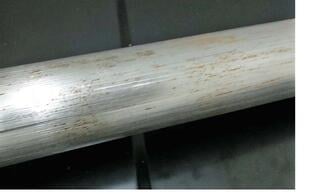
Despite the name, stainless steel can stain and rust. We review the best ways to remove rust from stainless steel in industrial applications.
How to Remove Rust, Corrosion on Stainless Steel
Stainless steel is typically specified because of its ability to resist corrosion in a variety of environments. Unfortunately, stainless steel is not fully stain- or rust-proof, it is just more resistant to corrosion. Exposure to high salinity environments such as sea water can remove the native protective layer (chromium oxide) and allow oxidation/corrosion to occur at the substrate.
In This Blog Post You Will Learn:
- How to remove rust from stainless steel for industrial applications including:
- Refining and petrochemical
- Semiconductor
- Analytical and laboratory testing
- Industrial processes
- How our industrial coating technology can improve stainless steel corrosion resistance.
|
Have a question about this blog or corrosion resistance? Click the box below to discuss your application with one of our coating scientists.
Have a Question? Contact Our Technical Service Team
So what is the most effective way to remove surface rust from stainless steel?
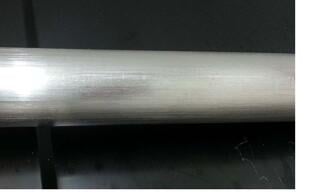
The best method will effectively remove surface rust, but minimize impact to the bulk stainless steel substrate. Two methods used by SilcoTek® to remove surface rust employ weak acids that will remove rust but will not damage the base metal. Here are the rust removal chemicals we use.
Phosphoric Acid
Phosphoric acid will dissolve iron oxide without attacking the other components of the steel (chromium and chromium oxide, nickel, and iron). The rust is dissolved by the following reaction: 2 𝐻3𝑃𝑂4 + 𝐹𝑒2𝑂3 → 2 𝐹𝑒𝑃𝑂4 + 3𝐻2𝑂
Phosphoric acid is readily available from a number of commercial suppliers (SilcoTek uses 85% ‘food grade’) and it can be used with no dilution because of its non-aggressive nature. Clean up after acid treatment is done by thoroughly rinsing parts in deionized water to remove any remaining acid on the surface. If deionized water is not available, rinse with distilled water.
Unfortunately, this technique is not 100% effective on all the forms of iron oxide and other surface preparation treatments could be necessary.
Acetic Acid
The reaction with acetic acid is often slower than phosphoric acid and can be a better choice when the underlying corrosion/staining affects a larger percentage of the substrate. We detail our rust removal process in detail in our rust removal report. Click on the link below to get the report.
Read the Entire Rust Removal Report.
Following the acid exposure, parts must be rinsed thoroughly with deionized water to assure complete removal of trace acid.
Watch our sonication video to see how to sonication removes particulates.
Improving Corrosion Resistance
Silcolloy® and Dursan® coatings can be applied to stainless steel components to improve the corrosion resistance of stainless steel and other alloys. The comparative graph below highlights the improved corrosion resistance of Silcolloy and Dursan coated surfaces. The coated samples were immersed in 6% hydrochloric acid for 24 hours. The results show a significant reduction in corrosion rate when parts are coated with Silcolloy or Dursan silicon coatings. Corrosion performance is comparable to Hastelloy®.
Read more about corrosion solutions.
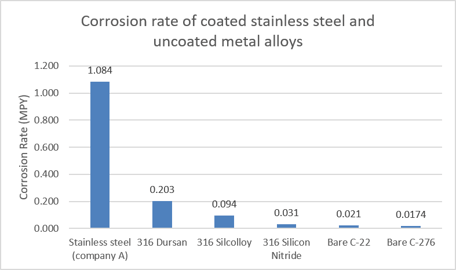
How do SilcoTek coatings perform in other corrosive applications? Under various severe corrosion exposure conditions shown below SilcoTek coatings improve the corrosion resistance of 316L stainless steel by 2-50x when compared to uncoated stainless steel.
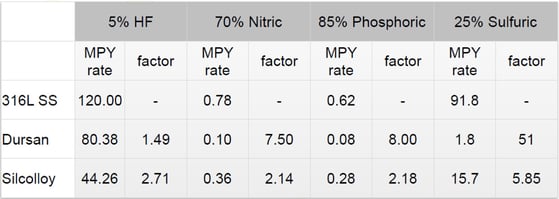
Note that the effectiveness of the coating as a barrier to corrosion can be compromised if the substrate surface has pre-existing rust or corrosion spots/stains.
Conclusion:
The best substrate to coat is one that is clean and does not show rust. If there is a potential for free iron on your part’s surface, SilcoTek recommends addressing it prior to shipping to us.
If it is not possible to apply the removal techniques in-house, SilcoTek’s sales group can provide a quote for the acid cleaning process upon request.
Click here to get a coating or cleaning quote.