SilcoTek® occasionally receives parts for coating that already have silver plating on them. Our materials compatibility guide lists silver plating as a substrate that “needs more information” because results over silver plating have varied depending on the quality of the silver plating itself. We will analyze and compare several different silver-plated parts and show how the purity of silver plating affects the outcome of SilcoTek’s CVD coating.
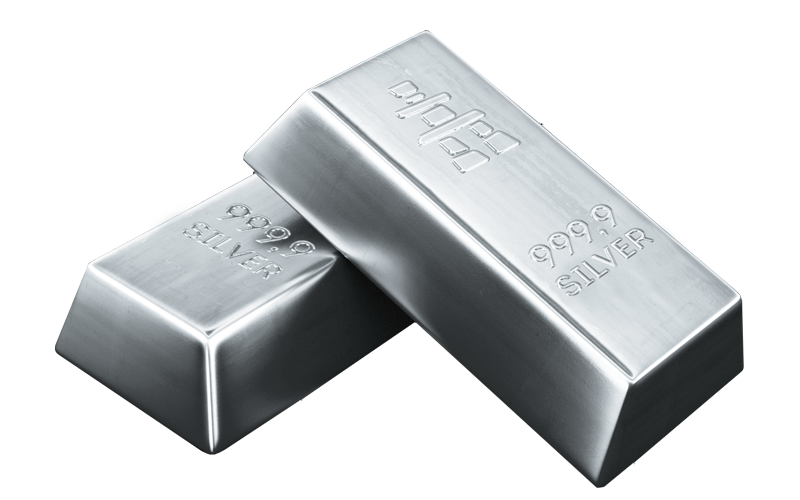
How CVD Coatings are Affected by Silver Plating
Sometimes, SilcoTek receives parts for coating that already have silver plating on them. Silver plating has generated inconsistent coating results historically, and for that reason was placed as a substrate that customers should contact SilcoTek to review on our materials compatibility guide. The reason for this variability hinges on the quality (or purity) of the silver plating, as silver plating may often contain other non-silver elements that can interfere with SilcoTek’s CVD (Chemical Vapor Deposition) process. In this blog post, our researchers will analyze and compare several different silver-plated parts coated by SilcoTek and demonstrate how impurities in the plating may compromise the coating and cause non-conforming results. Pure silver coating, on the other hand, is shown to be compatible with SilcoTek’s coating process and deliver good results.
Experiment
Silver-plated stainless steel screws were received as part of a customer order and processed via the standard SilcoNert 2000® (SN2000) coating process. Silver-plated 316 stainless steel VCR gaskets (part numbers SS-4 VCR-2 and SS-8-VCR-2) and compression nuts (part number SS-8M0-NFSET) were purchased from Swagelok® and processed via the standard SN2000 coating process. Silver plating is commonly used on these parts to impart good lubricity and anti-galling properties. SEM (Scanning Electron Microscopy) and EDS (Energy Dispersive Spectroscopy) analyses of the coated and uncoated parts were performed using Thermo Fisher Scientific Apreo SEM equipment at Penn State University.
Results
Typical SN2000 coating on stainless steel parts exhibits nice rainbow patterns like shown in Figure 1 (left). The customer-supplied screws, however, had an unappealing brown and flaky appearance that usually implies an incompatible substrate and would fail SilcoTek’s visual QC inspection (Figure 1, right). This is contrary to the results of a previous batch of silver-plated screws from the same customer, where everything coated successfully and passed inspection.
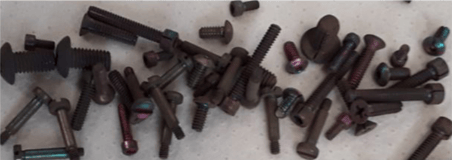
Figure 1: typical SN2000 output on SS parts (left), and SN2000 coating on a batch of customer-supplied silver-plated SS screws (right).
With the customer’s permission, we analyzed a few of the coated screws with SEM and EDS to look for answers. We found that instead of the smooth and conformal film coverage expected from our normal SN2000 coating, the screws were covered by clumps of nanowires made of silicon (Figure 2, left). EDS analysis also revealed a surprisingly high copper content in the substrate, higher even than silver, the plating metal that is supposed to cover the surface of the base stainless steel (Figure 2, right). The presence of copper explains the abnormal coating results experienced by these screws, as copper and copper alloys (such as brass and Monel) are known to catalyze nanowire growth of silicon (i.e. one-dimensional wire growth instead of a planar film growth that covers the entire substrate surface), and for that reason were listed as incompatible substrates on SilcoTek’s website.
Figure 2: SEM (left) revealed that instead of a smooth film, silicon nanowires were found on coated screws (10K magnification), and a very high copper concentration was detected in the substrate via EDS (right).
SilcoTek routinely coats Swagelok VCR gaskets and compression fittings without issue, and these parts typically come with silver plating on them to help prevent galling under elevated temperatures. An experiment was carried out to process and analyze a few of these parts in the same manner as the screws saw, to provide a comparison study of successful coating onto silver plating. Figure 3 shows the healthy appearance of these test parts after SN2000 coating, which would all have passed our QC inspection. The compression nut was cut open prior to the coating process to allow access to the silver-plated threads on the inside for easy inspection and analysis.
Figure 3: SN2000 coated Swagelok compression nut and VCR gaskets appear normal (all silver-plated).
SEM and EDS analyses were performed on the coated as well as uncoated Swagelok test parts to examine if there is similar nanowire growth on these parts. Figure 4 combines the uncoated and coated SEM images of each test part next to one another for comparison. No silicon nanowire growth was observed on any of the coated parts. The uncoated surfaces showed various degrees of roughness, while the coated surfaces appeared smoother in general in comparison. The SEM image of the coated compression nut showed some silicon particles that could not be completely removed via post-cleaning methods (i.e. CO2 blow off and sonication). Silicon dust particles are a side product of the SN2000 CVD deposition reaction and can sometimes adhere to a coated surface.
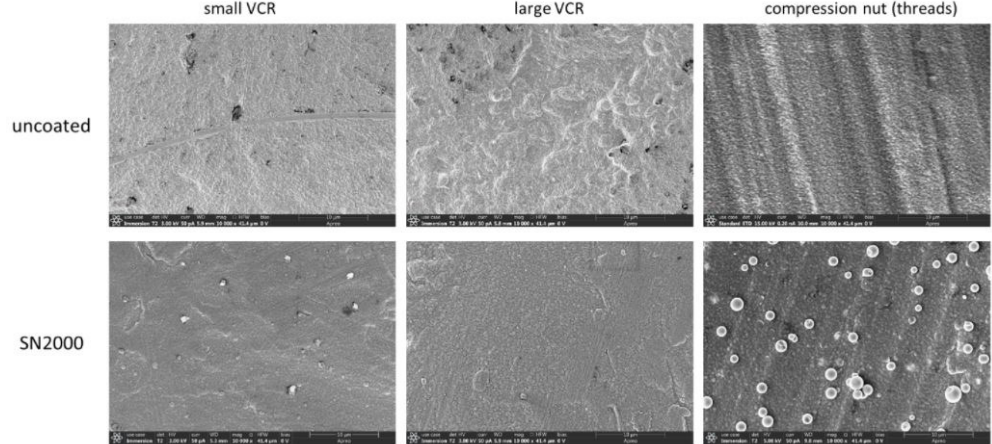
Figure 4: uncoated (top) and SN2000 coated Swagelok VCR gaskets and compression nut (all silver-plated) under SEM (all taken at 10K magnifications); no silicon nanowires were found.
EDS analysis on the uncoated Swagelok parts verified minimal amounts of impurities in the silver plating. Figure 5 shows the EDS scan results for each sample, revealing primarily silver (Ag) as the plating material and iron (Fe), nickel (Ni), chromium (Cr) from the underlying stainless steel metal. Carbon (C) may be from adventitious carbon picked up from either the air environment or sample preparation process, which is commonly encountered in EDS analysis. Stainless steel metals sometimes contain small amounts of aluminum (Al) and silicon (Si) which may account for the presence of these two elements in low quantities. Noticeably, no copper was detected in any of the three samples, testifying to the higher purity of the silver plating used on these Swagelok test parts.
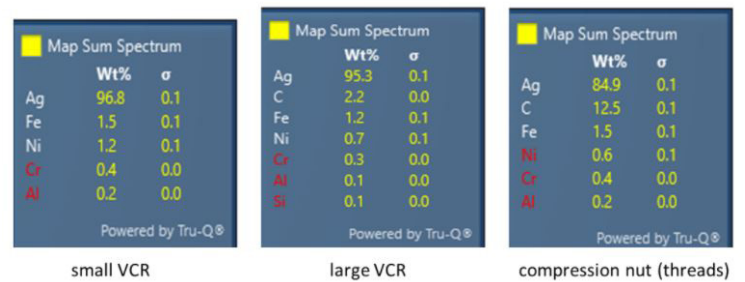
Figure 5: EDS analysis shows the elemental compositions of the three uncoated Swagelok test parts, verifying high purity of the silver plating.
Conclusion
In this blog post, we examine the compatibility between silver plating and our SilcoNert coating process. It was found that a pure silver plating is compatible with the coating and delivers good results. On the other hand, if the plating contains impurities such as copper, the coating results are often compromised due to silicon nanowire growth catalyzed by the impurities. Copper is not an unusual impurity in silver plating because copper and copper alloys are among the most common metals to receive silver plating. They can leave residues in the plating bath and contaminate the next batch of products if a fresh bath is not used. In addition, some platers apply a copper or nickel (or both) undercoat before the silver plating to help with film adhesion. Both copper and nickel will cause incompatibility issues with SilcoTek’s coating process. To ensure the best coating outcome, SilcoTek recommends customers to use a high quality, pure silver plating when sending parts in for coating.
To download the PDF version of this technical insight, please click here.
