Stainless steel is typically specified because of its ability to resist corrosion in a variety of environments. Unfortunately, stainless steel is not fully stain or rust-proof, it is just more resistant to corrosion that's why it's called stain less steel.
Exposure to corrosive process fluids and cleaners, high humidity or high salinity environments such as sea water can remove the native protective layer (chromium oxide) and can cause stainless steel corrosion. Removing surface rust from surfaces improves the appearance, but it's importance goes beyond the decorative. Rust, left unchecked, can lead to pitting and structural damage to products and components and can impact the performance of instrumentation, contaminate flow paths, and impact reliability.
So what is the most effective way to remove rust from stainless steel?
Before Rust Removal
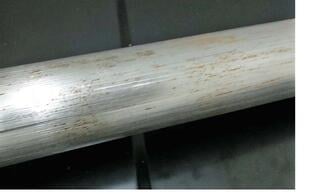
|
After Rust Removal
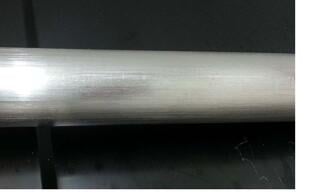
|
The best method will effectively remove surface rust, but minimize impact to the bulk stainless steel substrate. Abrasive techniques like sandblasting, abrasive pads, or abrasive rubbing compounds can damage the surface finish and embed particulates into the surface. Two methods used by SilcoTek® to remove surface rust employ weak acids.
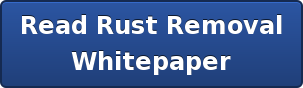
Phosphoric Acid
Phosphoric acid will dissolve iron oxide without attacking the other components of the steel (chromium and chromium oxide, nickel, and iron). The rust is dissolved by the following reaction: 2 𝐻3𝑃𝑂4 + 𝐹𝑒2𝑂3 → 2 𝐹𝑒𝑃𝑂4 + 3𝐻2𝑂
Phosphoric acid is readily available from a number of commercial suppliers (SilcoTek uses 85% ‘food grade’) and it can be used with no dilution because of its non-aggressive nature. Clean up after acid treatment is done by thoroughly rinsing parts in deionized water to remove any remaining acid on the surface. If deionized water is not available, rinse with distilled water.
Unfortunately, this technique is not 100% effective on all the forms of iron oxide and other surface preparation treatments could be necessary.
Acetic Acid
The reaction with acetic acid is often slower than phosphoric acid and can be a better choice when the underlying corrosion/staining affects a larger percentage of the substrate. Read the entire report. Following the acid exposure, parts must be rinsed thoroughly with deionized water to assure complete removal of trace acid.
Watch our sonication video to see how to sonication removes particulates.
Once the rust is gone, keep it off. Ways to prevent stainless steel rust.
Once the rust is gone, use high durability silicon coatings, like Silcolloy® and Dursan® , to improve the corrosion resistance of stainless steel and other alloys. Read more about corrosion solutions.
Process analyzers and process sampling systems can be exposed to challenging corrosive environments both internally and externally. Many sample streams contain reactive compounds that reduce equipment lifetime or require extended preventative maintenance.
Some systems are exposed to environments such as sea water and salt spray, which cause rapid deterioration of equipment, requiring extra cost to keep them operating. Or the sample stream itself can be highly corrosive like streams found in stack or flare systems. For systems that are required to give accurate, reliable and repeatable data in such conditions, the cost of upkeep and maintenance can be excessive in both dollars and lost yield or productivity due to plant or system outages. That's why it's important to find ways to improve the corrosion resistance of components rather than just constantly removing rust from surfaces.
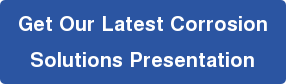
Salt Spray Exposure Testing
Salt spray immersion tests show Dursan significantly improves salt corrosion resistance, extending the useful life of 300 series stainless steel from days or weeks to years. After 250 days of salt spray exposure the Dursan coated coupon looks like new while the uncoated stainless steel coupon is rusted.
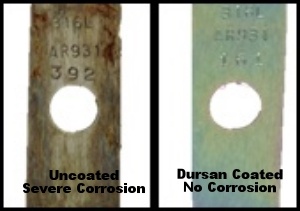
EIS data ( Electrochemical Impedance Spectroscopy) show Dursan remains pinhole free after over 250 days of salt spray exposure. Stainless steel exhibits significant pin holing after a few days as seen by the divergent impedance plot on the left. The Dursan graph (right) does not change, indicating no change in pinholes.
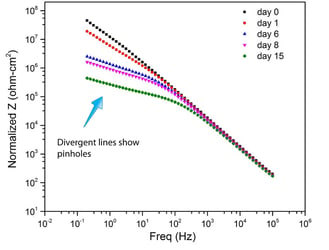
Stainless Steel: Significant Pinholes
|
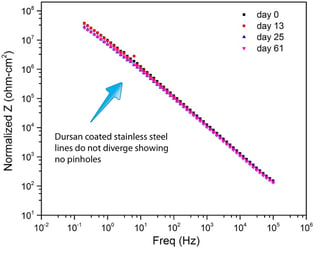
Dursan: No Pinholes
|
After 247 days, Dursan continues to be pinhole free.
Acid Exposure
Depending on the specific alloy, 300 series exposure to aggressive acids can range in durability from a few hours or days to a year or so before failure; not a great model for reliability. Generally, high levels of acid will spell trouble for 300, 304, or 316 stainless steel.
Table I provides the results obtained from ASTM G31 testing. This method is an immersion test for 24 hours in a 6M hydrochloric acid (HCl) (18%) solution at room temperature and pressure. After immersion, differential weighing allows the amount of material loss to be determined. The Dursan coated surface significantly improves chloride corrosion resistance.
Table I: Weight loss after 24 hour exposure to 6M (18%) HCl
24hr; 6M HCl; 22ºC
|
304 SS
|
Silicon coated
|
Dursan coated
|
MPY (mils-per-year)
|
389.36
|
16.31
|
1.86
|
Improvement Factor
|
---
|
23.9
|
209.8
|
Comparing multiple coupon materials, Dursan® demonstrates similar performance to costly super alloys. After 24 hours of exposure to concentrated hydrochloric acid, the Dursan coupon compares favorably to alloys. The best part? Dursan can be applied to stainless steel without significantly impacting durability or tolerances. So you can use existing parts or designs and enhance the corrosion performance without redesign or re engineering.
Conclusion:
In some ways the easy part of corrosion prevention on stainless steel is removing the rust. The hard part is keeping the rust off without costly component redesign or re manufacture. You can keep your components and improve corrosion resistance by bonding a high tolerance, high durability, corrosion resistant coating to the surface after rust removal. Remember to use the least damaging but still effective rust removal and cleaning method on parts. Highly aggressive rust removal agents and cleaners can etch part surfaces, creating sites for renewed corrosion or damaging surface finish, seal areas or flow paths. If it is not possible to apply the removal techniques at your facility, SilcoTek’s sales group can provide a quote for the acid cleaning process upon request. Click here to get a coating or cleaning quote.
Want to see our coating fight corrosion? Watch our corrosion video!