One of the most common questions we get is: Can I recoat a part that’s already been treated with a SilcoTek coating? The answer is yes, but with important qualifications.
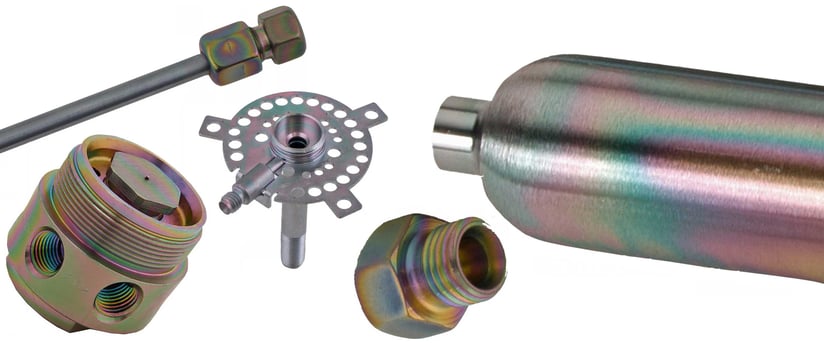
Why You Might Need to Recoat
Recoating may be necessary if:
- The coating has been damaged through use or cleaning
- Surface performance has degraded over time
- A different SilcoTek coating is now required for new application conditions
- You're reusing parts for a new process or project
In some cases, it may be more cost-effective or convenient to recoat a part rather than manufacture a new one.
What to Consider Before Recoating
Before you send parts back for recoating, here’s what to know:
1. The Original Coating Type
We can strip all coatings, but not all coatings can be recoated in the same way. For example:
-
SilcoNert® 2000: Can typically be stripped and recoated with no issue.
-
Dursan®: Can often be reapplied, but we’ll assess each part to ensure compatibility and performance.
- Siltride® 1000: This coating’s exceptional corrosion resistance and durability makes it the most intensive to strip and recoat.
2. The Base Material
Certain materials respond better to coating removal and reapplication than others. Stainless steel usually performs well in this regard, while some softer alloys may not.
3. Part Condition
We will evaluate the part for corrosion, deformation, contamination, or other damage that could affect recoating success. All stickers, PTFE, and other non-metallic materials should be removed prior to sending to SilcoTek for recoating. Please note that the recoating process will not fix any pitting, staining, or corrosion that has already occurred.
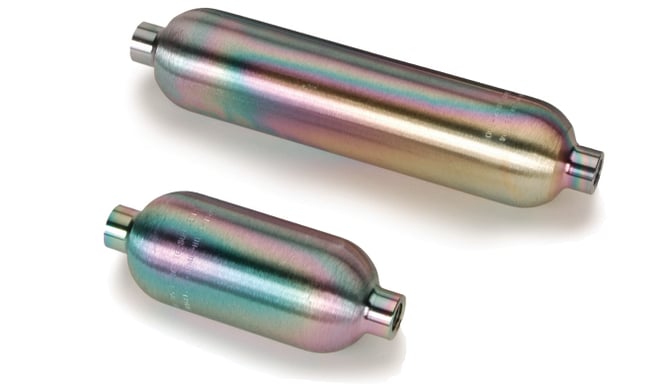
The Recoating Process
Here’s what happens when you return parts for recoating:
-
Initial Consultation and Evaluation: Please reach out to our technical service team so we can review the part history and application to determine recoating feasibility.
-
Coating Removal: The original coating is carefully stripped from the surface.
-
Surface Preparation: The part is cleaned, conditioned, and prepared for recoating to ensure maximum adhesion and performance.
-
Reapplication: A new coating is applied using our patented chemical vapor deposition (CVD) process.
Not all parts are good candidates for recoating. In some cases, it may be better to start with a new part to ensure optimal performance.
Recoating vs. Replacement: What’s Best?
While recoating can save time and money, it’s not always the best choice. If a part has been in service for years, or if performance issues have been observed, a replacement may offer better long-term results.
If you’re unsure, send us the part details and we’ll help you decide.
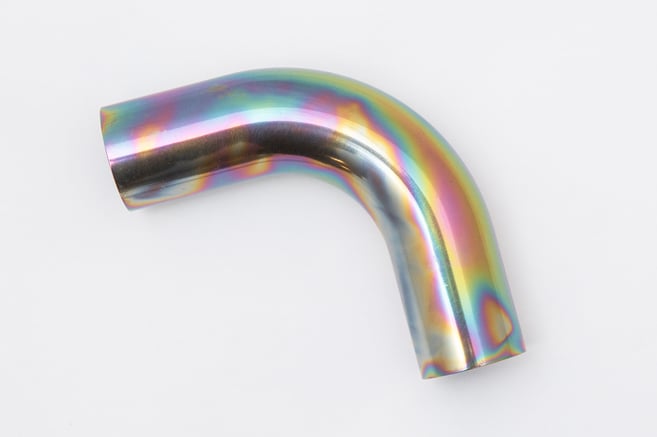
How to Start the Recoating Process
Ready to get started? Contact our team or submit a recoating inquiry here.
Please include:
- Part material and dimensions
- Original coating type and date (if known)
- Current application or reason for recoating
- Any known wear, corrosion, or contamination
- Quantity
Reach Out to Us!
We’ll evaluate your request and let you know the best path forward. Our technical team is always here to help. Whether you’re planning a recoating or exploring new coating options, we’ll guide you through the process to get the most out of your surfaces.