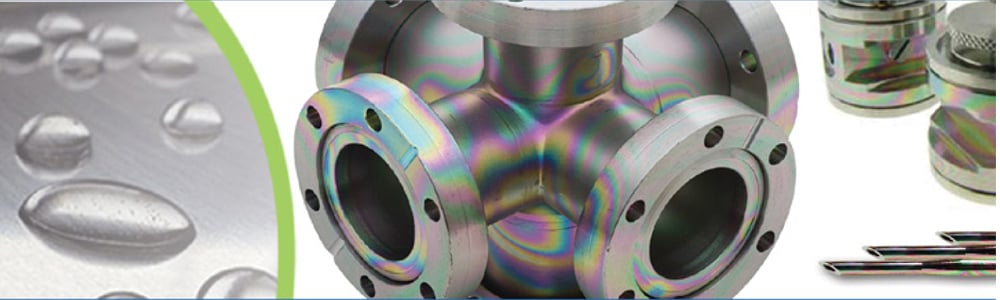
Covid, war, and a host of other disruptions have severely constrained material supply. What about SilcoTek? Are supply disruptions affecting coating lead times? Nope.
Are Supply Chain Disruptions Affecting SilcoTek Lead Times?
The short answer is no. But let's go into some details about SilcoTek® lead times and why others may be quoting long lead times for coated parts.
In this blog post you will learn:
- How recent world wide supply chain disruptions have not impacted SilcoTek® shipping performance.
- Learn about our coating process and how we quote lead times for coating your parts.
- How to minimize coating lead time for your parts.
|
Supply Chain Disruptions
SilcoTek® has not experienced significant supply chain disruptions due to the pandemic or shipping bottlenecks. Some suppliers may depend on international supply chains but our process does not depend on international supply chain logistics. Manufacturers of stainless steel products and coatings may have been severely impacted by several recent events including:
- Tariffs
- Pandemic related work stoppages.
- Supply disruptions due to shipping bottlenecks.
- Supply disruptions due to the war in Ukraine.
- Vendor reliability issues.

Why has SilcoTek been largely unaffected by supply chain issues? Because the SilcoTek coating facility and suppliers are located domestically. Additionally, our facility has been designated as a critical manufacturing operation and consequently has remained open throughout the pandemic.
Our raw materials are also domestically supplied and although not immune to supply disruptions, our process and raw material supply have not been impacted by recent events. Consequently, our lead times have not changed significantly throughout the pandemic.
Why ship parts to SilcoTek in the first place? CVD coatings are not sprayed on. They require reactors and sophisticated process monitoring to assure a quality coating. That's why we ask customers to ship their parts to us. Learn more about our CVD coating process get our introduction to coatings e-book.
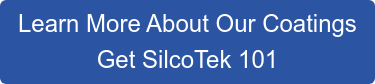
We know that shipping parts to us can lead to supply chain problems. That's why we try our best to coat parts and ship them back to you as soon as possible. (within 10 working days or less for most standard processes and products). We also offer other supply chain support to make doing business with SilcoTek easier:
- Simplified shipping guidelines to assist folks when sending parts to us.
- Dedicated international logistics representative to help with overseas shipping and customs.
- Place and coordinate orders through one of our local sales representatives.
- Kanban and other supply chain support.
- Work with your automated supply chain systems.
Our Process and How We Quote Coating Lead Time
Our coatings are applied by chemical vapor deposition at our Bellefonte Pennsylvania facility. The CVD process involves several critical steps that, in order to assure a quality coating, must be completed at our facility. The coating process generally involves the following steps.
- Part receipt
- Inspection
- Surface preparation
- Coating application
- Final inspection
- Ship completed order to the customer
The Process
Once received, your parts are inspected to ensure we received everything you intended to send. If there are any questions or "red flags" before coating, our Customer Service Representative will contact you to review your order and any potential concerns with processing. Substrates listed on our material compatibility chart as "not treatable" will either be returned directly to you or along with your compatible parts after coating. Once everything is confirmed, our customer service team will send you an order acknowledgment email.
SilcoTek® takes special care to collaborate with all our customers and provide exceptional service that exceeds your expectations. Our manufacturing process is designed to expedite every order that we process. By employing FIFO (first in, first out) and One-Piece-Flow methods for moving parts through the production process, we can maximize both speed and efficiency as well as minimize potential handling damage or errors.
After a thorough surface preparation, our technicians load customer parts into a vacuum vessel corresponding to the size of the parts. This vessel is placed in a large oven and connected to the raw material - gas - then heats to temperatures near 400° C. Throughout this process, a proprietary blend of gas enters the vessel and starts a reaction which diffuses the treatment into the molecular lattice of the substrate, forming the ultra-thin SilcoTek coating that so many have come to recognize and trust.
Learn more about our coatings and their applications.

What Process Impacts Lead Time
Coating lead times will vary depending on the degree of customization needed for the part. Parts that are coated using our standard process and those that are frequently coated will generally have a shorter lead time than parts requiring a customized coating or special processing. Coating lead times vary from days to weeks depending on the degree of customization required.
How to Minimize Coating Lead Time
We offer consistent and industry leading coating services for our customers but there are a few hacks that can help to speed up the coating process.
Talk to us first.
Contact us, tell us about your parts and get a quote and shipping instructions from us before sending your parts in to SilcoTek for coating. That will avoid confusion and processing delays while we contact you and quote you for coating service. Also talk to us about your performance needs and we'll suggest the best coating for the application. You can also use our coating selector guide to help you select the best coating for your application.
Pack your parts safely.
Nobody wants damaged parts. Be sure to follow best packaging practices when packing your parts for shipment to our facility. If parts are damaged in shipping we'll contact you to discuss the best options moving forward, but that can take time. Read more about packaging tips in our blog.
Disassemble parts before shipping to SilcoTek.
We ask customers to disassemble parts before shipping. If we have to disassemble parts we'll contact you. This can take time. We may also not be able to disassemble parts, especially complex assemblies. Working out disassembly issues can add time to the coating process and may result in returning parts to you for disassembly.
Tell us about any surface exposure or special handling needs.
Tell us if parts have been exposed to chemicals or grease or other environmental exposure. Chemical exposure can affect the surface preparation and coating process. And may result in poor coating quality which will require time consuming rework.
Where possible go with standard coatings and standard processing.
We can customize coatings to best suit your application but a custom coating may take more time to process. If possible stick with standard coatings and standard coating processes. That's usually the most cost effective and fastest process.
Want to learn how fast we can coat your parts? Get a coating quote.
If you're buying coated parts from an OEM supplier and get long lead times, it may be their supply chain issues. But at SilcoTek®, we're striving to excel at industry leading service and delivery, without the supply chain headaches.
To learn more about how our coatings can improve your products and process, subscribe to our blog, or follow us on LinkedIn.
