Rouging is a term used in biopharmaceutical manufacturing related applications to describe corrosive attack on flow path surfaces exposed to corrosive streams in water or water based systems. Rouging can be caused by several factors including: the flow path environmental conditions, material quality, fluid pH, duration and frequency of exposure, and the temperature range of the exposed flow path surface.
Rouging can be found in a variety of water systems or water containing systems including pure water, ultra-pure water, steam, treated potable water or untreated process water systems.
What Causes Rouging
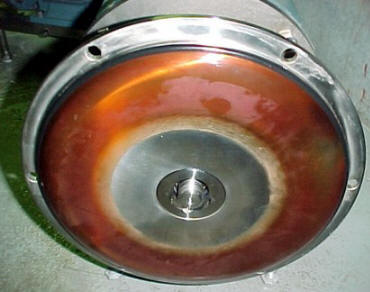
* Stainless steel that has experienced rouging due to corrosive cleaning agents
For the purposes of this blog post, we'll discuss the causes of rouging that relate to stainless steel surfaces. With that in mind we'll review some of the causes of rouging in biopharma, high purity water, WFI, and other systems that require high purity and high corrosion resistance.
Rouging can be caused by a range of conditions and materials in treated and untreated water systems or water-based systems including:
Material, equipment, and installation related causes
- The quality of the stainless steel, and the number of non-metallic inclusions in the stainless steel.
- Particulate contamination resulting from system assembly, grinding, welding or cutting particles.
- Metallic defects resulting from improper welding or heating.
- Iron contamination resulting from steel to stainless steel contact.
- Erosion or pump cavitation of stainless steel impellers or high velocity flow paths that result in stainless particulate generation which oxidizes and forms rouge.
Water/process fluid conditions
- For WFI and high purity, and process water systems or water based fluids, the oxygen content and pH of the water can result in corrosive attack and pitting.
- The pH level in WFI high purity water systems can have an effect on metal ions like ferrous and ferric ions found in stainless steel. Ferrous ion leaching can cause the red or black staining found in rouging.
- Metal Ion leaching resulting from deionized or high purity reverse osmosis water can result in surface pitting and rouging effects. Especially heated water which can erode the surface passivation due to less dissolved oxygen. High temperature will also increase iron diffusion rates which can then react with the oxygen in the water to cause iron oxides and hydroxides.
- Chlorine or dissolved oxygen in the process fluid causing oxidation of ferrous bicarbonate resulting in red/brown deposits in untreated water or process water systems.
- Exposure to high temperature, high purity, steam can result in a black surface. In electropolished systems the surface may appear glossy black. For mechanically polished finishes a flat black surface may result.
Cleaning and denaturing agents
- Cleaning agents and protein denaturing agents like guanidine hydrochloride can pit and corrode stainless steel flow paths, resulting in rouging.
- Contamination or corrosion resulting from aggressive cleaning agents or improper cleaning methods.
Impact of Rouging on High Purity Components
Rouging can contaminate high purity systems which can adulterate products, cause yield problems, increase maintenance, may result in lost product, and can reduce efficiency. Cleaning or restoring the surface to original condition can be time consuming and costly and involves a combination of one or all of the following:
- Acid cleaning, neutralizing and flushing the system.
- Disassembly and re-polishing or electropolishing components or flow paths.
- Mechanical cleaning of the surface.
- Employing chelating agents to remove iron
- Sanitizing or conditioning the surface to approved specifications.
- Testing the system to assure operation and quality is within specifications.
The remediation process for removing rouge and rouging effects may not be realistic for some high purity applications. For some systems, component replacement may be the only option. Because remediation or replacement are costly options, it's worth considering employing methods to prevent rouging from happening in the first place.
Solving Rouging on Stainless Steel BPE Components with CVD Surface Treatments
Electropolished and passivated alloys are not enough to prevent rouging while exotic alloys carry long lead times and prohibitive costs. Even the smoothest stainless steel or exotic alloys are prone to microscale reactions with process fluids that lead to expensive downtime, lower efficiency, and maintenance.
Fluid contact with metal surfaces should be eliminated to maximize output, performance, and purity, but metal alloys are a must-have for BPE. How can end users and manufacturers of bioprocess systems achieve both?
Surface technology from SilcoTek that makes stainless steel:
- Corrosion and rouge resistant to fluids at any pH 0-14
- Twice as durable
- Self-cleaning and easier to maintain
- Inert to the most coveted metal-sensitive compounds of interest, like oligonucleotides
SilcoTek’s surface technology is trusted by manufacturers of semiconductors, medical devices, analytical instruments, and other high technology applications where purity and performance are of utmost importance. Reasons include:
- Surface treatment is FDA compliant, USP Class VI and NSF certified
- Applicable to any BPE flow path component, including tubes up to 24’ long
- Penetrates and bonds to equipment surfaces molecularly, preventing flaking
- Does not change ASME-BPE surface designation, can be applied to SF0-SF6
- Vapor phase surface treatment process uniformly treats 100% of surfaces
- Significantly lower cost and lead time than exotic alloys
- Easy process – send SilcoTek® your equipment and we handle the rest
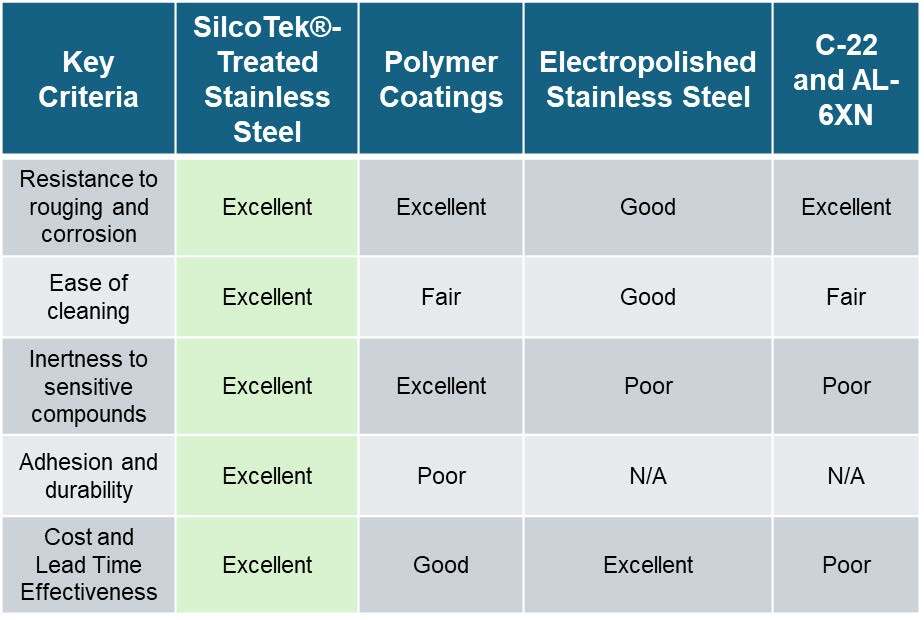
SilcoTek®-treated 316L stainless steel eliminates rouging in guanidine hydrochloride (left) and even prevents metal contaminants that leach from C-22 in the presence of high purity water (right).
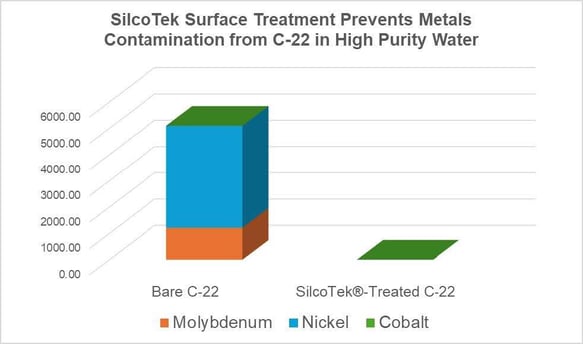
Surface Treatment Technology from SilcoTek Improves Purity, Efficiency, and Output of Bioprocessing
SilcoTek can coat your new or existing BPE components to improve performance at a fraction of the cost and lead time of exotic alloys. SilcoTek’s coatings and surface treatments are written into specifications for the world’s largest companies in semiconductor and pharmaceutical manufacturing where purity is paramount. Contact our experts to discuss your application and receive a free trial coating on your own parts to see the performance for yourself, no strings attached.
Have questions about SilcoTek coatings? Reach out to our team!
*Image Credit: Corrosion Doctors.org https://corrosion-doctors.org/MatSelect/rouging.htm