The purpose of this blog is to study the impact of substrate passivation before coating on the long-term HCl corrosion performance of three SilcoTek coatings. Dursan®, Silcolloy® 2000 and Siltride® 1000 were studied over a period of 30 – 40 days in 5% HCl while their corrosion rates were monitored in real time via Linear Polarization Resistance (LPR). Uncoated 316L stainless-steel and alloy C22 were also included in the study for comparison. All three coatings far outperformed bare 316 SS while Silcolloy 2000 and Siltride 1000 exhibited comparable performances as bare C22.
Background:
SilcoTek has recently launched a citric acid passivation service, a premium surface preparation step either to be applied prior to our CVD coating service. Passivation is the removal of free iron from the surface of stainless-steel to facilitate the formation of a thin passive oxide layer (enriched in chromium and chromium oxide) on the surface to enhance corrosion resistance properties.
A study was designed to evaluate the impact of passivation on the corrosion performance of three SilcoTek coatings on 316 stainless-steel, Dursan, Silcolloy 2000 and Siltride 1000, the three most corrosion resistant coatings offered by SilcoTek. Uncoated 316 stainless-steel (both passivated and unpassivated) and alloy C22 were included in the study for comparison purposes.
Passivation infographic
Test Procedures and Results:
316 stainless-steel (SS) coupons (2.25” x 2.25”) were serialized and mirror-polished on one side, and the polished side was used for all measurements. C22 coupons (2.25” x 2.25”) were machine finished on both sides and hand scribed for identification. All coupons were surface prepared through SilcoTek’s SOP alkaline bath to remove common surface contaminants such as grease and fingerprints. Half of the SS coupons were then processed through SilcoTek’s new citric acid passivation process per ASTM A967 Citric 2 before coating. None of the C22 coupons saw the passivation process.
(6) SS coupons were used for each coating type, where 3 were passivated and 3 were not. A total of 18 coated coupons were evaluated, along with 6 uncoated SS coupons (3 passivated and 3 not), and 3 uncoated C22 coupons. Each coupon was continuously exposed to a solution of 5% HCl via an electrochemical cell and linear polarization resistance (LPR) was used to monitor the real time corrosion rate of the test specimen over a period of 30 – 40 days. The LPR experiment set-up is shown in Figure 1, bottom. The average corrosion rate values of the three coupons per group are reported.
Figure 1 shows the results for uncoated 316 SS samples. Passivation showed perhaps some initial benefit (i.e. lower corrosion rate during the first week of exposure) but the thin passive oxide formed during passivation was not able to sustain lasting protection against HCl corrosion. The two groups performed similarly throughout much of the test window and all samples showed considerable signs of corrosion at the end of the 36-day test period. Note that the areas within the circle were exposed to the HCl solution and showed signs of corrosion.

Figure 1 (top left): corrosion rate progression of uncoated 316 SS in 5% HCl with and without passivation over 36 days, showing only initial benefit from passivation which quickly diminished over time; (top right): visual comparison showing considerable corrosion for all testing coupons; (bottom): the polarization resistance scan experiment set-up
When paired with SilcoTek's Dursan coating technology, the benefit of passivation is much more evident, as illustrated in Figure 2. Passivation helped to slow down the corrosion progression over time and reduce the corrosion rate by over half during the first month of exposure. The passivated coupons also showed less pitting in comparison to the unpassivated coupons at the end of the test 32 day (Figure 2 right).
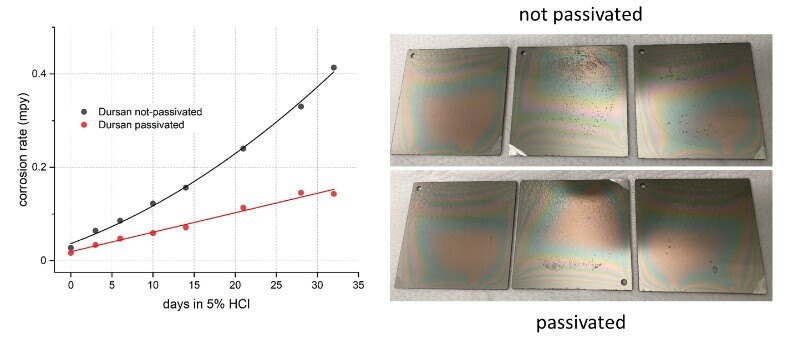
Figure 2 (left): corrosion rate progression of Dursan-coated 316 SS in 5% HCl with and without passivation over 32 days, showing the benefit of passivation and (right): visual comparison showing less pitting for the passivated samples at the end of the test.
Similar to Dursan, Silcolloy 2000-coated 316 SS also benefited from passivation, as illustrated in Figure 3. Passivation helped to slow down the corrosion progression over time and reduce the corrosion rate by over half during the 35 day exposure. The passivated coupons also showed less pitting in comparison to the unpassivated coupons at the end of the test (Figure 3 right).
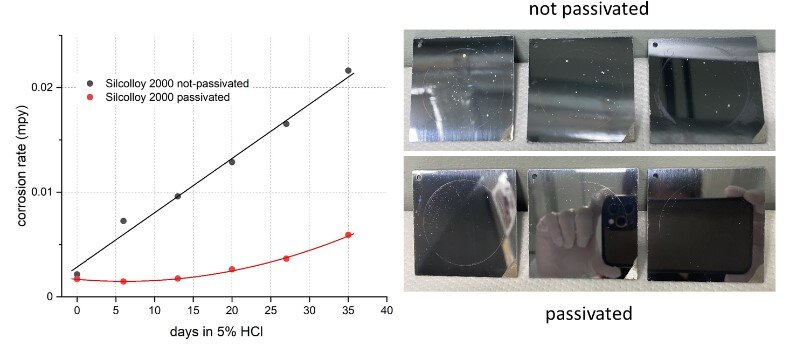
Figure 3 (left): corrosion rate progression of Silcolloy 2000-coated 316 SS in 5% HCl with and without passivation over 35 days, showing the benefit of passivation and (right): visual comparison showing less pitting for the passivated samples at the end of the test.
The last coating evaluated, Siltride 1000, did not show the same trend as the other two coupon coatings with and without passivation. Instead, the corrosion rates for all samples remained low and other than the initial slight increase, saw almost no change throughout the test regardless of passivation. Additionally, none of the samples showed any pitting after the test, as shown in Figure 4. Even though the corrosion rate seemed a bit higher for the passivated sample group, the actual difference between the two trend lines is very small given the log scale on the y-axis and is within normal sample variation and measurement error. The performances of the passivated and unpassivated Siltride 1000 samples are thus considered statistically identical. This does not necessarily indicate that passivation adds no benefit to Siltride though. It may simply require a longer test window or a more aggressive concentration to develop a clearer difference, which the current test parameters are too mild to reveal.
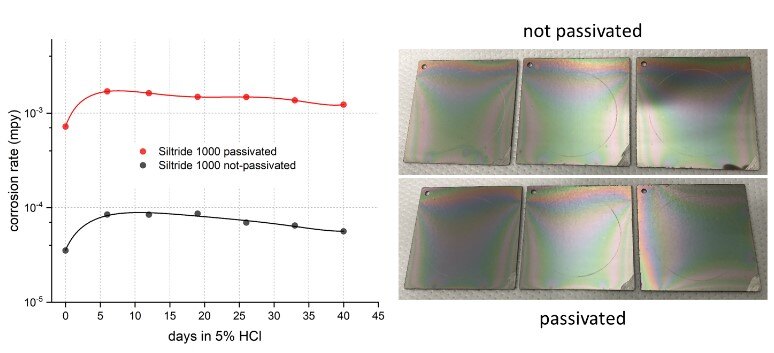
Figure 4 (left): corrosion rate progression of Siltride 1000-coated 316 SS in 5% HCl with and without passivation over 40 days, showing similar and excellent performances of both groups and (right): visual comparison showing no pitting for any of the samples at the end of the test.
Lastly, three uncoated alloy C22 coupons were evaluated in the same manner. Passivation is not a common practice for alloy C22 and was not applied to the C22 coupons in this study because C22 is a nickel-based alloy and only contains 2-6% iron. Unexpectedly, one of the C22 coupons showed rapid corrosion progression (Figure 5 right) that is uncharacteristic of this alloy and drastically different from the other two C22 coupons (Figure 5 left, excluding data from the outlier coupon).
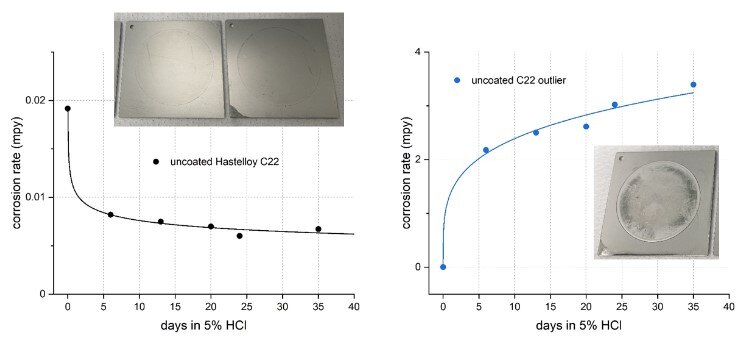
Figure 5 (left): corrosion rate progression of the two normal behaving uncoated C22 coupons in 5% HCl over 35 days and (right): C22 outlier coupon showing rapid corrosion progression.
SEM-EDS analysis was performed to understand the cause of the abnormal C22 behavior. First, an area outside the circle (i.e. not exposed to HCl) was analyzed on the abnormal coupon as well as on a normal behaving coupon. They both showed compositions in agreement with Hastelloy C22 spec, ruling out wrong metal type as the reason. Next, an area inside the circle (inside the circle is exposed to HCl and the analyzed area is highlighted in the red box in Figure 6) was analyzed on the abnormal coupon. The results shown in Figure 6 indicate a phase segregation of tungsten oxide (the island clusters in the SEM image) from the bulk C22 matrix. This “dealloying” behavior may explain the abnormal corrosion performance and suggests that high performance alloys sold as (and analyzed as) C22 are not immune from quality variations that can have significant negative impact on their performance.
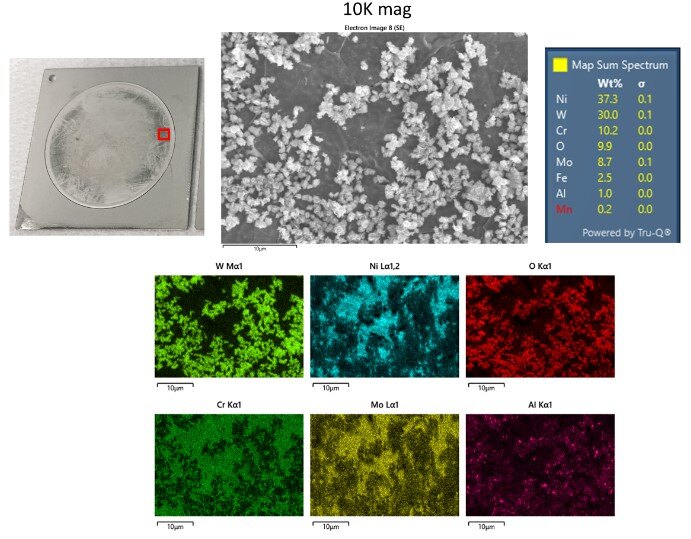
Figure 6: SEM-EDS analysis inside the corroded area of the abnormal C22 coupon showed “dealloying” of tungsten oxide from the rest of the alloy, which may explain the outlier behavior of this coupon.
Summary:
In this TI, we explored the impact of SilcoTek’s latest citric acid passivation on the corrosion performance of 316 SS substrate in 5% HCl over a period of 30-40 days, in combination with our CVD coatings. Dursan, Silcolloy 2000 and Siltride 1000 were evaluated with and without passivating the substrate prior to coating. Uncoated 316 SS and alloy C22 were also evaluated for benchmark purposes.
Figure 7 shows the overall comparison of all non-passivated (NP) 316 SS samples and C22. All coated 316 SS and the bare C22 samples far outperformed bare 316 SS, exhibiting at least two orders of magnitude lower corrosion rates. When examined closely, Silcolloy 2000 and Siltride 1000-coated 316 SS showed comparable performance to C22 with Siltride even slightly outperforming C22 (Dursan < Silcolloy 2000 < C22 < Siltride 1000).
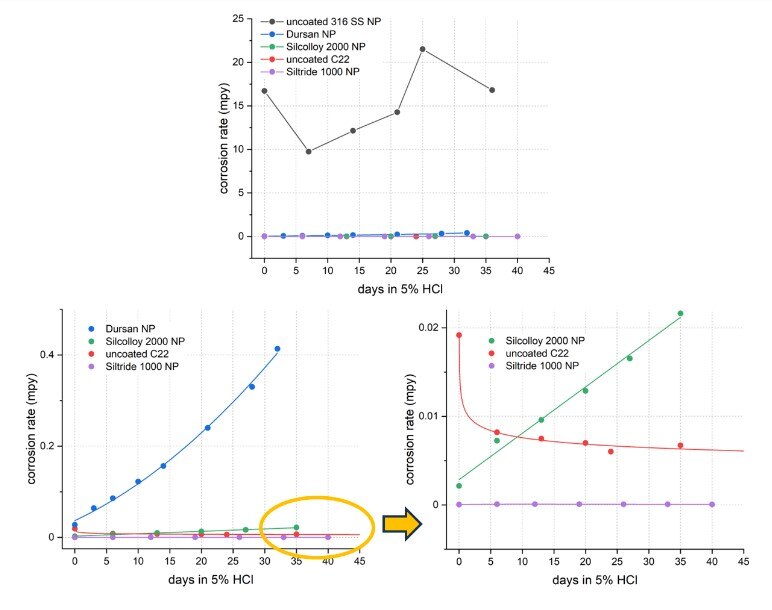
Figure 7: overall comparison of all non-passivated (NP) samples showing all coatings far outperforming uncoated 316 SS, and Silcolloy 2000 and Siltride 1000-coated 316 SS performing similarly to C22.
Figure 8 shows the overall comparison of all passivated (P) 316 SS samples and C22. Again, all coated 316 SS and the bare C22 samples far outperformed bare 316 SS, exhibiting at least two orders of magnitude lower corrosion rates. When examined closely (blowup in Figure 8 right), Silcolloy 2000 and Siltride 1000-coated 316 SS showed comparable performance to C22 with Siltride and Silcolloy 2000 even slightly outperforming C22 (Dursan < C22 < Silcolloy 2000 < Siltride 1000).
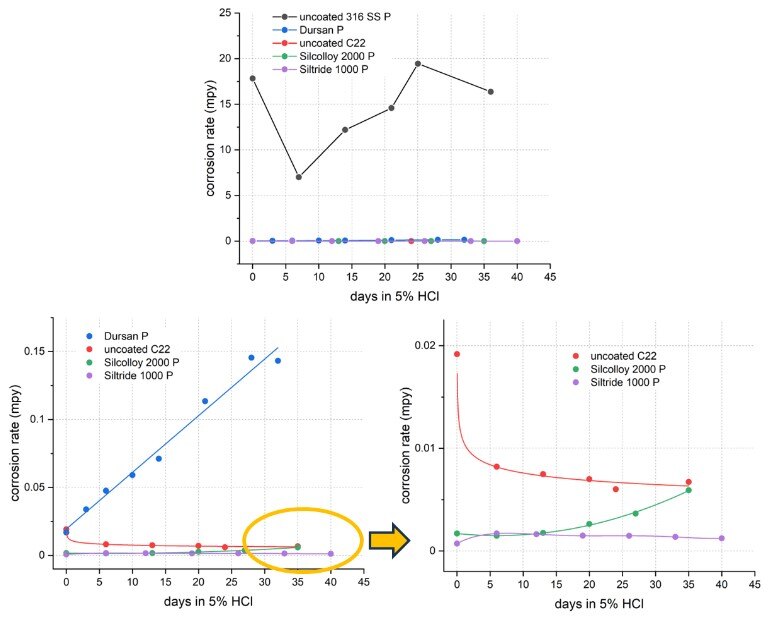
Figure 8: overall comparison of all passivated (P) samples showing all coating far outperforming uncoated 316 SS, and Silcolloy 2000 and Siltride 1000-coated 316 SS performing similarly to C22.
Passivation was found to benefit both Dursan and Silcolloy 2000, helping to slow down the corrosion progression over time and reduce the corrosion rate by over half during the test period. Passivation did not seem to impact the performance of Siltride 1000 as both groups showed excellent performance and no visual signs of corrosion. It may require a longer test window or a more aggressive concentration to determine any potential performance difference between passivated and non-passivated Siltride coupons.
For more information about passivation or SilcoTek's coating services, please contact our coating experts!