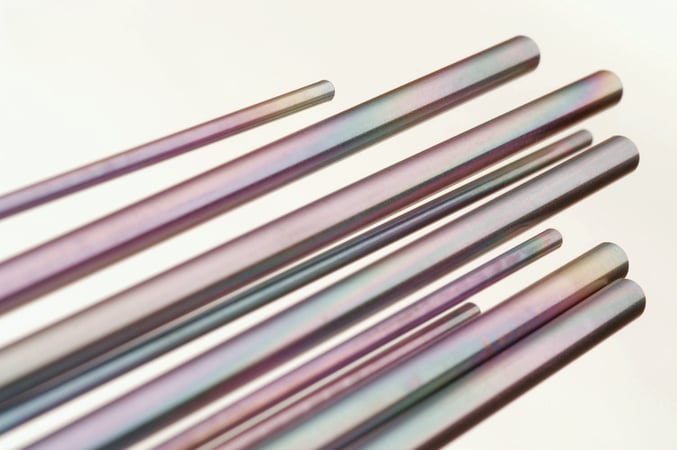
The global stainless steel market, valued at over $111 billion, underscores the critical role of high-performance tubing in modern industry. From analytical instruments to semiconductor manufacturing and chemical processing, the quality of tubing can significantly impact operational success. SilcoTek's innovative coating technology has emerged as a game-changing solution for industries demanding superior performance from their tubing systems.
Coating Process Overview
SilcoTek employs two distinct tubing coating methods, each optimized for specific tubing configurations. The internal coating process, designed specifically for coating coiled or rolled tubing, treats the tube itself as a process vessel. In this approach, process gases are flowed directly into the tube's inner bore, ensuring complete internal coverage. For straight tubing up to 80 inches in length (soon, we will be able to process up to 24 foot straight tubes!), we utilize our internal/external coating process, performed in a specialized reaction chamber that allows for comprehensive surface coverage.
Our chemical vapor deposition (CVD) process follows a carefully controlled sequence that begins with surface preparation using environmentally friendly cleaning solutions. The tubing is then heated to precise temperatures that enable optimal coating reaction conditions. Process gases are introduced in a controlled manner, resulting in the formation of a uniform, high-performance coating that bonds at the molecular level with the substrate.
Tubing Specifications and Capabilities
When it comes to coiled or rolled tubing, our process accommodates specific dimensional requirements to ensure optimal coating performance. For tubing larger than 1/16" in outer diameter, we can process coils up to 36 inches in diameter. Smaller tubing, with outer diameters of 1/16" or less, requires coils no larger than 18 inches in diameter. To maintain the integrity of the coils during processing, we require all tubing to be shipped on metal spools or securely bound with metal wire, as wooden, plastic, or other flammable materials cannot withstand our process conditions.
For straight tubing applications, our capabilities extend to pieces up to 80 inches (2 meters) in length. We can successfully coat tubing with internal diameters ranging from 1/16" up to sizes exceeding 6 inches, providing both internal and external coating coverage. This versatility allows us to serve a wide range of industrial applications while maintaining consistent coating quality. Coming soon, we will be able to process up to 24 foot straight tubes, so stay tuned for more information!
SilcoTek's maximum length for straight and coiled tubing.
Breaking New Ground in Bending Performance
Traditional bend radius recommendations have long served as industry standards, with specific guidelines based on tubing outer diameter. For tubing less than 1/16", we typically recommend a minimum bend radius of 1 inch (2.5 cm), while 1/8" tubing calls for a 2-inch (5.1 cm) radius. Larger tubing sizes of 1/4" and 3/8" require minimum bend radii of 4 inches (10.2 cm) and 6 inches (15.2 cm) respectively.
However, recent third-party testing has revealed exciting new possibilities for applications requiring tighter bends. Extensive testing has demonstrated that 1/16" tubing can successfully maintain coating performance even when bent to a radius as tight as 3mm—significantly tighter than traditional recommendations. This breakthrough has been validated through rigorous mass spectroscopy and FPD trials, with testing conducted across a range of reactive compounds, particularly sulfur species. The testing showed consistent performance regardless of whether the tubing was bent before or after coating, opening new possibilities for complex installation requirements. View our application brief on bending.
Our recommended minimum bend radius is calculated by multiplying the tube OD by 16. This is a common surface finishing guideline that is conservative to ensure tubing is not stretched to the extent of exposing new, uncoated surface area.
OD
<= 1/16"
1/8"
1/4"
3/8"
1/2"
3/4"
|
Min. Bend Radius
1" (2.5 cm)
2" (5.1 cm)
4" (10.2 cm)
6" (15.2 cm)
8" (20.3 cm)
12" (30.5 cm)
|
Performance Advantages in Real-World Applications
The superior performance of SilcoTek coatings manifests in several critical ways in analytical and industrial applications. In analytical settings, our coatings effectively eliminate common problems that plague uncoated systems, such as lost peaks, peak tailing, and ghost peaks. This enhanced performance enables reliable part-per-billion sensitivity in analytical applications, making our coated tubing ideal for high-precision measurements and analysis.
In terms of corrosion protection, our coatings demonstrate remarkable effectiveness, offering up to ten times improvement in corrosion resistance compared to uncoated surfaces (see below). This enhanced protection extends across a broad spectrum of aggressive chemicals, including hydrochloric acid, sulfuric acid, and hydrobromic acid. Such robust performance makes our coated tubing particularly valuable in demanding industrial environments where corrosion resistance is paramount.
Dursan can increase corrosion resistance by 10x or more through preventing interaction of the analyte or process fluid and the stainless steel surface. Dursan exceeds typical metal passivation capability. Immersion testing in 6M hydrochloric acid (HCl) shows that Dursan coated surfaces prevent surface attack and protect stainless steel from rust by orders of magnitude compared to passivated stainless steel, preventing corrosion.
Industry Applications and Impact
SilcoTek's coated tubing has found essential applications across numerous industries, each benefiting from its unique performance characteristics. In analytical and laboratory settings, our coatings have revolutionized chromatography and diagnostic equipment performance. The enhanced inertness and stability of coated surfaces enable more accurate measurements and more reliable results, particularly in trace analysis applications where every molecule counts.
The refinery and petrochemical processing sectors rely heavily on our coated tubing for precise feedstock quantification and process monitoring. These industries deal with highly corrosive and reactive materials, making our coating's protective properties invaluable for maintaining system integrity and reducing maintenance requirements. Similarly, in hydrogen production facilities, our coated tubing plays a crucial role in enabling trace-level measurement of problematic contaminants, ensuring product purity and process efficiency.
The semiconductor industry, with its stringent requirements for gas delivery systems, has embraced our coating technology as a solution for preventing contamination and corrosion. The exceptional inertness of our coated surfaces helps maintain the ultra-high purity levels required for semiconductor manufacturing, while their durability ensures long-term reliability in these critical systems.
Joining Methods and System Maintenance
Integrating SilcoTek-coated tubing into existing systems is straightforward, with several proven connection methods available. Compression fittings provide a reliable way to join coated tubing sections, and we recommend using coated fittings to maintain a continuous inert flow path. For applications requiring welded connections, our coatings accommodate welding, though it's important to note that the coating will be removed in the heat-affected zone approximately 2-4mm in all directions from the weld. Face seal flanges can be welded onto the tubing before coating, offering another flexible connection option.
System maintenance is simplified by our coating's durability and resistance to cleaning processes. The molecular-level bonding of our coatings to the base material ensures long-term stability and resistance to typical maintenance procedures. Our quality verification process includes comprehensive thickness testing using the Filmetrics F40-Series analyzer, along with detailed visual inspections for coating uniformity. This rigorous quality control ensures 100% coverage, even in complex pathways and tight geometries.
Coated Tubing Appearance
SilcoTek’s process for treating coiled tubing results in a uniform coating throughout the interior of the tubing from end to end. The exterior surface of coiled tubing is not coated, but it will exhibit a change in appearance after being oxidized by the high temperatures of our CVD coating process. The resulting external appearance will vary based on the specific elemental composition of the tubing substrate.
Coated tubing often exhibits a brownish appearance.
Technical Support and Customer Service
Our commitment to customer success extends beyond providing superior coatings. Our technical support teams in both the United States and Europe stand ready to assist with application-specific questions and coating selection. Customers can reach our technical service team at +1(814) 353-1778 or via email at TechService@SilcoTek.com.
Conclusion
SilcoTek's coating technology represents a significant advancement in tubing performance enhancement, offering solutions that meet and exceed the demanding requirements of modern industrial and analytical applications. The combination of our advanced CVD process, flexible coating options, and breakthrough capabilities in areas like bend radius makes our coated tubing an ideal choice for critical applications across industries.
The documented improvements in corrosion resistance, inertness, and overall performance demonstrate the tangible benefits our coatings provide. Whether dealing with aggressive chemical environments, requiring ultra-high purity, or seeking improved analytical accuracy, SilcoTek's coated tubing delivers measurable advantages over uncoated alternatives.
We invite you to connect with our technical service team to explore how our coating solutions can address your specific requirements and enhance your operational capabilities. Our expertise in surface treatment technology, combined with our commitment to customer success, ensures that you'll receive not just a product, but a complete solution tailored to your needs.