When considering the purchase of a chemical vapor deposition (CVD) coating, it’s natural to focus on the per-piece price. However, a more effective and strategic approach is to evaluate the total value the coating delivers - across performance, reliability, operational efficiency, and long-term cost reduction. Let's outline key considerations and strategies for rationalizing and optimizing your CVD coating investment from SilcoTek.
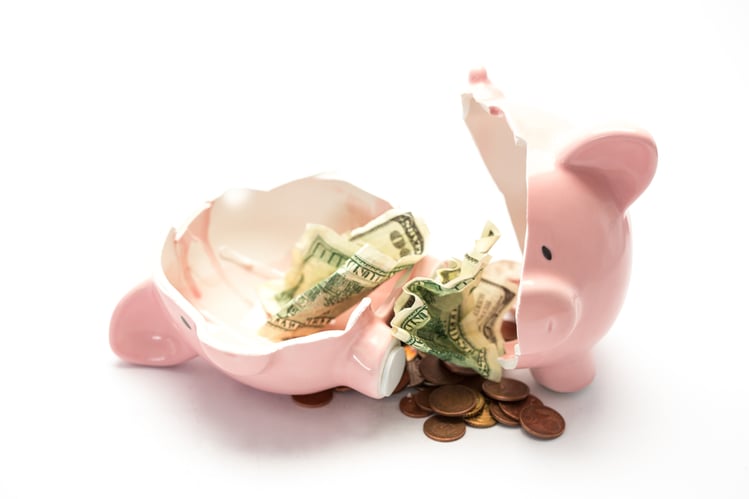
1. Understand What Influences Coating Cost
The price of a CVD coating is determined by a variety of factors beyond just the surface treatment itself:
-
Part size and material: Larger components and specialty materials such as ceramics or aluminum typically require more time and resources to process.
-
Order quantity: Volume plays a significant role in pricing. Higher quantities often unlock substantial per-part discounts.
-
Geometries and handling: Complex parts with blind holes or tight tolerances may require custom fixturing or extended engineering time.
-
Surface preparation: Components that need specialized cleaning, citric acid passivation, or other preparation prior to coating will generally incur higher costs.
-
Logistics: Premium or expedited processing, express shipping, and issues with import/export can all increase the total cost of coating services.
Understanding these variables allows procurement and engineering teams to identify opportunities to reduce cost without compromising performance.
2. Plan Orders Strategically
To reduce costs and streamline turnaround time, it is advisable to order in consolidated batches rather than individual parts. Even modest increases in quantity can significantly lower the per-part price.
Additionally, planning ahead to avoid expedited coating or shipping fees is a critical cost-saving measure. Coatings typically require about 10 business days to process. Building lead time into your production schedule or implementing a stocking system can prevent last-minute orders and associated surcharges.
3. Evaluate Coating Cost Against Alternatives
It’s important to benchmark CVD coating costs not just against raw or uncoated components, but also against alternative materials or surface treatments. For instance:
-
Coated stainless steel often performs similarly to more expensive alloys in corrosive or inert environments, at a fraction of the cost.
-
Competing coatings may appear less expensive, but differences in coating thickness, quality control, and functional durability should be carefully assessed.
-
Redesigning a part to avoid coating may result in higher material or machining expenses over the long term.
In many cases, the total lifecycle cost of a coated part is lower than alternative options, particularly when factoring in performance reliability and reduced replacement frequency.
4. Quantify Benefits to Justify Investment
CVD coatings often deliver quantifiable improvements in throughput, product quality, and operational uptime. For example, one customer using a coated GC fitting was able to reduce downtime between runs, resulting in 260 additional tests per year and more than $50,000 in additional lab revenue.
Other benefits may include:
-
Reduced frequency of part replacement due to corrosion or contamination
-
Fewer process interruptions and maintenance events
-
Greater consistency and accuracy in analytical or reactive environments
-
Enhanced performance that enables product innovation or regulatory compliance
By framing coating costs as investments rather than expenses, decision makers can more accurately assess return on investment.
5. Streamline Logistics and Operations
SilcoTek offers several support mechanisms to help customers reduce overhead and avoid delays:
Coordinating shipments and consolidating purchase orders can further reduce administrative and shipping costs.
6. Communicate Requirements Clearly
Providing detailed part information - including drawings, material composition, cleaning history, geometry complexity, and special handling requirements - at the quote stage improves turnaround time and reduces the likelihood of processing delays.
Discussing any unique performance conditions (e.g., exposure to high temperatures or aggressive chemicals) upfront enables the coating team to determine the most efficient and effective process for your specific needs.
CVD coatings offer significant long-term value by enhancing material performance, reducing operational disruptions, and enabling cost-effective alternatives to high-performance alloys. By understanding the factors that influence coating costs - and by planning, batching, and communicating effectively - companies can rationalize their coating investments and achieve meaningful cost savings.
To learn more or to request a detailed quote, contact SilcoTek’s applications and technical support team. We’re here to help you find the most efficient path to improved performance.
Have questions? Contact our team today!