This week, we're featuring the third book in our Ultimate Guide E-book series, Managing Challenging Sampling Environments.
Click the links to see the blog posts on books one and two. To download the third e-book, click below.

Hydrophobic Coatings Improve Analytical Systems
A single drop of water may appear to be harmless, but it can have a huge impact on the durability and performance of analytical and process monitoring systems. Moisture condensation in sample delivery, analytical GC columns, and process systems can cause corrosion as well as loss of sulfurs and reactive compounds. Even trace amounts of water in process sample and transport systems can have a major impact on product yield and quality in refining, petrochemical, polymer, and semiconductor manufacturing applications, amongst others.
Coatings to Repel Moisture
SilcoTek hydrophobic coatings repel water, dry quickly and don’t retain moisture, resulting in greater sensitivity and durability in sample transfer and analytical systems. SilcoTek’s inert, high temperature barrier coatings prevent surface interaction between critical flow path surfaces and your product. Dursan® improves moisture repelling properties of stainless steel, glass, and ceramic surfaces by 60% or more when compared to uncoated stainless steel. Comparative contact angle tests show stainless steel demonstrates limited moisture repelling properties with a low 20 degree contact angle. Moisture will wet the surface and “stick” in surface irregularities, causing analyte solvation and test errors. Dursan-coated surfaces exhibit exceptional moisture resistance and provide a 100+ degree contact angle. Dursan-coated surfaces prevent moisture contamination and solvation.
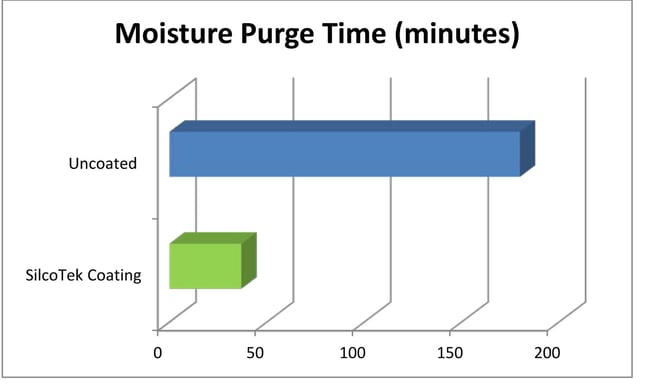
Coatings benefits include:
- Less water accumulation and retention in analytical systems.
- Faster system purge. Water is repelled so it’s easily removed.
- Fast recovery. Fast-drying surface allows for quicker response.
Maximize Hydrophobicity
To improve hydrophobicity in analytical systems, coat the entire flow path, purge gas system, and calibration flow path. Common parts include:
- Regulators
- Fittings
- Valves
- Tubing
- Filters
- Analytical components
- Probes
- Moisture sensors
Managing Sulfur - Reliable Results without Adsorption
Comparative testing exemplifies the extent of H2S adsorption and decomposition on stainless steel. After only 1 hour nearly 100% of the sample was lost due to reactivity of the stainless steel, aluminum, or carbon steel surface. A December, 2002 study by American Mobile Research, Inc. compared the surface inertness of various sample cylinder surfaces used in sulfur sampling in natural gas and natural gas liquids. The study concluded that SilcoNert-lined surfaces exhibited very low sulfur adsorption over 1 hour and 72 hour comparisons.
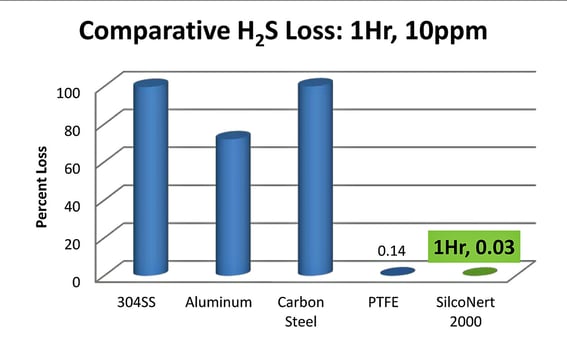
How to Manage Sulfur in Process Analytical Systems
To prevent adsorption and surface reactivity of stainless steel and assure maximum stability in stack and flare monitoring, use SilcoNert®-coated flow paths to maintain sample quality, even after 14 days of exposure. The graph below shows repeated sample cylinder tests using low level, 11 part-per-billion, sulfur samples. The results show consistent levels of sulfur throughout the sample period. Inert coatings are an ideal solution to sample cylinder stability problems.
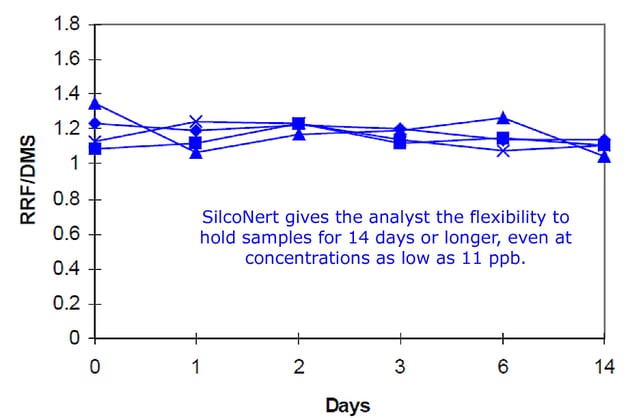
Coat the Entire Sampling Pathway
- Probes
- Fittings
- Heat trace tubing
- Regulators
- Filters
Sampling Mercury and Ammonia
Continuous emission monitoring systems (CEMS) and sorbent tube samplers can be degraded or compromised by the loss of mercury species and ammonia on reactive sampling surfaces. Reactions and adsorption on inner surfaces of transfer and monitoring equipment cause significant failures in system reliability. An inert flow path will prevent stainless steel surface interaction with active and reactive compounds during sampling and transfer. Without an inert coating like SilcoNert®, analyzers will produce inconsistent or substandard results, such as:
- Erratic calibration
- Long delays in response
- Inaccurate results
- False positive or false negative readings
- Lost mercury in sample storage equipment
Comparative Mercury Tests
Stability data (below) compares SilcoNert® 2000-treated 304 grade stainless steel gas sampling cylinders (Swagelok®, Solon OH) and untreated sample cylinders. Each cylinder was filled with 8 ug/m3 of elemental mercury (approximately 1 part per million) (Spectra Gases, Alpha NJ). The mercury in each cylinder was measured over time to determine the changes in concentration. The SilcoNert-treated sample cylinders showed minimal loss, while the uncoated cylinders lost 80% of the sample over the test period.
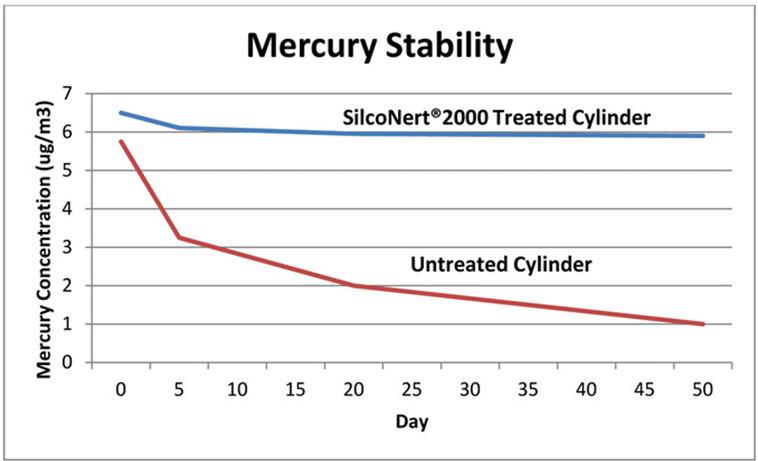
Comparative Ammonia Testing
Trace ammonia sampling in automotive, refinery, and industrial applications can be tedious at best and impossible under worst case conditions. If you’ve ever experienced progressively erratic and irrelevant results when testing for trace ammonia, Bertrand S. Lanher, PhD. with Sensors, Inc. may have an answer to your problem. A recent study by Dr. Lanher compared stainless steel, PTFE, and SilcoNert® 2000-coated tubing (noted as Sulfinert) for relative inertness, adsorption, and retention of trace level NH3.
Dr. Lanher’s test results (below) show that a relatively short 3 meter length of uncoated transfer tubing can be adsorptive and can result in significant delay in response and test errors.
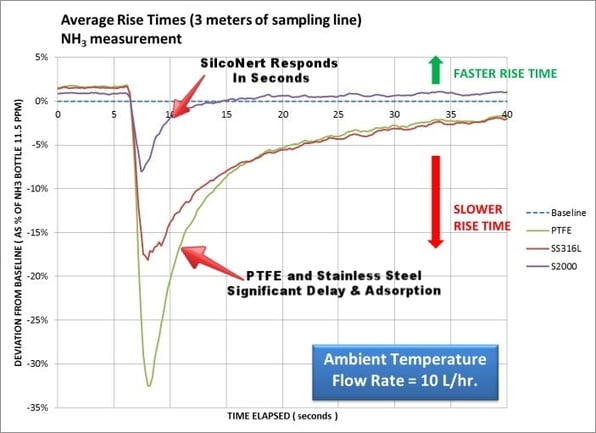
In fact, test errors can be significant; initial NH3 signal rise time results show major differences:
- 32% less response with a PTFE tubing flow path
- 18% less with a stainless steel flow path
- 8% less with SilcoNert-treated flow path
Why Response Error Matters
Fast response means less chance of a cumulative build-up of reactive compounds in the system and fewer test errors. The key to fast response? A surface that does not retain or adsorb the analyte. The graph above shows SilcoNert® does not adsorb the NH3 analyte, so there’s little resulting desorption and disruption to analytical results. SilcoNert’s response time to baseline is the shortest of the 3 surfaces compared:
- Stainless steel: 33 seconds
- PTFE: 18 seconds
- SilcoNert 2000-coated stainless steel: 9 seconds
- Baseline: 6 seconds
Coat the Flow Path
What’s the fix for ammonia and mercury test problems? SilcoNert®-coat the entire flow path. A short piece of tubing may not seem like a test killer, but the results prove that seemingly little things like an inert surface in the flow path can make the difference between garbage results and consistent, robust results. Other components you should coat are:
- Fritted filters: Each frit has a relatively huge surface area. Not coating frits will lead to performance issues related to high sample adsorption.
- Regulators: Although less surface area than frits, regulators too can retain NH3 and Hg, distorting calibration gas integrity and leading to calibration errors.
- Valves and fittings: As detection limits move from part-per-million to part-per-billion sensitivity, even small fittings and valves can retain sample compounds and distort results.
- Sample cylinders: Internal surfaces of sample cylinders are quite rough, creating ideal conditions for unwanted adsorption of ammonia and mercury.
Using Inert Coatings in High Temperature Stack Applications
Customers using our oxidation resistant, corrosion resistant, and inert coatings in high temperature stack, flare, and process applications (over 450° C) often ask if the coatings can “take the heat.” Our answer tends to be a bit long winded, but the short answer is yes; our SilcoNert® 1000 and Silcolloy® coatings are able to withstand temperatures over 1000° C, but there’s a condition.
The long answer is: SilcoNert 1000 and Silcolloy can take the heat over 1000 °C and more, but if you’re heating over 450 °C, you’ll need to preheat the part up to or over the maximum temperature in an inert atmosphere to assure the coating integrity. Why such a long answer? It’s a little complicated, but it all revolves around a phenomenon called carbide precipitation.
Stainless Steel’s Achilles Heel
Stainless steel is a wonderful metal. It’s corrosion resistant, easy to machine and can be made in vast quantities relatively inexpensively. There are issues with stainless steel, however - particularly 300-grade stainless steel.
What does Grain Boundary Corrosion have to do with Coating Integrity?
When heated above 500 °C, carbon in the metal grain boundaries of stainless steel will migrate (precipitate) out of the metal to the surface. The overall result is increased susceptibility to corrosion, known as heat sensitization.*
To assure a stable high temperature coating, follow these 3 steps:
- Consult recommended metallurgy guidelines for your alloy.
- Preheat part to the target temperature per the guidelines (approximately 10 hours should do the trick).
- Heat in an inert environment to prevent oxidation of the surface.
Oxidation Resistant Coating Benefits
Silcolloy®, a high temperature silicon coating, improves oxidation and corrosion resistance of stainless steel by preventing oxygen from interacting with the stainless steel surface, increasing oxidation resistance by orders of magnitude. The comparative oxidation rate of stainless steel vs. Silcolloy shows that the stainless surface oxidizes at a much faster rate than the coated surface.
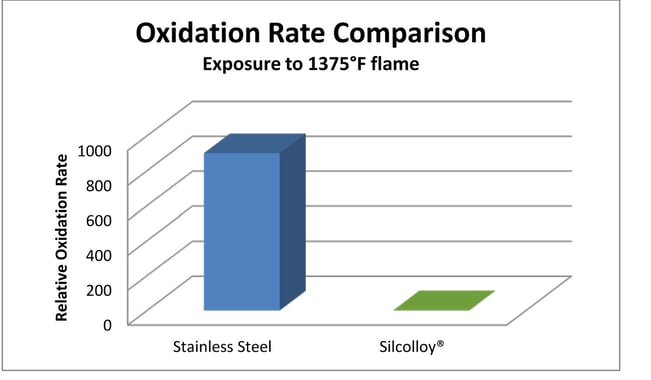
Silcolloy® will maintain a lustrous surface finish even under the most demanding conditions.
- Extend the life of components exposed to high temperatures
- Eliminate contamination from corrosion/oxide formation
- Maintain critical tolerances under high heat conditions
- High temperature coating maintains surface finish, even when exposed to >1000 °C in air
- Eliminate time consuming cleaning/oxide removal
SilcoTek’s high temperature coatings are used in a diverse range of industries and applications:
- Stack and flare sampling
- Fuel delivery and fuel nozzles
- Fluidized bed reactors
- Downhole sampling
- Refining
- Reactors and research
What about Corrosion? How to Prevent & Remove Rust from Analytical Flow Paths
Stainless steel is typically specified because of its ability to resist corrosion in a variety of environments. Unfortunately, stainless steel is not fully stain or rust proof; it’s just more resistant to corrosion than lower grade steels. Anyone who operates a refinery or offshore facility knows all too well that exposure to high salinity environments such as sea water or exposure to other chlorides such as HCl can remove the stainless steel’s native protective layer (chromium oxide) and allow oxidation/corrosion to occur at the substrate. Silcolloy® and Dursan® coatings are both applied to improve the corrosion resistance of stainless steel and other alloys.
Preventing Rust
If you’re sampling in a corrosive or reactive environment, it makes sense to avoid sample contamination and damage to the sample pathway by coating wetted surfaces with an inert, corrosion resistant barrier coating. SilcoTek’s Dursan coating helps to avoid product contamination and extends the life of process equipment and sample flow paths.
Table I provides the results obtained from ASTM G31 testing. This method is an immersion test for 24 hours in a 6M hydrochloric acid (HCl) (18%) solution at room temperature and pressure. After immersion, differential weighing allows the amount of material loss to be determined. The Dursan-coated surface significantly improves chloride corrosion resistance.
Table I: Weight loss after 24 hour exposure to 6M (18%) HCl
24hr; 6M HCl; 22ºC |
304 SS |
Silicon Coated |
Dursan Coated |
MPY (mils-per-year) |
389.36 |
16.31 |
1.86 |
Improvement Factor |
--- |
23.9 |
209.8 |
Comparing multiple coupon materials, Dursan®-coated 316L stainless steel demonstrates similar performance to super alloys.
Superior Salt Spray Performance
Salt spray exposure tests show Dursan significantly improves salt corrosion resistance, extending the useful life of 300-series stainless steel from weeks to years.
Already got rust? Learn how to get rid of it.
So what is the most effective way to remove surface rust from stainless steel? The best method will effectively remove surface rust, but minimize impact to the bulk stainless steel substrate. Two methods used by SilcoTek® to remove surface rust employ weak acids.
Phosphoric Acid
Soaking a part in phosphoric acid will dissolve iron oxide without attacking the other components of the steel (chromium and chromium oxide, nickel, and iron).
Acetic Acid
The reaction with acetic acid is often slower than phosphoric acid and can be a better choice when the underlying corrosion/ staining affects a larger percentage of the substrate.
Read the entire guide on How to Remove Rust
After rust is removed from the surface, coat the parts with a corrosion resistant coating like Dursan® or Silcolloy® to prevent future flow path corrosion
Once Rust is Gone, Keep it Off.
Once the rust is gone, use rugged silicon-based coatings from SilcoTek to improve the corrosion resistance of stainless steel and other alloys. Read more about corrosion resistant coating solutions and how they can benefit you.
Process analyzers and process sampling systems can be exposed to challenging corrosive environments both internally and externally. Many sample streams contain reactive compounds that reduce equipment lifetime or require extended preventative maintenance. Some systems are exposed to environments such as sea water and salt spray, which cause rapid deterioration of equipment, requiring extra cost to keep them operating. Or, the sample stream itself can be highly corrosive like those found in stack or flare systems. For systems that are required to give accurate, reliable and repeatable data in such conditions, the cost of upkeep and maintenance can be excessive in both dollars and lost yield or productivity due to plant or system outages. That’s why it’s important to find ways to improve the corrosion resistance of components rather than just constantly removing rust from surfaces, or worse - paying for frequent replacements.
Conclusion
SilcoTek’s silicon coatings applied by chemical vapor deposition (CVD) improve the inertness, corrosion resistance and durability of sample flow paths. Improving flow path performance can have a significant impact on quality of results and profitability. Here are a few examples:
- Go with a hydrophobic, water repelling surface to prevent corrosion and adsorption of analytes.
- Use inert coatings to act as a barrier between reactive stainless steel and the sample. An inert, silicon surface like SilcoNert® or Dursan® will not adsorb or react with sulfur samples.
- Line sample flow paths with these silicon coatings to also prevent loss of mercury and ammonia samples.
- Silicon coatings bonded to stainless steel flow paths prevent corrosion, reactivity, & oxidation in high temperature process, stack and flare sampling applications.
- Prevent flow path rust if you want to improve reliability of the sample data and system itself. Inert coatings from can be a cost effective solution in many industries and applications including analytical/laboratory instrumentation and sampling, oil and gas upstream and downstream sampling, refinery/petrochemical, semiconductor and research, amongst many more.
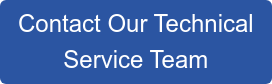