Introduction to CVD Coatings
Chemical Vapor Deposition (CVD) is a process that creates thin, durable coatings on a variety of surfaces. These coatings play a critical role in industries ranging from semiconductor, analytical, life sciences, or energy, where high-performance, precision coatings are essential. This blog post will guide you through the CVD process, explore its benefits and challenges, and offer insights on how to maximize the advantages of CVD coatings for your specific applications.
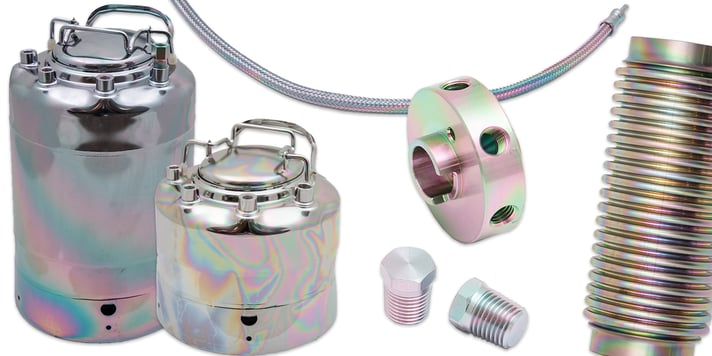
Understanding the CVD Process
CVD involves the reaction of a volatile precursor gas in a heated chamber which is under vacuum. As the chamber reaches the required temperature, the precursor decomposes, and the desired coating material deposits onto the substrate's surface. This process ensures that the coating forms evenly across all exposed areas, including intricate internal geometries.
For example, using a precursor like trichlorosilane (SiHCl3), the gas is introduced into the chamber where it breaks down upon heating, leading to the deposition of silicon on the surface. The by-products, such as chlorine and hydrochloric acid, are safely vented and scrubbed in accordance with regulatory requirements. The CVD process is highly controlled, allowing for precision in coating thickness and uniformity.
Here's our process video to explain how the process works:
Characteristics and Benefits of CVD Coatings
CVD coatings are known for their ability to be applied to a wide variety of materials, including metals, ceramics, and glass. We can coat many popular metals such as Titanium, Hastelloy, Monel, and Inconel. Check out our material compatibility guide to see what other substrates we can coat. The process can coat complex surfaces with precision, including internal features and fine details that other coating methods might miss. The TEM EDS image below shows a cross section of the coating (red) applied to the substrate surface (blue). The profile shows a uniform silicon layer which will minimize disruption to flow path surfaces.
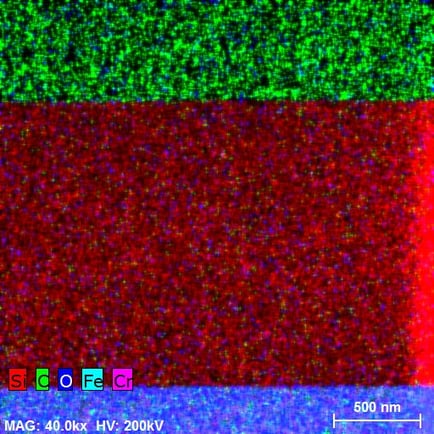
Another common coating used in many industries is spray-on PTFE coatings. In comparison to CVD coatings, you can see in the illustration below that CVD is able to coat the entirety of the part, while PTFE coatings only cover what is in the direct line-of-sight. Because CVD coatings are non-line-of-sight, you can be assured that there won't be any exposed substrate that could cause reactive sites and compromise your parts. PTFE coatings also contain PFAS, which have been proven to be toxic to our health and environment, resulting in strict regulations. Our coatings have significantly higher temperature stability, flexibility, and density compared to PFAS coatings like PTFE.
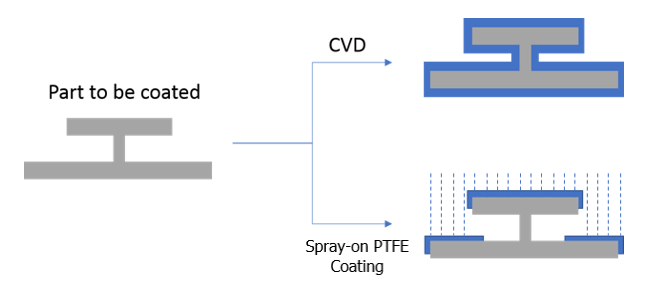
SilcoTek’s CVD process effectively coats the entirety of sub-micron filter pores without clogging them, drastically reducing unwanted interactions between process fluids and the metal or ceramic filter material. Filters have extremely high surface area and are thus prime sites for corrosion, catalysis, and other surface interactions that cause premature system failures, excessive maintenance, and inaccurate or untrustworthy analytical results. As you can see in the cross section photo below, SilcoTek's coating process can coat even the pores of very small frits.
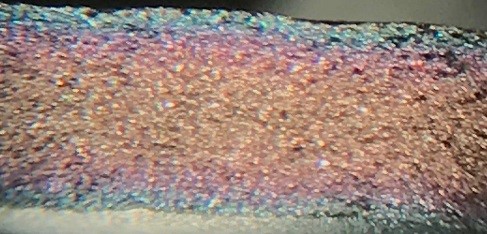
Another significant advantage of CVD is its capacity to withstand extreme temperatures and thermal cycling, making it suitable for applications that require durability in harsh environments.
The bond formed during the CVD process is exceptionally strong, ensuring that the coating remains intact even under stress. Additionally, the precursor gases used in CVD can be customized to achieve specific coating properties, such as enhanced lubricity, corrosion resistance, and chemical inertness.
Challenges of CVD Coatings
Despite its many benefits, CVD is not without its limitations. The high temperatures required for the process can restrict the types of materials that can be coated. We are not able to mask any surface, as CVD coats all exposed surfaces. Moreover, the size of the parts that can be coated is limited by the dimensions of the reaction chamber. Finally, SilcoTek's CVD is an off-site process, requiring parts to be sent to our facility in central Pennsylvania, USA for coating.
Maximizing CVD Coating Performance
To maximize the benefits of CVD coatings, several factors must be considered. Fixturing during the deposition process plays a crucial role in ensuring consistent coating quality. Custom fixtures are often designed to hold parts securely during the coating process, preventing damage and ensuring uniform thickness. Proper fixturing also enhances surface preparation, which is vital for optimal adhesion and overall coating quality.
The condition of the surface being coated significantly impacts the outcome. Smooth, passivated surfaces tend to produce more uniform coatings, while rougher surfaces may result in slight variations. In addition to coating services, SilcoTek offers Citric 2 passivation per ASTM A967 standards. Passivation enhances the surface chemistry and inherent corrosion resistance of stainless steel by removing free iron that causes rouging, rust, and undesirable surface interactions. Semiconductor, biopharmaceutical, medical, and other industries where purity is paramount rely on citric acid passivation on stainless steel and other alloys. Additionally, the configuration of the part, such as narrow bores or blind holes, can affect coating thickness due to variations in gas flow within these confined areas. It’s important to consider the base material as well, as different materials can influence the coating rate and uniformity, particularly if the surface has been oxidized or contaminated.
Finally, achieving the ideal coating involves balancing process time, cost, and quality. Allowing sufficient lead time ensures that the coating is optimized for your specific application, providing the best possible performance. If lead time is a concern for your application or situation, talk to our team about our expedite options!
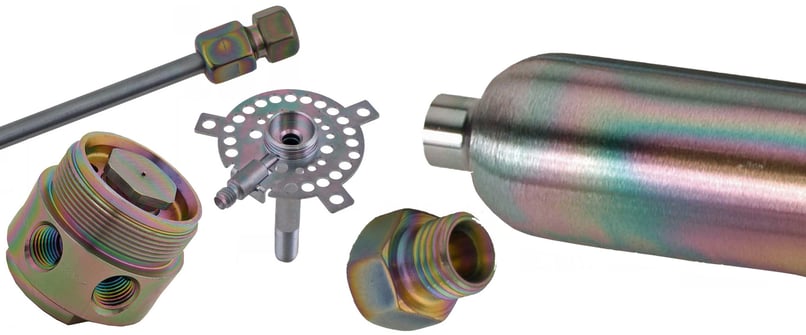
Chemical Vapor Deposition is an unique, versatile, and powerful technique that enhances the surface properties of materials across a wide range of applications. By understanding the CVD process and considering the factors that influence coating performance, you can achieve high-quality, durable coatings that meet the harsh demands of your industry.
Please reach out to our knowledgeable team for more information!
Check out our Case Studies that solve real world problems for our customers. How can SilcoTek's CVD coatings help your processes?