An under-performing sampling system can cost an operator more than just time and money. A lousy system can be the cause of poor yield, slow response, bad decisions, and regulatory or contract violations. We all know when a sample transfer system is running great, but how do you know when a system is not doing its job?
The first in our Analytical series, SilcoTek's e-book, "Keys to a High-Performance Analytical System" is jam-packed with useful information about keeping your analytical equipment running at peak performance. The e-book goes into detail about the below points and offers excellent data showing how an inert analytical system is the best way to ensure fast and reliable results.
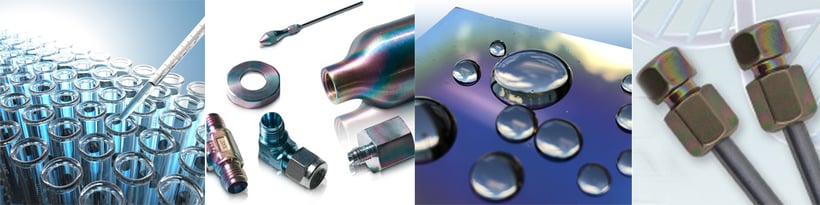
There are 5 tell-tale signs that your system is not running at peak performance.
- Calibration Errors
- Slow Response
- Suspiciously Steady Readings
- Excessive Maintenance
- Variable Response
Each of these factors can cause a tremendous amount of time, money, and frustration for companies who rely on accurate and fast results. No one likes surprises when it comes to their results. SilcoTek coatings can offer you peace of mind in knowing that your results are accurate.
Here are 7 tips and questions to ask for improving analytical sampling and reliability:
- Make the flow path inert
- Coat the entire sample pathway
- Check the calibration system
- Check the sample probe location
- Is the heat trace tubing inert and installed per manufacturer specifications?
- Are regulators designed for inertness?
- Are GC setup conditions, column, and injection volume within specifications?
How do you know if your flowpath is inert?
Testing for relevant, controlled target compounds is a sure-fire way to know if you're getting the results you expect. This would test both adsorption and desorption in the stream. If your test results are not as you would expect, it is likely that your flowpath is not inert and could be altering your results.
What are the surface energy effects?
Contact angle and surface energy can play an important role in compound retention. Low contact angle and high surface energy can cause adsorption and can corrupt the sample. SilcoTek coatings alter the surface energy of your substrate to increase contact angle, effectively reducing surface energy, making it less likely for a reaction with your sample.
Does heat affect inertness?
Because heat acts as a catalyst to many chemical reactions, introducing higher temperatures can speed up the time it would take for a reaction to occur. In doing so, you are adding more opportunities for chemical and surface reactivity. Ensuring that your pathway is inert will combat the higher temperature's disastrous effects.
How to reduce contamination and improve reliability:
- Determine the sample integrity
- Manage moisture
- Consider your flowpath
- Eliminate cold spots in heat trace tubing
- Proper installation to avoid moisture retention
- Avoid build-up of active particulates
- Select proper materials for the sampling environment
- Protect the flowpath with inert coatings
- Consult the experts
- Tubing suppliers
- Coating providers
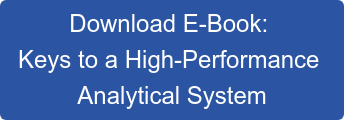
Check back next month for the next e-book in this series!