Last week, we talked about metallurgy and how SilcoTek's coatings don't change the physical properties of 316L stainless steel. To build on that topic, we also wanted to talk about substrate materials and how different substrates can yield differing coating performance. What, if any, are the issues with using 304 grade stainless steel vs. 316L stainless steel?
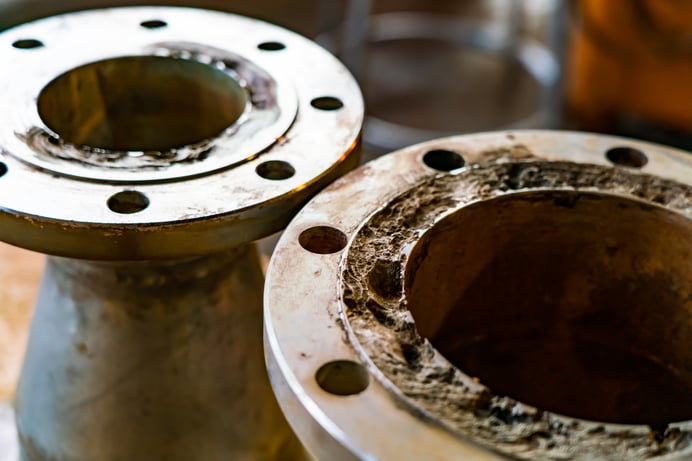
Not All Materials Are Created Equal
When it comes to corrosion-resistant coatings, not all stainless steel is created equal. Selecting the right stainless steel for your application is crucial for achieving optimal corrosion resistance, even with barrier coatings like SilcoTek's. In this blog post, we'll explore the key differences between two commonly used stainless steel grades, 304 and 316L, and how the addition of molybdenum (Mo) significantly enhances corrosion resistance.
Understanding Corrosion and Stainless Steel
304 and 316L stainless steel substrates are prevalent in various industries, but the critical distinction lies in the addition of 2~3% molybdenum to the 316L family. This addition dramatically improves corrosion and oxidation resistance, particularly in environments exposed to saline or chloride-containing chemicals.
The Impact of Substrate Metal on Coating Performance
Even with corrosion-barrier coatings, the choice of substrate metal plays a crucial role in determining performance. Protective coatings act as barriers between the metal and corrosive environments, requiring corrosive chemicals to diffuse through the coating's pathways. The quality of the substrate metal influences the overall corrosion rate when coated.
Comparing 304 and 316L Stainless Steel Coupons
A corrosion test compared the performance of 304 and 316L stainless steel coupons, both coated with SilcoTek's Dursan® coating, in hydrochloric acid (HCl) and sulfuric acid (H2SO4) solutions over one week. The results revealed a significant disparity between the two grades.
Figure 1: Corrosion test results of 304 and 316L SS coupons in 6M HCl for one week.
In 6M HCl, 304 SS, even when coated, exhibited severe corrosion, with only a moderate rate reduction of 13%. In contrast, Dursan-coated 316L SS demonstrated a remarkable improvement factor of over 60 fold. The presence of molybdenum in 316L played a crucial role in forming a higher quality passive film, resulting in a stronger coating/substrate interface and ultimately lower corrosion rates.
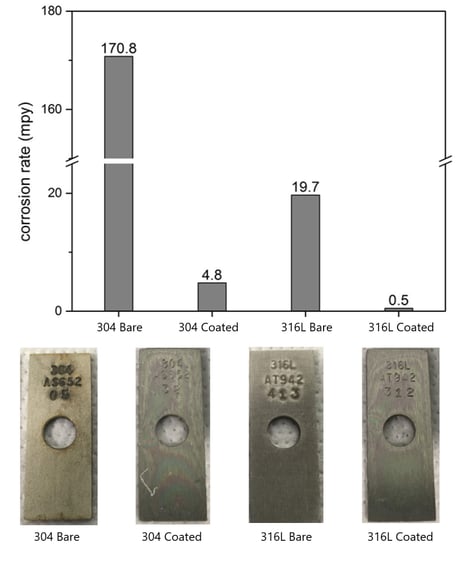
Figures 2 & 3: Corrosion test results of 304 and 316L SS coupons in 25% H2SO4 for one week (left) and test results of 304 and 316L SS coupons in 5% HCl for one week (right).
The second test immersed coupons in 5% and 25% H2SO4 separately, showing similar results. The 304 SS, a poor baseline material for this exposure condition, experienced heavy corrosion, while Dursan-coated 316L SS significantly reduced the corrosion rate by two orders of magnitude.
Tailoring Solutions to Corrosive Environments
The data emphasizes the importance of selecting an appropriate substrate metal based on the corrosive environment's severity. In less aggressive conditions, coatings like Dursan offer significant protection and extend the lifetime of both 304 SS and 316L SS base materials.
Conclusion
In tackling corrosion challenges with coatings like SilcoTek's CVD coating, considering the combination of baseline metal and coating as a whole is essential. Factors such as the environment's severity, substrate metal quality, coating-substrate interface, coating quality, and end-user expectations collectively determine the success of a solution for a particular corrosion challenge. Testing the combination in the actual application environment before scaling up is recommended, so SilcoTek offers free coated stainless steel samples and can even coat your own custom test parts at reduced or no cost to you. Click here to start your evaluation.
In conclusion, the right choice of stainless steel, combined with an appropriate coating, can provide superior corrosion resistance and extend the lifespan of metallic components. Understanding the intricacies of substrate metal and coating interactions is key to achieving optimal performance in diverse corrosive environments.
SilcoTek’s team of experts is standing by to assist customers with their material and coating selection questions. We are here to partner with you and collectively achieve game-changing performance for your products.
Ready to start your coating project?