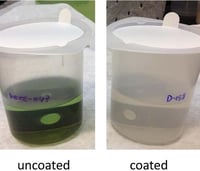
Process analyzers and process sampling systems can be exposed to challenging corrosive environments both internally and externally. Many sample streams contain reactive compounds that reduce equipment lifetime or require extended preventative maintenance.
How To Prevent Chloride Corrosion In Process Sampling
Some systems are exposed to environments such as sea water and salt spray, which cause rapid deterioration of equipment, requiring extra cost to keep them operating. Or the sample stream itself can be highly corrosive like streams found in stack or flare systems.
The challenge is the system must convey the sample without adsorption or contamination while somehow protecting itself from corrosion. In short, the sample system must be both corrosion resistant and inert.
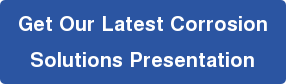
For systems that are required to give accurate, reliable and repeatable data in such conditions, the cost of upkeep and maintenance can be excessive in both dollars and lost yield or productivity due to plant outages.
How to prevent chloride corrosion?
Sample system corrosion solutions can range from inexpensive paints up to costly super alloys. All have the objective to increase the lifetime of components in salt and/or chloride containing environments. Unfortunately, 300 series stainless steel won't make the grade alone. Depending on the specific alloy, 300 series exposure to chlorides can range in durability from a few hours or days to a year or so before failure; not a great model for reliability. Generally, high levels of chlorides will spell trouble for 300, 304, or 316 stainless steel.
The solution to chloride corrosion
Dursan® offers an inert and corrosion resistant coating solution to stainless steel durability problems. The rare instance where one solution solves 2 problems!
First let's look at inertness performance; the graph below demonstrates the very low adsorption rate of Dursan. Trace sulfur and other active compounds don't react with the surface; improving inertness response by orders of magnitude.
Chloride Exposure
Table I provides the results obtained from ASTM G31 testing. This method is an immersion test for 24 hours in a 6M hydrochloric acid (HCl) (18%) solution at room temperature and pressure. After immersion, differential weighing allows the amount of material loss to be determined. The Dursan coated surface significantly improves chloride corrosion resistance.
Table I: Weight loss after 24 hour exposure to 6M (18%) HCl
24hr; 6M HCl; 22ºC
|
304 SS
|
Silicon coated
|
Dursan coated
|
MPY (mils-per-year)
|
389.36
|
16.31
|
1.86
|
Improvement Factor
|
---
|
23.9
|
209.8
|
Comparing multiple coupon materials, Dursan® demonstrates similar performance to Hastelloy®
.jpg?t=1491406345027&width=398&name=corrosion_comparison_in_HCl_(4).jpg)
Salt Spray Exposure
Salt spray immersion tests show Dursan significantly improves salt corrosion resistance, extending the useful life of 300 series stainless steel from days or weeks to years.
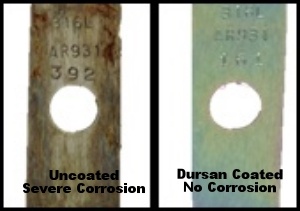
EIS data ( Electrochemical Impedance Spectroscopy) show Dursan remains pinhole free after over 250 days of salt spray exposure. Stainless steel exhibits significant pin holing after a few days.
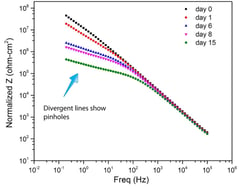
Stainless Steel: Significant Pinholes
|
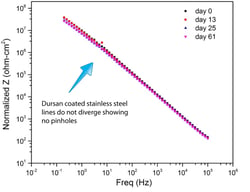
Dursan: No Pinholes
|
After 247 days, Dursan continues to be pinhole free.
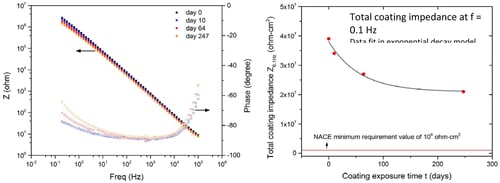
Why is this important?
If you're sampling in a reactive environment, it makes sense to avoid sample contamination and damage to the sample pathway by coating wetted surfaces with an inert, corrosion resistant coating. If you're a semiconductor manufacturer or other high purity processor, Dursan helps to avoid product contamination and extends the life of process equipment.
Coat the entire sample pathway.
Dursan® can be applied to the entire wetted pathway, or wherever corrosion can damage processes or products .
Coat:
Regulators |
Valves and fittings |
Tubing |
Sample Cylinders |
High purity gas delivery systems |
Semiconductor gas manifolds |
Process sample probes |
Glass and ceramics |
Learn where to buy inert and corrosion resistant products for your process sampling project.
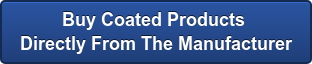