Let’s be honest: unless you're deep in the semiconductor world, it's easy to overlook just how precise chipmaking really is. We’re talking nanometer-level tolerances, where a single speck of contamination can throw off an entire wafer. Yikes!
It’s no surprise that semicon process engineers are obsessed with purity. But what often gets overlooked in the purity conversation? The equipment itself. That’s where SilcoTek CVD coatings come in.
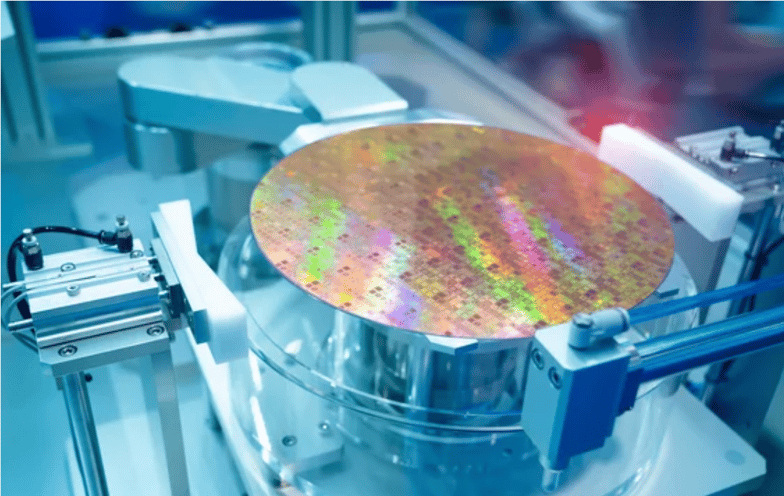
The Semiconductor World Runs on Ultra-Pure Everything
Semiconductor fabrication involves dozens of complex steps - deposition, etching, cleaning, and more. Every step has to be performed in ultra-clean environments using ultra-pure chemicals and gases.
But here’s the catch: these super pure chemicals often flow through metal valves, filters, and flow paths. Over time, those surfaces can leach trace metals or interact chemically with the process gases. And when that happens? You guessed it—contamination, yield loss, or costly downtime.
So, What’s the Fix?
Protect the surface.
By applying a chemically inert, corrosion-resistant coating like Silcolloy® 2000, Siltride® 1000, or Dursan®, we essentially put a barrier between the reactive metal substrate and the critical process. That means:
-
Fewer metal ion contaminants leaching into your process gases
-
Improved chemical compatibility with harsh etchants and solvents
-
Longer equipment life and reduced maintenance
In short: better yield, fewer headaches.
Coatings Aren’t Just for “Problem” Applications
We sometimes hear, “We don’t have corrosion problems, so we probably don’t need coatings.” But let’s flip that thinking for a second.
In semiconductor processes, even invisible contamination—at parts per trillion levels—can impact results. Our coatings aren’t just about preventing visible damage. They’re about creating an ultra-clean, inert surface that actively helps your process stay consistent and clean.
Whether it’s a vacuum line, a gas delivery system, or a component inside a deposition chamber, coating the internal surfaces can drastically improve process control.
Who’s Using These Coatings?
Without naming names (NDA life, you know how it is), our coatings are used by major fabs, OEMs, and equipment suppliers around the world. They’re especially common in:
-
ALD and CVD systems (where precursor purity is everything)
-
Wet etch stations (handling aggressive chemistries)
-
Gas distribution components (filters, regulators, manifolds)
We even coat parts before they ever see the cleanroom—so they arrive at your fab ready to go, no bakeout drama required.
Not to mention - we have an ISO 6 Class 1000 cleanroom on-site at SilcoTek that includes post-coating precision rinsing, drying, helium leak check, vacuum packaging, and custom labeling. Contact us for more information on that!
The Bottom Line
If you’re looking for a way to reduce contamination, improve chemical resistance, or simply make your semiconductor tools run cleaner for longer—surface coatings should be part of the conversation.
And if you’ve never considered it before? Let’s talk. We’d love to help you explore how the right coating can make a big difference.
Contact us today if you have questions about how our coatings can help in your applications!
Follow Us on Social Media!