Coating Certifications & Compliance Statements
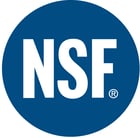
SilcoTek's chemical vapor deposition (CVD) coating process is unlike any other, but it is especially unique because of its environmentally friendly nature. There are two byproducts from this process: water and sand.
Each coating's composition can be found on their data sheets.
SilcoTek Compliance Statements and Coating Certifications
SilcoTek's official RoHS and REACH compliance along with SDS exemption statements are listed below along with coating certifications from relevant internationally-recognized agencies:
Safety Data Sheet (SDS) Exemption
SilcoTek® does not provide SDSs for our coatings as they are not hazardous chemical products.
SilcoTek’s state-of-the-art CVD processes deposit a thin (0.0005um – 2um) ceramic layer bonded to a customer’s substrate. The layer is comprised of elemental combinations of silicon, oxygen, and carbon, with no CFCs or other toxic chemicals.
Want to learn more about SilcoTek quality? Go to our Quality Systems Page.
USP Class VI
Dursan has been certified to meet USP Class VI standards for biocompatibility. USP Class VI is the most stringent materials testing for biocompatibility and assures that customers using Dursan in medical and pharmaceutical applications are using a truly biocompatible product.
Click here to view the Certificate.
NSF (National Sanitation Foundation) Certification
Our Dursan® coating is compliant with NSF/ANSI 51 and all applicable requirements. That means that it is safe for food contact and also meets the FDA's requirements for compliance. Dursan® is a high performance, versatile coating solution that provides corrosion resistance, durability, and anti-stick surfaces to the food and biomedical industries.
Click here to view our NSF Certificate.
California Proposition 65
SilcoTek® coatings do not contain chemicals which are listed on the state of California Safe Drinking Water and Toxic Enforcement Act of 1986, California Proposition 65. Proposition 65 protects California drinking water from contamination by chemicals known to cause cancer, birth defects, and other reproductive harm. The act requires businesses to inform Californians about exposure to these hazardous chemicals. The Proposition 65 chemical list can be found at:
https://oehha.ca.gov/proposition-65/proposition-65-list
Restriction of Hazardous Substances Directive 2015/863/EU (RoHS 3)
SilcoTek® coatings do not contain any of the following compounds at levels exceeding RoHS compliance limits: Cadmium; Mercury; Lead; Hexavalent Chromium; Polybrominated Biphenyls (PBB); Polybrominated Diphenyl Ethers (PBDE); Bis(2-Ethylhexyl) phthalate (DEHP); Benzyl Butyl Phthalate (BBP); Dibutyl Phthalate (DBP); and Diisobutyl Phthalate (DIBP).
SilcoTek® does not manufacture electrical/electronic products, devices, or equipment and is not required to CE-mark any outgoing shipments.
Registration, Evaluation, Authorization, and Restriction of Chemicals - Substances of Very High Concern (REACH-SVHC)
SilcoTek coatings do not contain any of the 250 REACH Substances of Very High Concern (SVHC) as updated by the European Chemicals Agency (ECHA) under the provisions of Regulation (EC) No. 1907/2006 of the European Parliament and of the council concerning the Registration, Evaluation, Authorization, and Restriction of Chemicals (REACH) per the ECHA 25-June-2025 and previous updates.
Persistent, Bioaccumulative, and Toxic (BPT) Chemicals under TSCA Section 6(h)
SilcoTek coatings do not contain any of the five PBT chemicals under TSCA section 6(h). As stated on the United States Environmental Protection Agency Website the five PBT chemicals include: Decabromodiphenyl ether (DecaBDE), Phenol, Isopropylated Phosphate (3:1) (PIP (3:1), 2,4,6-Tris(tert-butyl)phenol (2,4,6-TTBP), Hexachlorobutadiene (HCBD), and Pentachlorothiophenol (PCTP).
Minimization of Transmission of Transmissible Spongiform Encephalopathy (TSE) and Bovine Spongiform Encephalopathy (BSE)
SilcoTek does not use materials of animal origin in SilcoTek processes. In addition, SilcoTek coating services are all at temperatures above 250 degrees Celsius, which further reduces risk of any TSE or BSE contaminations. SilcoTek packaging of customer parts is able to be specified to further avoid any risk.
Latex
SilcoTek does not use latex materials. Gloves used by employees are nitrile-based. SilcoTek standard packaging of customer parts does not use latex.
Click here to download the compliance statement on TSE/BSE and Latex.
Conflict Minerals
3TG (Tantalum, Tin, Tungsten and Gold) are not added or used in the coating process.
Click here to download the conflict minerals reporting template.
Medium chain chlorinated paraffins (MCCPs) and long chain perfluorocarboxylic acids (LC-PFCA)
SilcoTek coatings do not contain medium chain chlorinated paraffins (MCCPs) or long chain perfluorocarboxylic acids (LC-PFCA).
Click here to download the compliance statement on MCCPs and LC-PFCA.