SilcoTek is very excited to announce our 2 newest services, citric passivation and ISO 6 Class 1000 cleanroom and packaging! Read on to find out how these new offerings can benefit your processes.
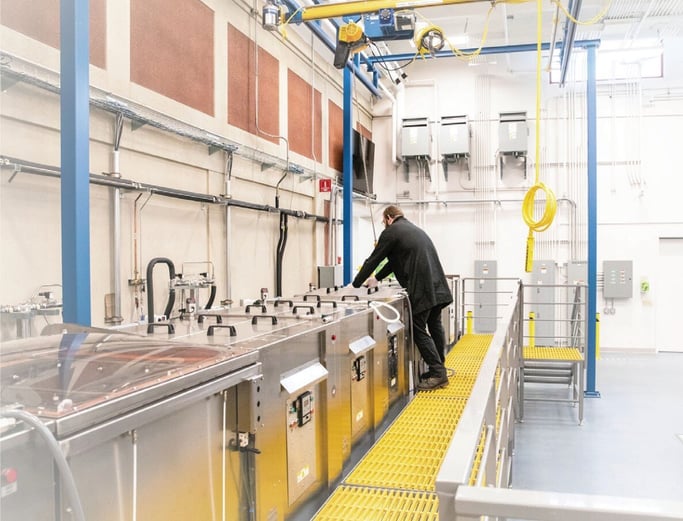
SilcoTek's new passivation line.
What is passivation?
Passivation is an anti-corrosion treatment that enhances stainless steel's resistance to rust. The process forms a protective metal oxide layer to provide greater protection from chemical attack. Our process is defined by the American Society for Testing and Materials (ASTM) A967 method. ASTM A967 is the industry standard specification for chemical passivation of stainless steel parts. There are several different types of chemical passivation, including nitric acid immersion, citric acid immersion, and electrochemical treatment. At SilcoTek, we are using a citric acid passivation technique, of which there are several versions. SilcoTek's version is "Citric 2—The solution shall contain 4 to 10 weight percent of citric acid. The parts shall be immersed for a minimum of 10 min at a temperature in the range from 50 to 60°C [120 to 140°F]" (ASTM, 2017).
Additional Corrosion Protection
We offer a one-stop-shop to provide not only the benefits of the SilcoTek-coated surface, but also improved coating adhesion and corrosion resistance. Combining passivation with our coatings is the best way to maximize part performance and lifetime while minimizing risks to our customer’s process. While passivation is not required before SilcoTek’s coating processes, surface cleanliness is critical to coating success.
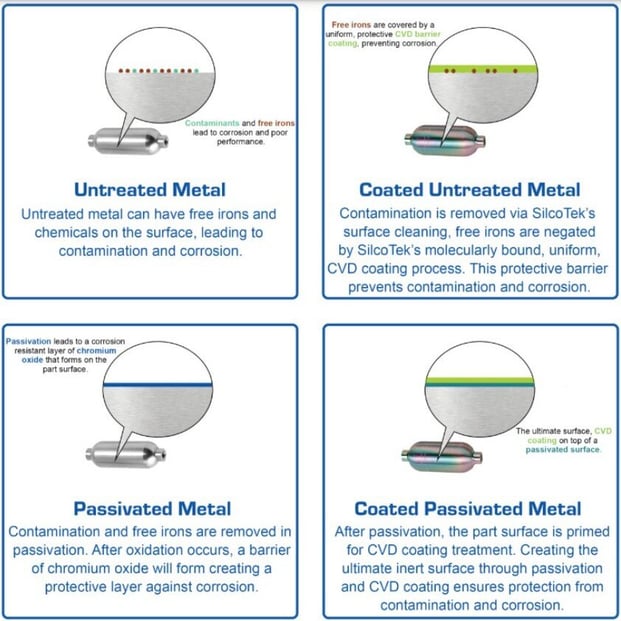
Benefits of SilcoTek Performing Citric Passivation Before Coating:
- Significantly reduce lead times and costs in your supply chain by consolidating services under one roof.
- Save money by improving corrosion resistance of coated stainless steel parts, increasing service life of your investment.
- Further enhance game-changing properties of SilcoTek-coated parts including hydrophobicity, anti-fouling, chemical inertness, and more.
- Increase sustainability in your overall manufacturing process. Unlike nitric acid, citric acid requires no special disposal and can be flushed down the drain like tap water.
Our passivation service meets the SEMI F19 Ultra High Purity standard, which defines the "wetted surface characterization requirements and the finish acceptance criteria for tubing and components fabricated in stainless steel per SEMI F20 and intended to control or contain gases and liquids used in semiconductor manufacturing" (SEMI, 2015). SEMI F19 makes an extended definition based on specific testing methods:
High Purity
- Cr:Fe > 1.0 · CrOx:FeOx > 1.0 · Oxide thickness, t > 1.5 nm
Ultra High Purity
- Cr:Fe > 1.5 · CrOx:FeOx > 2.0 · Oxide thickness, t > 1.5 nm
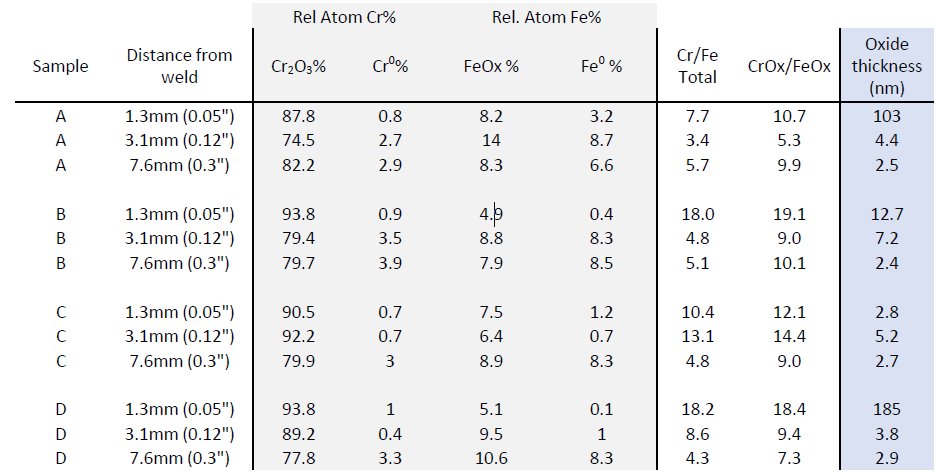
Data showing XPS results demonstrating the Chrome:Iron, Chrome Oxide:Iron Oxide, and Oxide thickness measurement meet the UHP standard of a SilcoTek passivated tubing sample that had been welded.
Liquid Particle Counter
In addition to the clean room, SilcoTek has invested in a Liquid Particle Counter (LPC) to ensure particulates are not being introduced to your parts after coating and to ensure the parts do not exceed the particulate thresholds. The LPC is being installed in-line with our passivation tanks to allow for a seamless passivation process. We will be introducing this option in July!
What is a cleanroom?
We have an ISO 6 Class 1000 cleanroom. These specifications mean that our cleanroom has HEPA filtration systems that maintain an air cleanliness of up to 1,000 particles per cubic meter. The filtration system must have a minimum of 20-30% coverage and at least 180 air changes per hour. SilcoTek’s filtration system covers more than 30% and changes the room air up to 240 times per hour, exceeding standard requirements.
SilcoTek's new cleanroom packaging service.
We can provide post-coating rinsing, drying, helium leak checks, and vacuum packaging from our ISO 6 (Class 1000) cleanroom. The benefits of cleanroom packaging include protecting sensitive hardware from contamination, customized labelling to meet specific requirements, and safeguarding coated products for transit.
Benefits of SilcoTek Performing Cleanroom Services:
- Prevent contamination in the initial production process. Ensure that coated parts coming from SilcoTek will not disrupt processes because of particulate contamination.
- Guarantee that customer parts are treated in a facility that complies with industry standards on allowable particulate.
Some of the most important benefits to consider with SilcoTek's new passivation and cleanroom services are the reduction in shipping time, shipping costs, and additional vendors to deal with. We offer the convenience of these services at competative pricing. Contact us today for a quote!
Have questions about our new cleanroom or passivation services? Contact one of SilcoTek's technical service team members today!
Follow Us on Social Media!
