On April 22nd, we will celebrate the 54th official Earth Day! With this celebration, we wanted to talk about how SilcoTek coatings can help us keep Mother Earth beautiful and sustainable for generations to come!
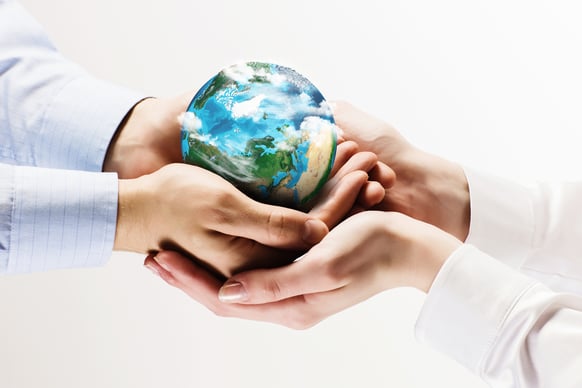
Did You Know?
- Earth Day wasn't nationally recognized until 1970, but had been in the works for several years at that point. In fact, it originated due to a book written by Rachel Carson, entitled Silent Spring, that sparked interest in environmental issues nationwide.
- The Environmental Protection Agency (EPA) was founded largely due to the public's interest in Earth Day.
- Earth Day is celebrated annually in 192 countries worldwide!
- There is an unofficial Earth Day anthem and flag:
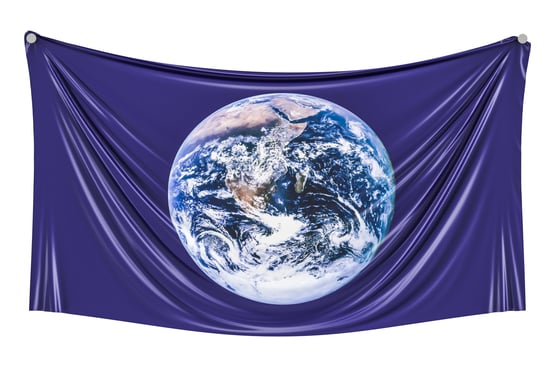
- Every Earth Day has a theme. This year's theme is Planet vs. Plastic, with a goal of reducing plastic production by 60% by 2040. On the topic of plastics, we wanted to weigh in on how SilcoTek can help!
So, how can SilcoTek help with these initiatives?
You may be asking yourself how a coatings company can be involved in keeping the Earth protected and contribute to a more sustainable future. Well, the answer is that our game-changing coatings are already being used in several applications that are making this task easier. From new PFAS legislature to air quality control to semiconductor sub-fab process improvements, our coatings are helping to shape the way environmental issues are quantified and brought to light.
The PFAS Predicament
Per- and polyfluoroalkyl substances (PFAS) are a hot-button topic these days with new regulations set in place at the beginning of 2024. They are prevalent in our daily lives, from cosmetics and non-stick cookware to other applications like weatherproof clothing. The wide-ranging use of PFAS has led to detectable levels in human blood, animal tissues, and the environment, prompting regulatory agencies like the EPA and ECHA to propose limitations on their usage.
Among the commonly used PFAS, PTFE (Teflon®) plays a significant role as a coating in industrial processes. However, the need for a sustainable alternative has never been more pressing.
Enter SilcoTek...
SilcoTek's Chemical Vapor Deposition (CVD) coatings allow for a shift towards sustainability and our coatings stand out as superior alternatives to PFAS. With benefits like an Earth-friendly composition, enhanced performance, chemical inertness, corrosion resistance, and exceptional adhesion, the switch to SilcoTek coatings will become more and more relevant. SilcoTek coatings are comprised of silicon, oxygen, carbon, and hydrogen - all fundamental elements of the Earth. In many environmental applications, temperature stability and corrosion resistance are key to proper detection. In addition to corrosion resistance, inertness, and temperature, SilcoTek coatings offer flexability that doesn't allow for flaking or reactive sites. The nature of the deposition process allows for all surfaces to be evenly coated, including tubing, small parts, and complex geometries.
Coatings and Air Quality Control
SilcoTek coatings play a crucial role in enhancing the accuracy and reliability of air quality monitoring systems. Here at SilcoTek, we specialize in advanced coatings and surface treatments, which can contribute to improving and monitoring air quality through various applications. Our coating technology can provide solutions like emissions control and sensor performance in industrial applications. There have been several air quality applications.
Here is just one example... Untreated flow paths like bare stainless steel and even PTFE-lined flow paths will hold onto an ammonia sample, causing delayed readings or artificially low readings. As the NH3 accumulates in the system flowpath, it will eventually desorb or leach into the sample stream, resulting in high readings. The back and forth adsorption and desorption ultimately makes testing less and less relevant to real world conditions. At minimum, a reactive flowpath will reduce test efficiency while the analyst struggles to recalibrate or purge the flowpath. At worst, a reactive flowpath will skew test results, jeopardizing regulatory compliance or may lead to process stream contamination or reduced yield. This can be especially important for air quality testing.
Fast response means less chance of a cumulative build-up of reactive compounds in the system and fewer test errors. The key to fast response? A surface that does not retain or adsorb the analyte. The graph below shows SilcoNert 2000 does not adsorb the NH3 analyte, so there's little resulting desorption and disruption to analytical results.
SilcoNert response time to baseline is the shortest of the 3 surfaces compared:
- Stainless Steel: 33 seconds
- PTFE: 18 seconds
- SilcoNert: 9 seconds
- Baseline: 6 second
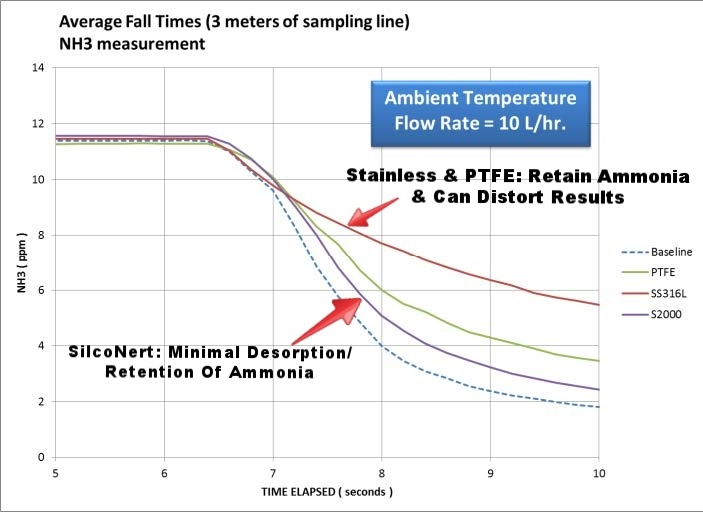
Semiconductor Sub-Fab Sustainability
Take, for example, our case study with Samsung Austin. SilcoTek partnered with Samsung Austin to provide a solution to issues they were seeing with their scrubber systems. Our coating was used to protect Samsung's decomposition reaction chamber by reducing corrosion. By utilizing SilcoTek's coating technology, Samsung was able to increase sustainability, reduce solid and contaminated water waste, improve uptime, decrease maintenance costs, and improve longevity of their parts. A controlled experiment compared the performance of their stainless steel and inconel uncoated parts to coated parts. Samsung saw a 300% increase in the longevity of the coated parts over the course of the experiment.
Two different coatings were tested to extend the lifetime of metal scrubber parts. The coated parts were exposed to 5 different chemistries. Two different corrosion mechanism were elucidated from the failure analysis performed. It is possible, indeed likely, that additional corrosion mechanisms are at play if all the possible process chemistries are taking into account. Although the a-Si coating performed better than the control, the coating of choice based on this study is an a-SiON. Based on the reduced corrosion rate, at least 100 kg/year of heavy metals are no longer incorporated into the fab waste stream. The amount of corroded solid waste is reduced by an order of magnitude. In addition to the reduction of metal in the waste stream, there was a significant decrease in discarded corroded equipment by over 1,000 kg/year.
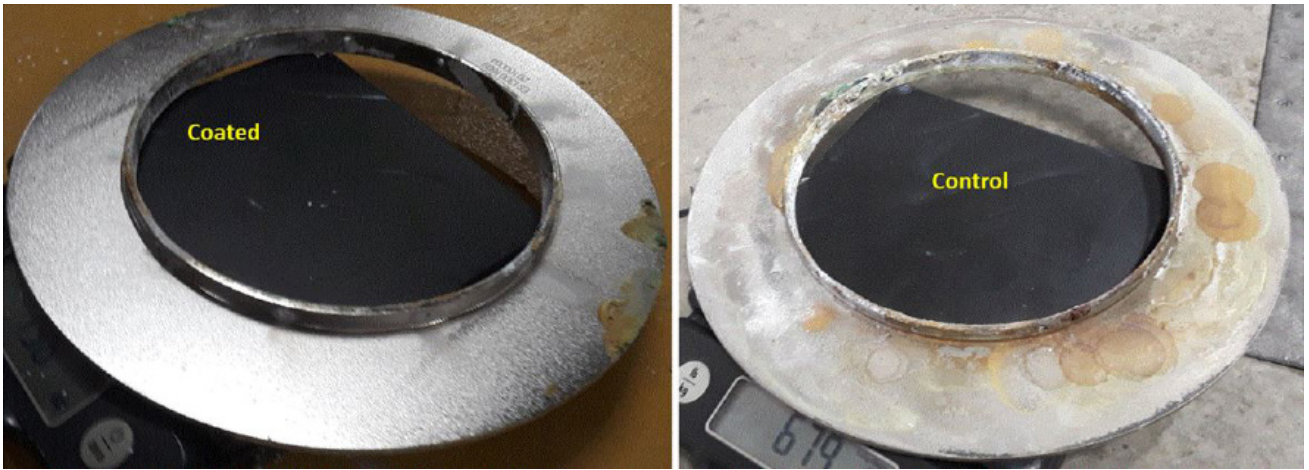
Above is a photo of the Siltride coated quench sleeve (left) in comparison to an uncoated quench sleeve (right) over the course of this testing. This is just one part in the process stream that was enhanced by SilcoTek's coatings. The considerable reduction in waste throughout the whole process is incredibly significant in sub-fab operations all over the world.
Check out EarthDay.org to see how you can get involved in Earth Day activities near you! If you have questions about SilcoTek's coatings, please reach out to our coating experts!