Current market conditions have created significant delays in the supply chain for stainless steel tubing. Additional post-manufacturing processes like surface treatment are often required but inevitably extend lead times. As a result of long lead times for electropolished tubing, many customers have asked us, "can I use your SilcoNert coating instead of electropolishing?" We explore that question in detail below and prove that, in many cases, the answer is an emphatic "yes."
Solve Supply Chain Challenges with Better Surface Technology
Electropolishing is an electrochemical technique used to improve metal surfaces. Metal parts are placed into a fluidic bath that an electrical current is then passed through. This creates a smooth and passive surface that is more desirable than stainless steel in applications like semiconductors, medical devices, analytical chemistry, pharmaceuticals, and more.
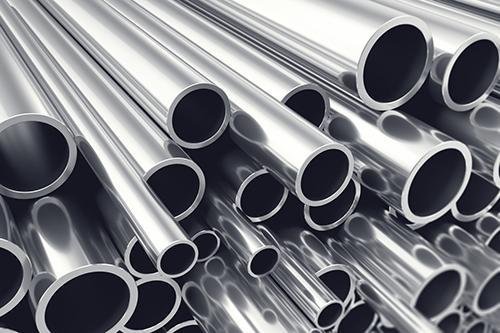
Engineers in these industries require special surface modifications to improve the compatibility and performance of preferred materials of construction like stainless steel. Electropolishing has historically been considered a solution by default. However, today, EP often carries extreme lead times which lead to higher costs in the form of expedite fees, lost production yield, and customer disappointments. Additionally, although improved over unpolished metal, EP still leaves exposed metal throughout the flow path which leads to catalytic activity, adsorption, and subsequent problems in chromatography, pharmaceutical manufacturing, semiconductor gas delivery, and many other sensitive applications.
SilcoNert CVD coatings on stainless steel provide superior chemical inertness, corrosion resistance, and surface properties than electropolishing. SilcoTek® coats high volumes of parts within a few weeks for any customer, large or small. We partner with leading manufacturers across the globe to stock SilcoNert-coated tubing, valves, fittings, and more.
Can SilcoTek CVD Coatings Replace Electropolishing?
Even better, the data below prove that SilcoNert can replace electropolishing and outperform it. SilcoTek’s gas phase coating process uniformly deposits a thin layer of inert amorphous silicon across 100% of any part surface, even complex and torturous geometries such as micron-sized filters. The SilcoNert coating process is a universally acknowledged surface solution for creating a chemically protective metal-free barrier to improve inertness, reduce the effects of corrosion and ion leaching, and increase hydrophobicity. These coatings are written into material specifications for the world’s largest public and private organizations to enable accurate detection of trace impurities, extend the lifetime of critical components, and improve the purity of metal surfaces.
Corrosion
The coating provides excellent corrosion resistance, protecting the underlying material from degradation caused by harsh chemicals, moisture, or corrosive gases. This extends the lifespan of the components and ensures the integrity of the transfer system over time. SilcoNert 2000 provides a good corrosion barrier for 5% HCl, as shown in the chart below each coupon type. The SilcoNert coated coupons show over 100x better corrosion protection than the EP coupons.
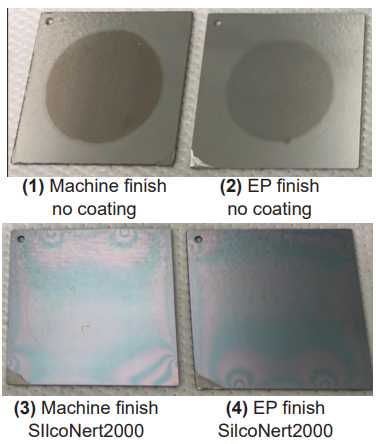
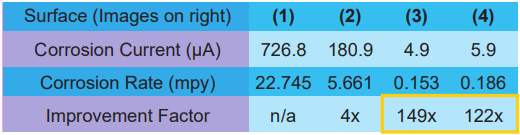
Inertness
SilcoNert 2000 creates an inert surface, reducing the chances of chemical reactions or adsorption, making it ideal for handling sensitive materials or samples without contamination or reaction. For this experiment, electropolished tubing (Fig. 5) and SilcoNert 2000 non-electropolished coated tubing (Fig. 6) was filled with 100 psi nitrogen that contained 20 ppb hydrogen sulfide (H2S), carbonyl sulfide (COS), and methyl mercaptan (MeSH). It was monitored through days 0, day 1, and day 4, as shown in the chromatograms below. The electropolished tubing in Figure 5 shows an immediate loss of signal for all reactive materials with the yellow box area of interest showing a complete loss of MeSH signal on Day 1. When compared to SilcoNert 2000 nonelectropolished coated tubing in Figure 6, all reactive materials still maintain a nearly identical signal from Day 0 to Day 4. These results highlight the impressive inertness needed for the accurate detection of trace impurities over time.
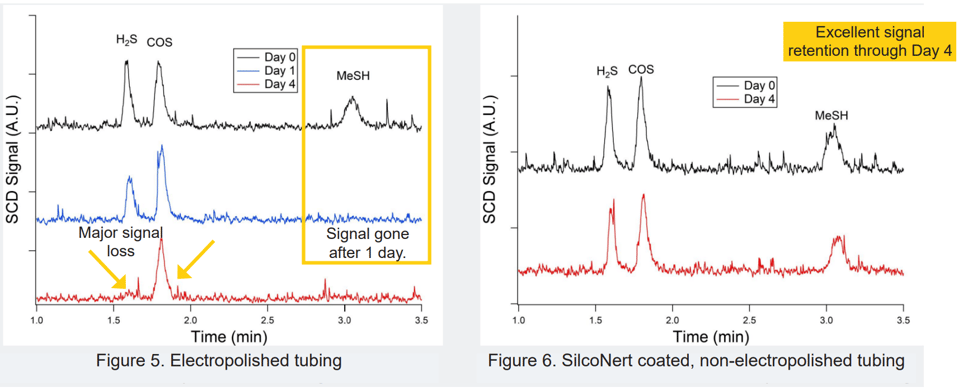
Improve Hydrophobicity, Boost Dry Down Performance
The SilcoNert coating technology lowers the surface energy of materials, improving the hydrophobicity and reducing the adhesion ability of liquid molecules to the surface. This allows for a faster dry down time which is necessary in analytical instruments or applications where maintaining sample purity and minimizing carryover is crucial.
Figure 8 (is Figure 7, 5x zoom) shows electropolished surfaces have a nearly immeasurable impact over nonelectropolished surfaces when quantifying moisture content over time. The SilcoNert 2000 non-electropolished coated surface cuts dry down time in half, saving over 15 minutes in comparison to electropolished surfaces and 25 minutes to untreated surfaces. The improved hydrophobic SilcoNert technology will allow users to save time while maintaining a high standard of purity.
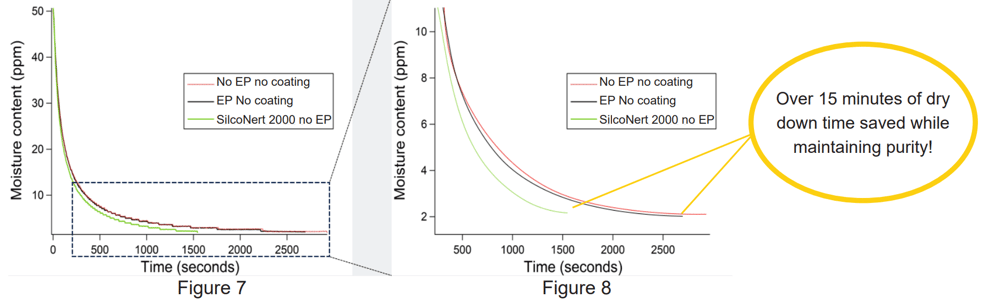
What is the cost difference?*
SilcoTek’s SilcoNert coating significantly improves the chemical inertness, corrosion resistance, and moisture dry-down performance of stainless steel tubing and thousands of other products. EP is commonly specified with the intent of achieving similar improvements, but new data prove that SilcoNert outperforms EP in both performance and, as illustrated below, price.*
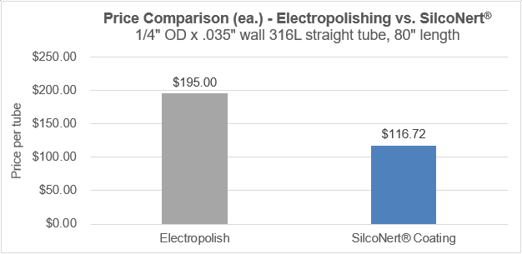
SilcoTek can apply our game-changing SilcoNert coating to both coiled and straight tubes for any customer, typically at better prices and lead times than electropolishing services. Data gathered in March 2024 (above) show that SilcoNert is over 5x less expensive per foot than EP for coiled tubing, and nearly 1.5x less expensive than EP for straight tubes.
Interested in learning more about SilcoNert's capabilities and how it compares to electropolishing? Talk to one of our coating experts!
*Price data gathered in March 2024 from multiple electropolishing service vendors in the United States and Europe. Prices subject to change at any time. Discounts may apply at longer lengths and/or higher quantities. This information does not constitute a formal quote from SilcoTek or any electropolishing service vendor.