What is a Heat Exchanger and How Do Coatings Help?
Heat exchangers are devices designed to transfer heat between two or more fluids without mixing them. They are commonly used in various industries, including power generation, chemical processing, HVAC (heating, ventilation, and air conditioning), automotive, and refrigeration. The primary function of a heat exchanger is to either absorb or dissipate heat from one fluid to another, improving energy efficiency and controlling temperatures within systems.
SilcoTek coatings help to mitigate particulate build up on the surface of the tubes that transport the fluids. By avoiding coking and fouling from that build up, it allows the heat exchanger to perform at its best, which means less equipment maintenance and replacement, decreased down time, increased output, and better ROI than other exotic alloys.
SilcoTek Coatings: The Science Behind the Solution
SilcoTek employs a chemical vapor deposition (CVD) process to create high-performance coatings that can be applied to a variety of metal substrates. The most notable anti-stiction SilcoTek coatings for anti-fouling and anti-coking applications are SilcoKlean®, Dursan®, and Notak®. We address fouling by 2 different methods: barrier approach (SilcoKlean) and chemistry approach (Dursan and Notak).
SilcoKlean:
- Designed specifically to reduce coking and fouling.
- Is a functionalized barrier coating process to deposit a flexible, amorphous silicon layer.
- This layer diffuses into the metal substrate, creating a surface that is resistant to carbon buildup and harsh chemical environments.
Dursan:
- Provides a robust barrier against corrosive and fouling agents.
- Coated surfaces exhibit high durability, chemical inertness, and hydrophobic properties, which prevent material adherence and simplify cleaning processes.
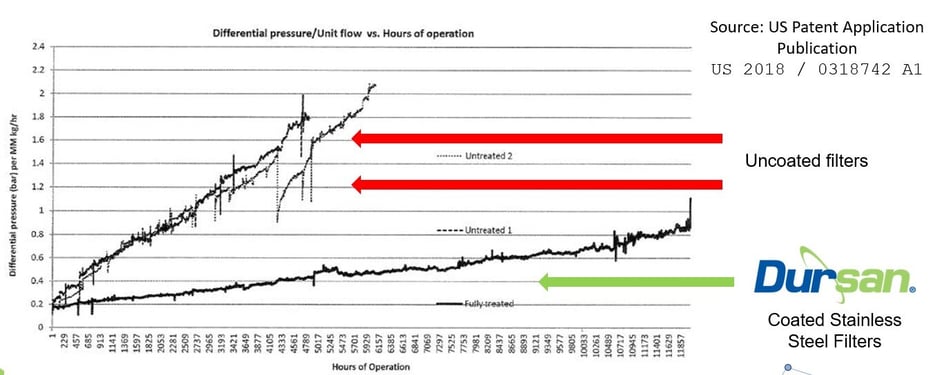
Notak:
- High contact angle (see below) which allows for low surface energy and mitigating particulate build up.
- Provides superior anti-fouling properties by minimizing the adhesion of particulate matter and biological materials.
- Enhances process cleanliness and efficiency.
- Reduces cleaning time and maintenance requirements.
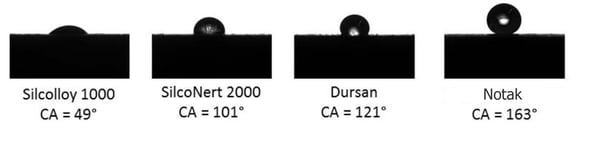
How SilcoTek Coatings Work
SilcoTek coatings are engineered to address specific challenges related to fouling and coking, common issues in many industrial processes. These coatings enhance surface properties by modifying the surface energy of substrates, making them less attractive to foulants and coke precursors. Additionally, they offer excellent chemical resistance, preventing chemical reactions that lead to fouling and coking. With thermal stability, these coatings can withstand high temperatures, maintaining their protective properties and preventing thermal degradation that often leads to coking. Their durability is ensured through a strong bond formed during the CVD process, providing extended protection against fouling and coking. By reducing fouling and coking, these coatings help maintain the efficiency of heat exchangers, reactors, and other equipment, leading to lower energy consumption and operational costs.
Applications in Industry
-
Petrochemical and Refining:
- Furnaces and Heat Exchangers: SilcoKlean reduces coke formation on furnace walls and heat exchanger tubes, improving heat transfer and reducing maintenance.
- Pipelines: Dursan coating helps in maintaining clean pipelines by preventing fouling from crude oil and other hydrocarbons.
-
Aerospace:
- Fuel Systems: SilcoTek coatings prevent carbon buildup in jet fuel systems, ensuring smooth operation and reducing the risk of blockages.
-
Power Generation:
- Boilers and Turbines: The coatings protect against fouling and corrosion, thereby enhancing efficiency and reducing downtime.
Case Study: Jet Fuel Fouling Experiments
In a study to mitigate carbon deposition by autoxidation of jet fuel, SilcoKlean 1000 coating was applied to stainless steel tubes and tested under controlled conditions. The results demonstrated significantly reduced carbon deposition compared to uncoated and other coated samples, validating the effectiveness of SilcoTek coatings in high-temperature, high-fouling environments. According to the University of Illinois, Urbana-Champaign, the SilcoKlean coated stainless steel had greater than 10x less carbon build-up in comparison to bare stainless steel. See the visual differences in the before (left) and after (right) below! Read their study HERE.


Images above are from University of Illinois, Urbana-Champaign's study on carbon deposition mitigation with coatings.
Solving Fouling Problems
Even under extreme pressure and temperature, SilcoTek coatings significantly improve corrosion resistance, allowing for more efficient and easy release of particulate and extending the life of your equipment.
Coating features and benefits include:
- Low surface energy, high contact angle surface
- Better wear resistance for higher durability, and erosion prevention
- Higher lubricity to improve operation
- Takes the place of release chemicals
- Prevent contamination by release chemicals and oxidation by-products in medical and electronic applications
- Does not transfer onto the plastic part during molding
- Eliminate diamond finish release problems by improving surface lubricity
- Improved corrosion resistance
Conclusion
SilcoTek coatings offer a reliable and effective solution to combat fouling and coking in various industrial applications. By enhancing surface properties, improving chemical resistance, and maintaining thermal stability, these coatings extend equipment life, improve efficiency, and reduce maintenance costs. With a new focus on heat exchanger applications, coatings are also beneficial to provide optimal performance and longevity in petrochemical processing, aerospace, and power generation.