A research group from the University of Illinois at Urbana-Champaign recently published their research paper, Jet fuel oxidation on conventionally and additively manufactured metallic tubes, in Applied Thermal Engineering. The paper explores their work regarding the benefits of additive manufacturing in aerospace and the risks associated with increased surface roughness. SilcoTek coatings were used to reduce surface roughness and withstand high heat applications, enabling easier additive manufacturing without unwanted fouling effects.
SilcoTek's Dr. Min Yuan interviews the research team from UIUC about their experiments and their interactions with SilcoTek coatings in the newest installation of a video interview series by SilcoTek- SilcoTalk.
Researchers used SilcoTek's coating, Silcolloy 2000, to "ensure with better adhesion to the substrates, forming a layer of hydrogenated, amorphous silicon (a-Si:H) on the inside of the tubes." They cited Silcolloy with "minimizing jet fuel degradation significantly, allowing researchers to utilize additive manufacturing for aircraft thermal management component manufacture by alleviating concerns related to fuel blockage and performance deterioration stemming from surface deposition."
Additively manufactured materials (aka 3D printing) are used in the aviation industry due to their flexible design and lightweight nature, which makes them perfect for creating complex parts that enhance performance and aerodynamics. Reductions in weight and increases in strength not only facilitate better safety protocols, but higher efficiency as well.
Researchers and students at UIUC tested whether the additively manufactured metallic heat exchanger tubes would decrease fouling in their aviation platform. In using additively manufactured tubes, there is an increase in surface roughness, which caused concern for additional jet fuel oxidation and fouling. They tested regular and additively manufactured 316 stainless steel, aluminum alloy AlSi 10Mg, titanium, and Inconel 625 tubes to resist carbonaceous solid deposits via the Jet Fuel Thermal Oxidation Test (JFTOT) method, which is used to determine jet fuel instability.
Silcolloy 2000 coated additively manufactured tubes in various substrates. This color variation shows that the same coating applied to different substrates can have different visual appearances, even with similar coating thicknesses.
Results
Comparisons between regularly manufactured and additively manufactured parts were tested with coating and without coating. The graphs below show the estimated carbon deposition thickness (left) and weight percentage of carbonaceous deposits (right) on the internal surface of the tubes after the test (left) and before and after the test (right). Due to the increase in surface roughness, the additively manufactured metal tubes experienced greater surface deposition than their traditionally manufactured counterparts. Aside from copper, the titanium additively manufactured tube had the thickest estimated carbon deposition among the four substrates. With the use of Silcolloy 2000 coating, the additively manufactured tubes performed better at resisting carbon deposition.
Even though some additively manufactured tubes showed greater carbonaceous depositions than the traditional parts, the design variability, cost savings, and high strength-to-weight ratio of the additively manufactured parts can certainly outweigh the regular alternatives.
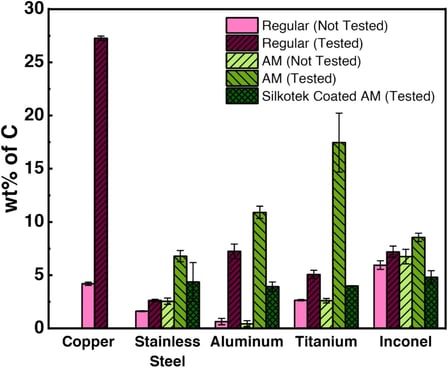
Watch the video to see what the research students had to say about how SilcoTek's coatings helped in this experimental research.
Have questions about your applications or research projects? Reach out to our knowledgeable team today!
Reference:
Dipto, M. J., Rabbi, K. F., Thukral, T. S., & Miljkovic, N. (2025, February 15). Jet fuel oxidation on conventionally and additively manufactured metallic tubes. Applied Thermal Engineering. https://www.sciencedirect.com/science/article/pii/S1359431124028230?via%3Dihub&utm_campaign=7184022-General%20Promotion&utm_medium=email&_hsenc=p2ANqtz-_TlQTyNVffF0jRBxdoGN7QKCBUVdaTZjALzNWaWFpApPpfmXg2QyN9nEoW2eXwEf7mEdLK_s0wIjG8k78WwItT7wcvXA&_hsmi=349315694&utm_content=349315694&utm_source=hs_email