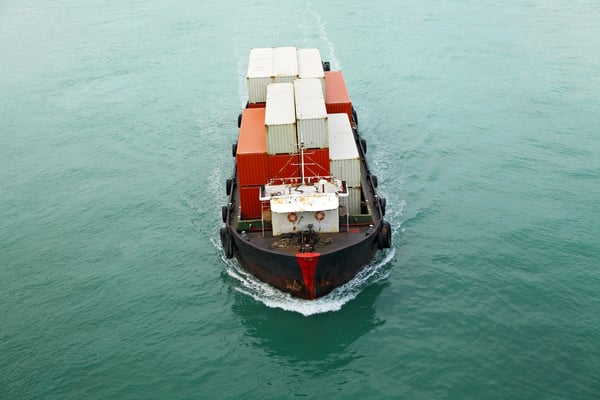
In 2016 the UN International Maritime Organization (IMO) took a stand for cleaner air by setting stricter standards for sulfur content in fuel oil used to power global shipping. Don't care about shipping? Don't think this new standard has anything to do with your business? You're sadly mistaken.
A May 2018 article in Marine Link Magazine "New Rules on Ship Emissions Herald Sea Change for Oil Market" by Libby George and Ahmad Ghaddar discusses the potential impact of a new sulfur emission regulation promulgated by the UN IMO. After reading the article, I realized the far reaching impact the regulation will have not only on global shipping but how this regulation could impact everything from the price of an airline ticket to the cost of my Amazon Prime!
In this blog you will learn:
- How the New IMO rule could cost you more for shipping
- How demand for low sulfur sweet crude could increase
- How refinery capacity for production of marine gas oil will be stretched to the limit
- Opportunities for better sulfur management and detection systems
|
About the IMO rule and global shipping
About 3 million people world wide die every year from air pollution. One of the primary killer pollutants is sulfur emissions from buring fossil fuels. To combat the world air pollution epidemic and to reduce sulfur emissions, the UN International Maritime Organization set stricter standards for sulfur content in fuels in an effort to improve world air quality. By 2020, the regulation requires the use of 0.5% sulfur fuel oil (down from the current permitted 3.5% sulfur). Vessels that continue to burn 3.5% sulfur fuel will be required to install exhaust scrubbers. Violators could find themselves in hot water including:
- Fines
- Insurance coverage problems
- Potential declaration the ship "unseaworthy", preventing it's use on the high seas

Options
The shipping carrier has a few options regarding the new IMO regulation. They can choose to pay the higher fuel costs associated with purchasing low sulfur distillates. They can install scrubbers on the ship. Or they can cheat and risk essentially losing the vessel to an unseaworthy declaration if caught.
None of the options for shipping operators are particularly compelling. Demand for distillates like marine gasoil will likely spike. Given the limited supply of distillates, prices for low sulfur distillates could result in a fuel cost increase of $6K to $20K per day. That could mean billions in increased costs for shipping. Scrubbers would allow a ship operator to continue to burn the less costly high sulfur fuel but entails an expensive scrubber installation. Scrubbers can cost millions per ship which can stress the capital budget. More importantly there are only so many companies with the expertise to build and install a scrubber system on a large vessel. The overall capacity for scrubber installations is estimated to be about 500 vessels per year. At that rate it would take about 100 years to convert all 60,000 vessels. Not a realistic option. Speaking of not realistic, cheating is not a viable option for most major shipping firms. The risk to reputation and the bottom line is too great, especially considering new "black box" emissions technology that could provide real time sulfur emissions data.
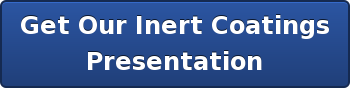
Why is this a big deal? It all has to do with the fuel source, the refinery.
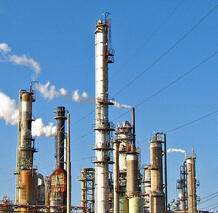
Global shipping is the cornerstone of world trade. Approximately 90% of manufactured products are shipped by bulk carrier including consumer products, equipment, and crude oil. About 60,000 vessels burn 4 million barrels of fuel oil a day while plying the seas. That's about the equivalent production of the number 4 oil producer and about 40% of production in the US. So a change in sulfur requirement is not trivial to world markets and refineries, here's why.
Not all oil is the same and a refinery is not just a refinery. The sulfur content in crude oil varies generally by region (there's variation in individual wells but in general, regions produce sweet (low sulfur) or sour (high sulfur) crude. For example Saudi Arabia oil is generally lower in sulfur content while Venezuela crude contains higher levels of sulfur. Refineries exist to process crude oil into petroleum products like gasoline, jet fuel, or marine fuel oil. It would be costly and inefficient to build a refinery to be able to process all types of crude or crude products so they specialize in a particular type of crude and petroleum products. For example, a refinery may be constructed to process a light sweet crude (a higher cost crude but cheaper to process into petroleum products) or the refinery owner will design the refinery to process higher sulfur crude (lower cost crude but higher processing cost). It all depends on the complex cost calculation of refinery location, their cost structure, the deal they have with the crude producer, proximity/shipping costs, etc.
I'm getting bored, what's all this got to do with my Amazon Prime?
OK, OK I'll get to the point! There's only so much low sulfur distillation capacity in the world. Just as there's only so much low sulfur crude. The expected shift to low sulfur fuel will significantly increase demand which, you guessed it, will increase the price of those fuels. The price pressure will spread to diesel, jet fuel, and perhaps gasoline (depending on the refiner's crude source). How will this effect shipping costs? Let's use Amazon as an example. Let's say I've just ordered some great man gadget from Amazon, using my Amazon Prime account. The gadget shipped from China by boat (first potential for added cost due to higher marine fuel prices). The package arrived in LA and is flown to the Eastern distribution center (second area for an increase due to higher jet fuel cost), shipped by truck to local distribution center and (more cost due to higher diesel prices) and finally delivered to my door (again higher diesel cost). All that low sulfur fuel demand will surely increase shipping costs and ultimately will lead to an increase to my Prime account! Think of something you buy that does not depend on fuel costs. Not many things, maybe happiness, but you can't buy that...
The Importance of Low Level Sulfur Analysis
All the extra cost and effort will be worth it for one important reason. Our air quality will improve!
The importance of low level sulfur analysis has never been more clear. Testing fuels and monitoring air quality is a vital pillar to enforcing clean air regulations. Unfortunately stainless steel sampling surfaces will adsorb or retain sulfur. Sulfur adsorption can cause multiple problems for the refinery including:
- Regulatory emissions compliance
- Poor product quality (if the sulfur content of your fuel or refined product is higher than you think it will cost you in the long run and will make an angry customer)
- Calibration problems. Sulfur loss due to sulfur adsorption will cause calibration errors.
- Higher cost. Sulfur contamination can damage catalysts, causing increased catalyst replacement cost.
Improving sulfur analysis = better products and emissions compliance.
To prevent loss of sulfur during testing, coat the entire sample flow path with SilcoNert® or Dursan® coatings. SilcoNert and Dursan are barrier coatings that act as an inert non reactive surface. A non reactive surface ensures that all the sulfur sample makes it to the detector. When all the sulfur is completely and consistently transported to the detector, calibration is easier and the test is accurate and repeatable. Even after 14 days, sulfur samples remain unchanged as seen in the 14 day stability test (below left). The uncoated sample flow path (below right) completely adsorbed the sulfur sample within hours of exposure, resulting in test failure or poor product quality.
Why is sulfur hard to sample and detect?
Because sulfur and sulfur compounds tend to stick to materials commonly used in sample flow paths. If the sulfur gets trapped in the flow path, the instrument can't accurately record the data, making control of scrubbers and processes difficult at best. Here's an example of how sulfur can get lost in a tube. Shell and O'Brien conducted a study where a sulfur compound was injected into a tube. Then they waited for the detector at the other end to "see" the sulfur. They waited... and waited... and finally after 90 minutes some sulfur hit the detector! Here's a graph of the test results.
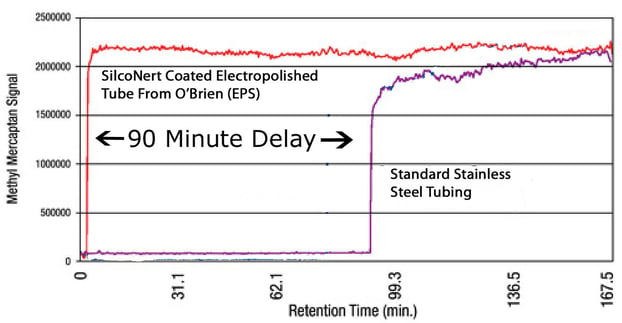
The first red line is a graph of the sulfur response when that tube is coated with SilcoNert®. Under the same test conditions the response is almost immediate! Virtually no sulfur was lost in the tube. When all the sulfur makes it to the detector, the plant, ship or refinery can accurately monitor and control emissions and process; making for a better product while minimizing sulfur related air pollution.
Read The Entire Sulfur Detection Study By Shell and O'Brien Analytical
How big a problem is sulfur adsorption? Well if we look at the US EPA Tier 3 standard, a 10ppm sample will be completely lost in a relatively short length of sample tubing. If the sample were exposed to a high surface area metal (for example if a sample were filtered through a sintered metal frit), most if not all of the sample would be adsorbed onto the surface.
Here's an example of how dramatic sulfur loss can be. A sample of hydrogen sulfide, carbonyl sulfide, and methylmercaptan were injected onto a GC column through a 3 inch long stainless steel liner. During the brief exposure to the stainless steel liner, the sulfurs adsorbed onto the stainless steel surface. The adsorption was so complete that the detector was not able to see any hydrogen sulfide (H2S) or mercaptan (image below). If we rerun the test using a SilcoNert 2000 coated liner, the H2S and mercaptan are clearly picked up by the detector. (second graph).
How do SilcoTek® inert silicon CVD coatings improve sulfur sampling and air quality?
Our inert CVD coating, SilcoNert®, provides a barrier between the sample and the reactive stainless steel surface. That allows the sulfur or NOx sample to pass right through the flow path without interacting with the surface, delivering the entire sample to the detector. Our inert coating benefits include:
Want to lean more about analytical sampling and how surface science can improve results?
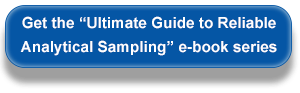