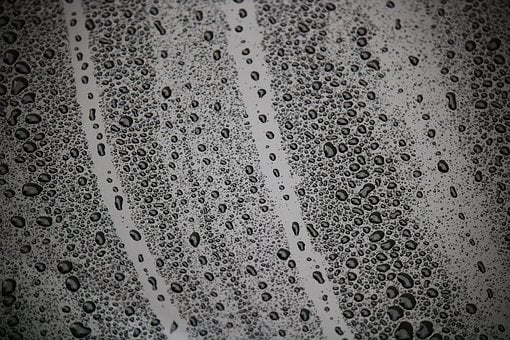
Coating aluminum with a silicon CVD coating can present significant material challenges. In this blog post we'll discuss the latest developments in applying our coatings to aluminum.
Improve Aluminum Corrosion Resistance and Inertness
The physical properties of chemical resistant aluminum (Al) alloys are versatile and ideal for use in a variety of manufacturing or industrial applications. These unique properties, however, can present challenges to surface treatment providers like SilcoTek®. Aluminum is weakened at temperatures in excess of 100° C. Go to our Coating Aluminum web page to learn more.
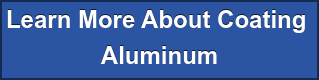
Because of the temperature related strength limitations associated with aluminum; SilcoTek does not recommend coating cylinders or any other aluminum product that will be pressurized or used in high stress applications. But there are many low stress applications where aluminum corrosion resistance and inertness is needed. In this blog post we'll discuss recent coating developments relating to improved corrosion resistance of 6000 series and 5000 series aluminum.
In this blog post you will learn:
- How to improve the corrosion resistance of 5000 series and 6000 series aluminum.
- How a new coating, optimized for aluminum, performs in corrosion tests.
- How coated 5000 series aluminum compares to 6000 series aluminum in corrosion studies.
|
Background
While stainless steel is naturally compatible with SilcoTek’s CVD chemistry and fosters a smooth amorphous silicon film growth (preferred), aluminum interacts very differently with the CVD process, i.e. they not only induce silicon nanowire growth but also catalyzes the amorphous-to-crystalline transition so that the deposited film contains a mixture of amorphous and microcrystalline silicon.
These growth abnormalities usually manifest as cosmetic coating defects (dark haze, dirty finish, grainy appearance, etc.), and as a result, require SilcoTek to employ special handling procedures for aluminum alloys to control undesirable growth patterns. These procedures have worked well for most aluminum alloys, with the exception of the 5000-series.
SilcoTek has been developing a new process aimed at improving coating results on aluminum substrate in general. The new process, developed by SilcoTek’s R&D team, involves a newly developed CVD process that was designed to address the interface challenges encountered in coating aluminum with the Silco-line of coatings. The new CVD process will be referred to as RD12 here as the coating is still in the research and development phase.
Coating Aluminum, Experimental
Identical 5000 series aluminum test coupons were sourced. Once cleaned, the coupons were divided into three groups, with each group receiving a different coating for comparison, i.e. standard SilcoNert® 2000 (SN2000), RD12, and corrosion resistant coating Dursan®. Every group contains both the 5083 and 5456 alloys. Figure 1 (below) shows the visual appearance of the coated coupons. The standard SN2000 coating still exhibits a dark hazy appearance on both alloys, with streaks of dark brown discoloration near the edges. This is reminiscent of the initial coating attempt on the 5183 alloy discussed earlier, showing that the new surface preparation chemistry alone did not transform the visual output for SN2000 coating on 5000-series aluminum.
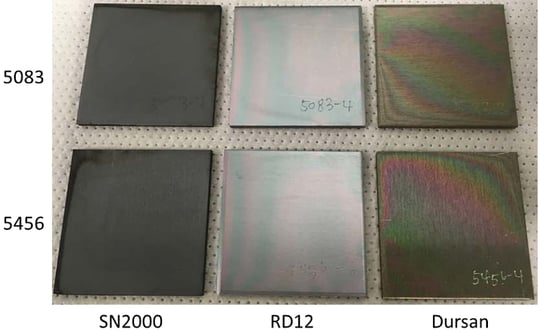
On the other hand, the experimental RD12 coating gave the familiar rainbow appearance expected on coated stainless steel parts, indicating that the RD12 process, without relying on any special handling procedures, was able to suppress the growth abnormalities associated with aluminum alloys, and deposit a smooth amorphous silicon coating similar to that on stainless steel substrate. The Dursan coating also turned out well visually (Figure 1 on the right).
Corrosion Testing
Polarization resistance scans were carried out in 5% HCl solution to test the corrosion resistance of the coated coupons, and the results were shown in Figure 2. Average value of the 5083 and 5456 alloys for each coating type is reported, as these two alloys performed similarly. The Dursan coating showed no benefit over the uncoated samples, whereas the RD12 reduced the corrosion rate by about half. A much larger benefit from the RD12 coating was observed when 6061 aluminum alloys were tested (Figure 3), indicating that the high Mg content in the 5000-series is likely limiting the extent of the coating’s benefit.
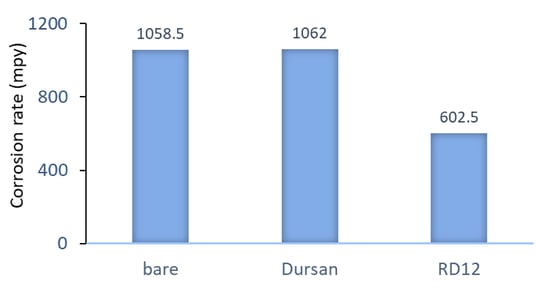
Figure 2: Corrosion rate in mils per year (mpy) obtained from polarization resistance scans in 5% HCl solution (20 minutes immersion) on 5083 and 5456 aluminum alloys
Figure 3: Corrosion rate in mils per year (mpy) obtained from polarization resistance scans in 5% HCl solution (20 minutes immersion) on 6061 aluminum alloys
Conclusion
The RD12 process was found to work very well for 6061 Al. The new coating delivered better visual output and smooth surface coverage on the 5000-Al coupons, but the corrosion performance did not match that on 6061 Al. The SilcoTek R&D team will continue to optimize and revolutionize corrosion resistant coatings for improved material performance in the most challenging applications.
Want to learn more about about how our coatings perform in your application? Go to our Coating Applications Page, or ask the experts on LinkedIn.
