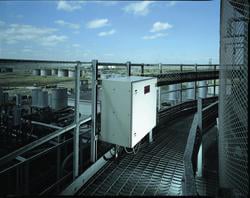
Monitoring process conditions and emissions are critical to plant performance. Unfortunately process sampling can be a complex and frustrating endeavor. Often analysts are frustrated by seemingly unexplained and sudden changes to process conditions and sampling system accuracy.
- Unable to calibrate or long calibration times
- Loss of sample
- Inaccurate results
- Slow response
For example; a large oil refining company had trouble calibrating their sulfur standard. Both high standard and low standard flowpaths were coated with SilcoNert® 2000. The low side (10ppm) calibrated immediately; but the high side (200ppm) would not stabilize. The technicians struggled for a week trying to bring the system into calibration. Eventually the cause of the long calibration time was traced to a single fritted filter in a regulator that was not coated. This demonstrates the importance of a totally inert sample pathway.

SilcoTek® coatings can improve sample system performance 3 ways.
Minimize adsorption
SilcoTek® inert coatings prevent adsorption of sample and sample loss.
|
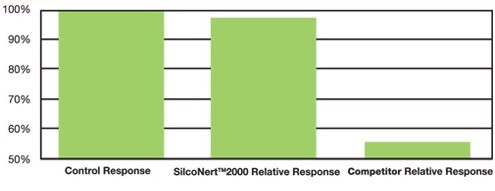 |
Coat the entire sample pathway including:
- Metal filters
- Regulators
- Tubing
- Sample cylinders
- Fittings
When sampling for low level sulfurs, priming and traditional sample techniques are ineffective. Inert coatings are the best option for minimizing adsorption. At low detection levels, even small uncoated surfaces, like a single fitting can impact sample calibration and accuracy.
Repel water
Prevent moisture contamination and adsorption by lining the sample pathway with hydrophobic coatings.
|
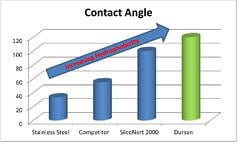 |
Moisture can adsorb sample compounds and cause system corrosion and response issues. SilcoTek coatings are hydrophobic, improving moisture control by 8x or more. Systems using SilcoTek coatings experience:
- Faster response
- Improved flow
- Less maintenance
- Easier calibration
SilcoTek coatings improve corrosion resistance by 8x or more. By reducing corrosion, system maintenance is reduced, sample response is improved and sample reliability can be increased by orders of magnitude.
Coat the entire pathway:
- Regulators
- Filters
- Tubing
- Fittings & valves
- Sample cylinders
One final note, no matter how good the coating; poor system design will impact system performance. Follow heat trace installation and maintenance instructions. Maintain analyzers, probes, filters and all system components according to manufacturers instructions. Inert coatings and robust system design will prevent most analyzer sampling issues.
Learn more about improving sample system performance.
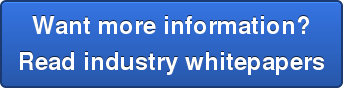