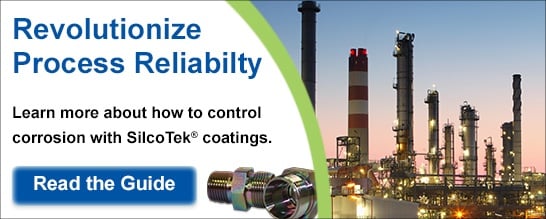
We tested our coatings in a wide range of corrosive environments to see just how effective they are in protecting stainless steel from corrosion and preventing rust on stainless steel. Here's what we learned.
In this blog post you will learn;
- How traditional stainless steel passivation techniques are not effective in preventing corrosion.
- Ways to protect stainless steel from rust with a corrosion resistant barrier coating.
- Review corrosion data for various corrosives including:
- HF
- Nitric Acid
- Phosphoric Acid
- Sulfuric Acid
- Hydrochloric Acid
- Hydrogen Sulfide (H2S)
- Get links to more in-depth corrosion data
|
Corrosion can not only compromise analytical system integrity and increase maintenance cost; it can also generate particulates that can result in obstruction and fouling of the system and cause adsorption of reactive compounds. Pitting can also create excellent hiding places for “sticky” molecules, resulting in carryover and false positive results. Passivation and polymeric coatings have been utilized to reduce corrosive attack, but there’s a higher performing alternative that improves both inertness and corrosion resistance of the surface. But first let's talk about passivation and why it's not an ideal corrosion prevention technique in analytical flow paths.
About Passivation
Nitric acid passivation is commonly used in an effort to remove exogenous iron from surfaces and add an oxide layer in the
hope that the stainless steel flow path will become more corrosion resistant or inert.
Traditional passivation techniques involve the following steps:
• Thorough cleaning of surfaces
• Immersion in nitric or citric acid bath for 30 minutes. (acid concentration and additives are dependent on the grade of
stainless steel)
• Rinse parts thoroughly in water
• Test part for passivation by placing in a humidity cabinet.
Unfortunately, when applications require the use of aggressive agents like bleach, sulfuric, or hydrochloric acid, no amount of
passivation or electropolishing will prevent corrosive attack. That's because highly corrosive agents react with the stainless steel protective oxide layer, causing pitting and corrosion of the surface.
Read more on how to effectively prevent corrosive attack.
Get Our Corrosion Webinar Summary Presentation
An Alternative to Passivation
There's an alternative to passivation that produces better results: change the surface properties of the material by bonding enhanced silicon compounds onto the steel surface via chemical vapor deposition (CVD). A CVD coating like Dursan®, for example, will improve the corrosion resistance and inertness of the surface, offering a multitude of benefits. The chemical vapor deposition process used to coat stainless steel flow paths will prevent disruption of grain boundaries and act as an inert barrier to aggressive and sticky compounds. Dursan coated analytical flow paths will prevent HCl, sulfuric acid, bleach, and other corrosives from pitting and attacking stainless steel surfaces. Here are some examples of how Dursan and Silcolloy® can improve corrosion resistance.
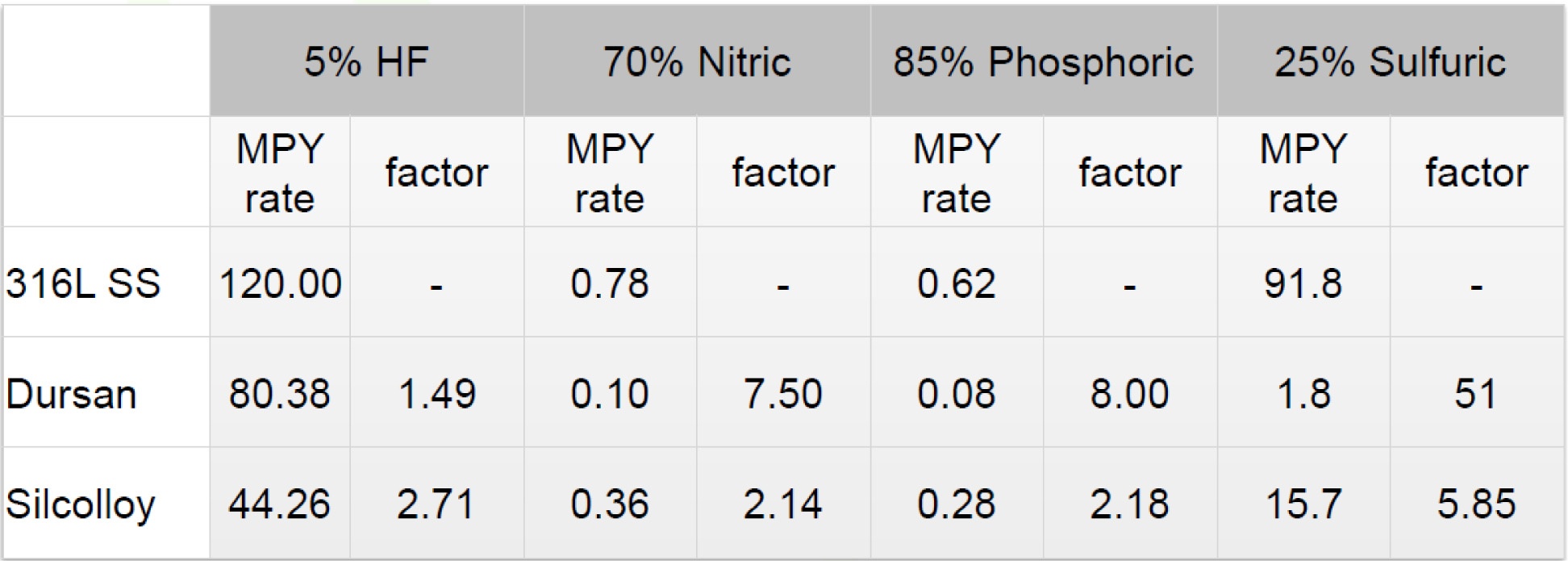
Click here to learn more about improving the corrosion resistance and durability of analytical systems.
Dursan offers inertness, durability, fouling, and carryover contamination benefits for process analytical, medical diagnostics and HPLC applications. Want to learn how our coatings benefit HPLC analysis? Sign up for our new HPLC Webinar.

Dursan Corrosion Resistance Data. How a CVD Coating Can Protect Stainless Steel From Rust.
Dursan® can increase corrosion resistance by 10x or more through preventing interaction of the analyte or process fluid and the stainless steel surface. Dursan exceeds typical metal passivation capability. Immersion testing in 6M hydrochloric acid (HCl) shows that Dursan coated surfaces prevent surface attack and protect stainless steel from rust by orders of magnitude compared to passivated stainless steel.
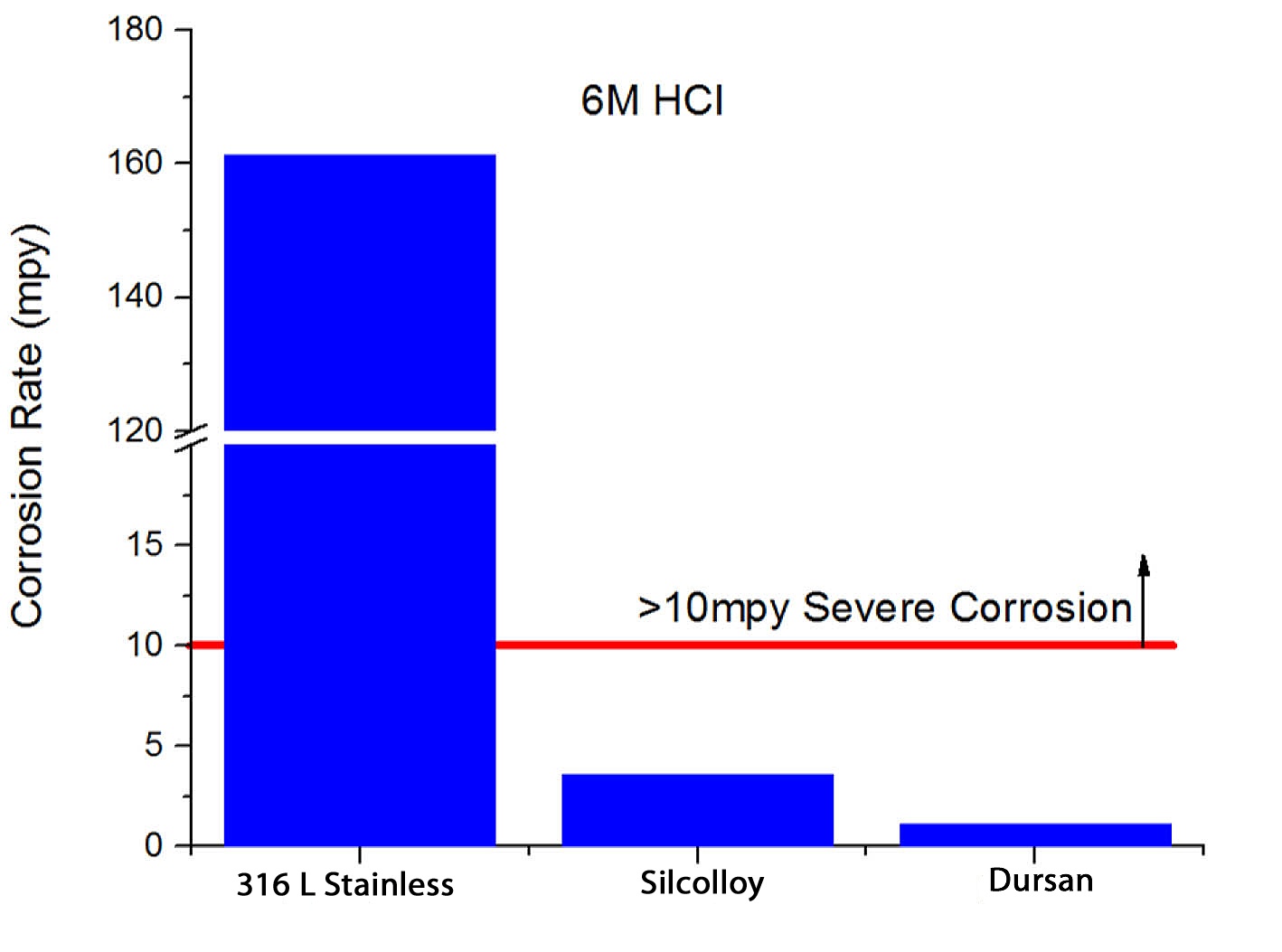
Sulfuric acid can form in process analytical sampling systems and stack sampling systems that transport stack emissions or hydrocarbon flare samples. When exposed to water and heat, sulfur compounds commonly found in stack samples can form sulfuric acid and corrode and contaminate sample systems. Inert coatings like Dursan reduce the risk of corrosion, even when exposed to sulfuric acid.
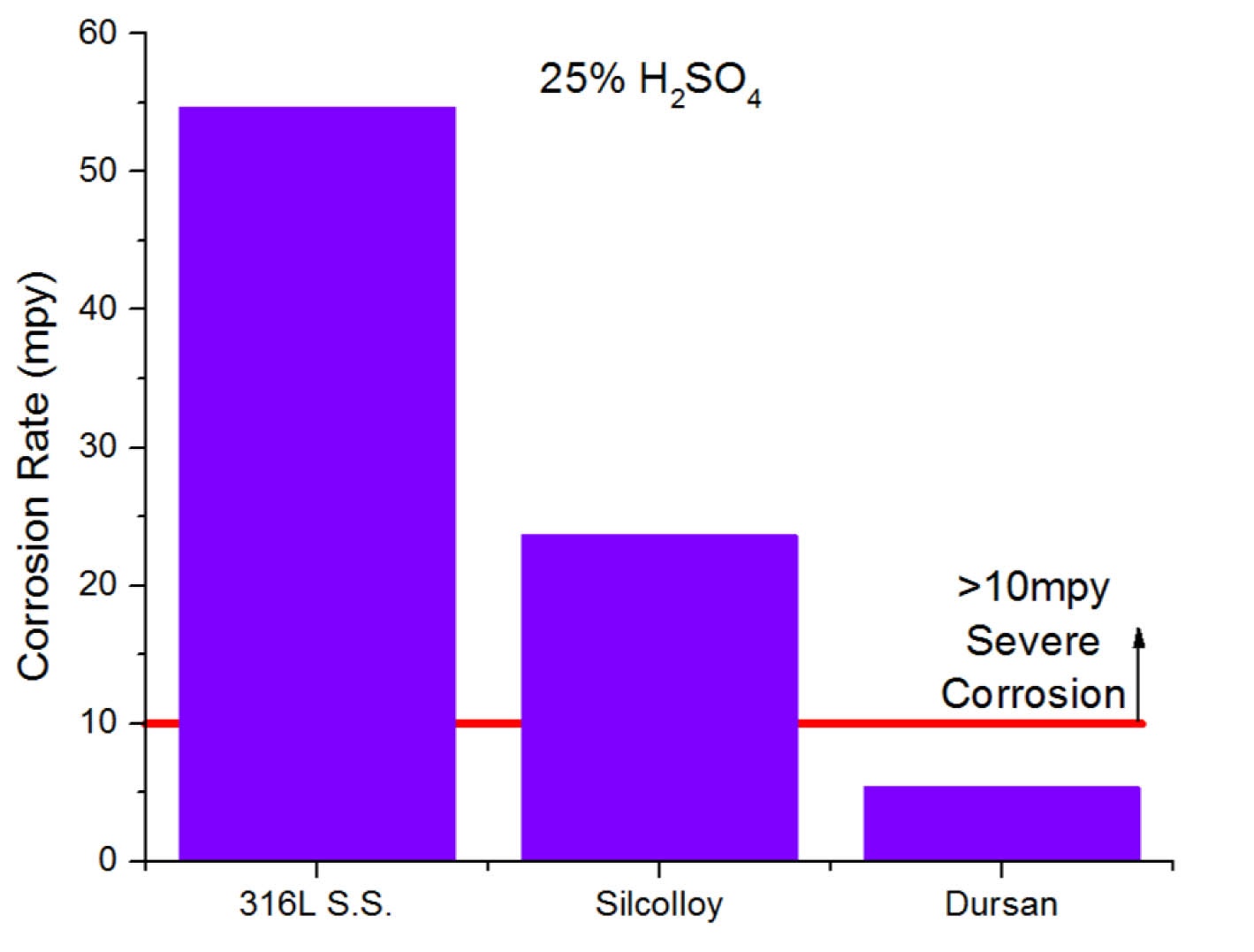
H2S corrosion resistance
Immersion in H2S saturated acidic brine solution for 30 days per NACE TM0177 shows that the Dursan coated coupons improve corrosion resistance but do show some pitting on the surface. Note that any coating does not meet NACE MRO175 standard for H2S exposure. MRO175 applies to the base metal exposure only. Dursan, however, can improve H2S inertness and sample flow path durability in conjunction with MRO175 compliant materials.
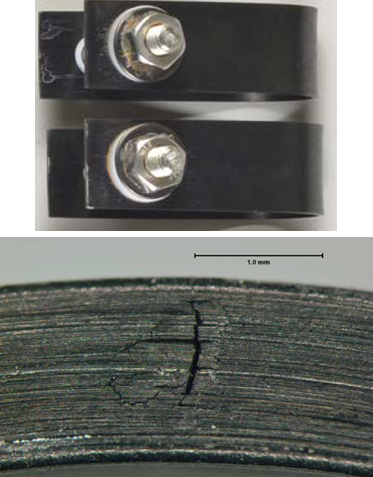
Uncoated test coupons show cracking and corrosion after H2S exposure.
|
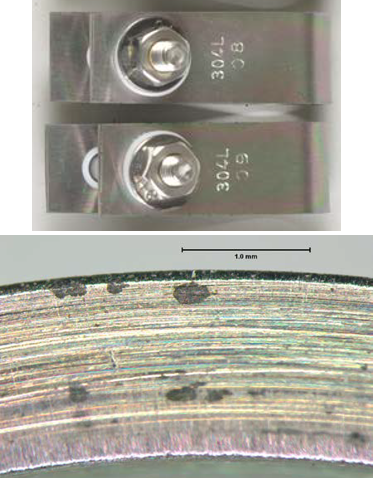
Dursan coated coupons show minor pitting after H2S exposure.
|
Get more corrosion application information and benefits for your process or products. Get our corrosion presentation.
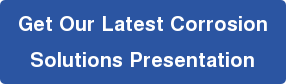
Protecting analytical flow paths from rust can revolutionize the reliability of process and analytical sampling. Contact our technical service team to discuss your application. Need an inert hydrophobic surface? How about an anti-fouling surface that's wear resistant? Our team can help match the best coating for your application.