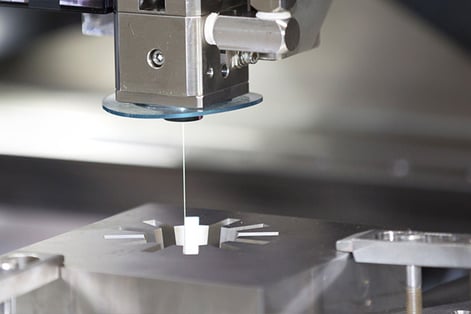
A problem part leads to a discovery about wire EDM and silicon compatibility.
Is Wire EDM Compatible with the Silicon Coating Processes
*Wire electrical discharge machining (EDM) is a technique that can be used to make very high tolerance parts. Recently parts were unknowingly fabricated via EDM and sent to SilcoTek® for coating. These parts failed our coating process. In this blog post we'll discuss details of why certain EDM processes are incompatible with our coating technology. Is wire EDM compatible with the silicon coating process? That all depends on the wire material.
In this blog post you will learn:
- How the material composition of wire EDM effects silicon coating quality.
- Why copper contamination is important to control in processes sensitive to certain types of metal contamination.
- How to evaluate surfaces for copper contamination.
|
Background:
SilcoTek typically does not have the details about what processes parts are exposed to prior to arrival for coating. Some processes can expose parts to materials and chemicals that can unknowingly be detrimental to the coating process. Some examples are cleaning with incompatible detergents such as simple green or other common household detergents, cross contamination of copper alloys whether it be by machining with the same tool or contamination via cleaning in the same bath, or in the case of this blog post, utilizing wire EDM instruments for cutting parts during the machining process. In particular, the use of brass or copper wires while performing EDM can cause issues. Let's discuss further.

Copper Contamination and Silicon Coating Quality
Copper, and alloys that contain large amounts of copper, are known to not coat well through our process. The copper can catalyze silicon nanowire growth (figure 1) rather than forming the desirable planar growth (figure 2) expected from our coatings. For this reason, many copper based alloys are marked as “not treatable” on SilcoTek’s material compatibility guide.
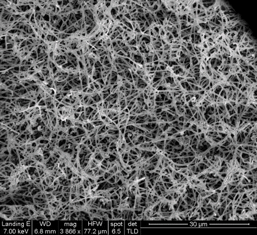
Figure 1: An example of nanowire growth.
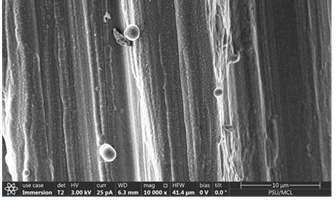
Figure 2: Typical silicon planar growth.
There are times that customers inadvertently perform steps that incorporate copper into their parts making typically treatable parts no longer treatable. For example, a previous investigation found copper contamination from a machine shop that would machine brass and stainless steel parts on the same instrument. The shop did not change the tooling which would cause cross contamination of the copper onto the stainless steel part.
Learn about the latest in coating material performance, get our coating properties quick reference guide.
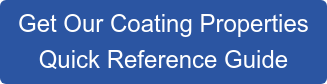
Data and Discussion
Electrical discharge machining (EDM) is a technique that can be used to machine parts to very tight tolerances. For a description of this technique, please watch this youtube video. Figure 3 shows coupons that were machined via EDM on one side of the coupon. Not only do the two sides look different visually, but scanning the surface with our XRF instrument (used to inspect incoming product by our Manufacturing Receiving Team) detected an elemental difference.
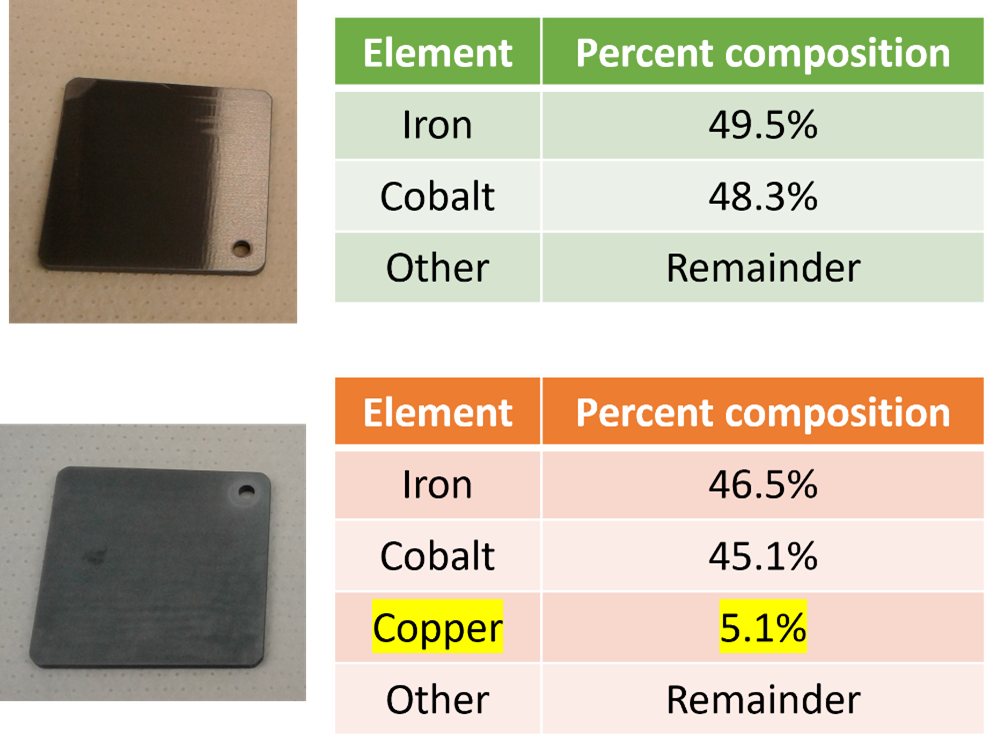
Figure 3: Metal coupon that had a different appearance and metal composition on each side. The top shows a surface that was not cut via EDM where the bottom shows a surface that was made via EDM.
**During the EDM process, small amounts of the cutting wire, which are typically made of copper or brass will embed themselves into the metal surface. Previous experiments show that even nitric acid treatments do not fully eliminate the copper contamination, and the result will be a poor coating appearance through our process. Customers with processes sensitive to copper contamination should be aware of potential surface contamination of stainless steel parts if stainless steel components used in their process were cut by wire EDM during manufacturing.
Conclusion:
Brass is the most common EDM wire material in use today, EDM can cause copper contamination of the substrate that is near impossible to remove using common cleaning techniques. The copper contamination can lead to silicon nanowire or other detrimental growth modes in our coating process, causing the coating to appear dirty and unacceptable. SilcoTek recommends that customers do not use EDM to machine their parts. If utilizing EDM is unavoidable, it is recommended that molybdenum or tungsten wire, which do not show deleterious effects, be used rather than copper or brass wires. If you are unsure of how to minimize the impact of wire EDM contamination, contact our Technical Service Team. We'll be happy to discuss your application.
Stay in touch with the latest in material science. Subscribe to our email and blog, or follow us on LinkedIn.

*image credit BobCAD-CAM.com
**© Copyright Triad National Security, LLC. All Rights Reserved (https://www.lanl.gov/resources/web-policies/copyright-legal.php)