If you are performing an analysis using a sampling system, there can be many roadblocks in the way of obtaining accurate and reliable results. One of the most frustrating of these is adsorption, which can lead to a host of other problems down the road. Our coating, SilcoNert® 2000, creates an inert barrier for your flow path to prevent adsorption of compounds like water, carbon monoxide (CO), hydrogen sulfide (H2S), ammonia (NH3), methane (CH4), hydrochloric acid (HCl), nitrogen dioxide (NO2), formaldehyde (CH2O), and others.
CVD Coating Improves Reliability of Hydrogen Fuel Cell Analysis
Let's look at hydrogen fuel cells as an example. The way that hydrogen cells produce electricity is by combining hydrogen and oxygen atoms. According to a 2017 article by American History, "in general terms, hydrogen atoms enter a fuel cell at the anode where a chemical reaction strips them of their electrons. The hydrogen atoms are now "ionized," and carry a positive electrical charge. The negatively charged electrons provide the current through wires to do work. If alternating current (AC) is needed, the DC output of the fuel cell must be routed through a conversion device called an inverter." Then, the hydrogen reacts with the oxygen through an electrochemical cell at the electrodes. The products of this reaction are electricity, water and a little heat. Depending on the size of your cell, you can generate enough power to run a laptop or an electric power grid.
A passivated surface will reduce surface reactivity and adsorption. This improves test accuracy and overall test reliability, but what are the consequences of an inaccurate test? Contaminated fuel can damage fuel cells and engines as well as damage catalysts. Not to mention that off-spec fuels can can be a real liability for the supplier. So it's in everyone's best interest to test as accurately as possible.
The Consequences of Inaccurate Hydrogen Fuel Testing in Fuel Cells
- Fuel cell damage due to poisoning
- Reduced fuel cell performance
- Increased maintenance
- Cell failure
Trace level contaminants can have a real effect on overall system performance. A reactive flow path can adsorb many trace contaminants which will lead detection failures. Without precise testing, hydrogen contamination will continue and ultimately lead to system failures. That's why it's important to select flow path materials that prevent adsorption of hydrogen contaminants. Gaseous compounds may adhere to sample line, regulator, filter, etc. Because of this, many equipment materials would not fit this application.
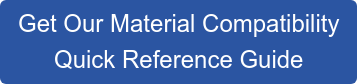
Primary Sources of Hydrogen Contamination and Why it's Important to Keep Them Under Control
The below table highlights contaminants that can affect the performance of hydrogen powered systems, either in the production of hydrogen, the delivery of hydrogen, or in the efficient operation of the power system (internal combustion engines or fuel cell systems).
Some contaminants can reduce the efficiency of hydrogen production or damage catalysts which can result in catalyst poisoning and premature system failure. Contaminants can also damage hydrogen transport systems. For example, water can freeze valves, regulators or filters while particulates can damage or interfere with gaskets and seal areas or clog filters. While other contaminants, like N2, NOx or CO2, may not directly damage the fuel delivery system or damage the fuel cell itself, they can reduce the overall energy density of the fuel. This can result in poor performance in fuel cells or internal combustion engines. An increase in air emissions (NOx, SOx, etc.) may also result from contamination in the fuel stream.
Table 1: Directory of limiting characteristics (maximum allowable limits of contaminants) from ISO FDIS 14687-2. ( "Hydrogen Fuel Quality Specifications for Polymer Electrolyte Fuel Cells in Road Vehicles", US Department of Energy, 2016 )
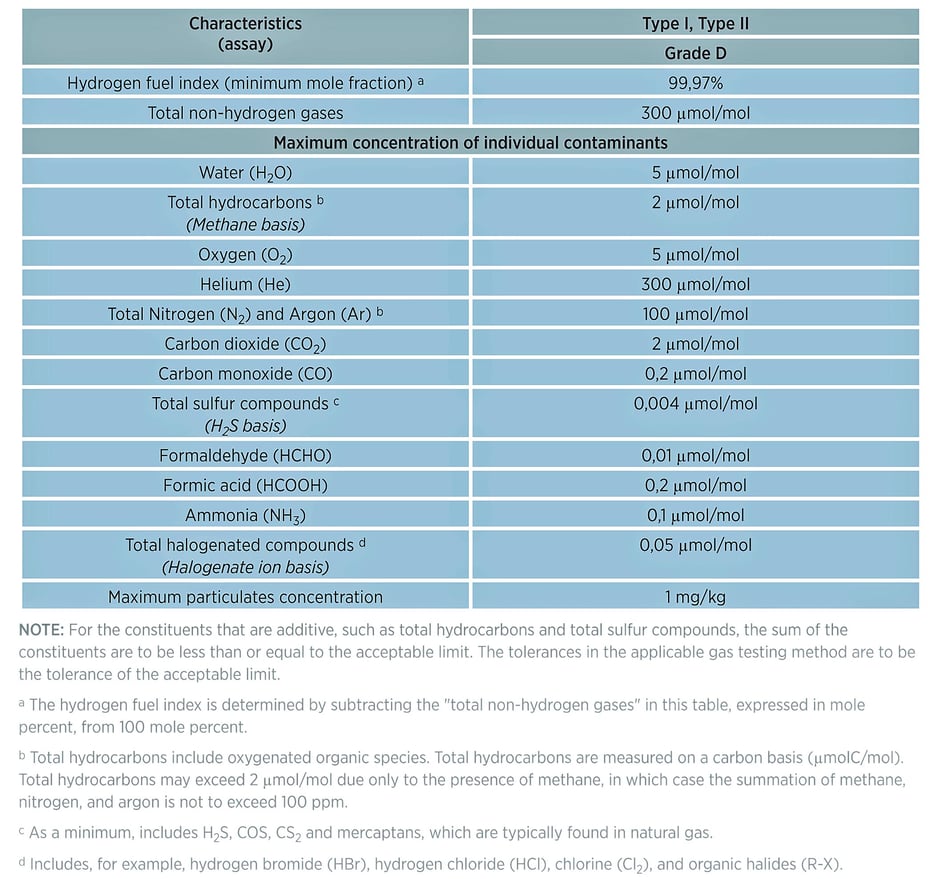
According to a study by the US Department of Energy, the contaminants that pose the greatest danger to the performance of hydrogen production, delivery, and power systems like fuel cells or internal combustion (IC) engines include:
- Carbon monoxide (CO) - CO can absorb onto the fuel cell surface and prevents hydrogen production.
- Sulfur and sulfur species like hydrogen sulfide (H2S) - Sulfurs will contaminate the fuel cell catalyst and hydrogen production catalysts. Even trace sulfur contamination can quickly and irreversibly damage catalysts, causing poor performance and eventual premature catalyst replacement.
- Ammonia (NH3) - Ammonia can can also poison catalysts and impede hydrogen production. Levels of ammonia as low as 2 ppm have been shown to result in degradation of hydrogen production.
- Inert gases like nitrogen (N2) or oxides of nitrogen (NOx), or carbon dioxide (CO2) - inert gases do not damage catalysts or other system flow path components but they will reduce the overall energy density of the gas stream, reducing the performance of the downstream equipment like fuel cells or internal combustion engines using hydrogen as a fuel.
- Methane CH4 - Methane can also dilute the hydrogen gas stream. Methane contamination in production processes can reduce the overall hydrogen production efficiency.
- Water - Water can freeze in process and transport flow paths, inhibiting operation or damaging valves, regulators, orifices, or filters.
- Aromatic hydrocarbons - Aromatic hydrocarbons, like benzene BTEX (the name for benzene, toluene, ethylbenzene, and xylene contaminants) can absorb onto the catalyst surface and block or inhibit hydrocarbon production.
- Fine Particulates (below 10 microns) - particulates can damage flow path seals and blind filters.
The combined effects of contaminants in hydrogen production and use can result in an increase in production cost, impact reliability and performance of catalysts, can increase air emissions, and can potentially lead to safety and reliability issues in transportation systems. All of these negative effects can inhibit the expansion of hydrogen use in the greater economy and limit hydrogen's potential as a contributor to achieving carbon neutrality in energy use and production.
The amount of adsorption/loss will depend on flow velocity, material, flow path configuration (bends, tubing diameter, number of fittings, etc.) and the amount of time the sample is exposed to the surface. Here are some best practices that you can use when testing your sample.
Sampling Best Practices
Before sampling hydrogen, or any substance for that matter, best practices outlined by industry standards should be followed. Best practices include:
- Assure material compatibility with the system, environment, test conditions, and analyte. This includes accounting for system pressure, corrosion resistance, temperature exposure, physical use and damage; as well as analyte adsorption and reactivity.
- Be sure all flow path components are not damaged and perform to specification.
- Flow path surfaces should be cleaned in accordance with industry standards. Cleaning solvents should be tested or certified that no trace contaminants are left on the flow path surface after the cleaning process.
- Flow paths and analytical equipment should be tested with a control sample to assure the system is performing to standard.
To achieve even more accurate and reliable results, SilcoTek recommends coating the entire sample flow path. Just one uncoated fitting can adsorb enough sulfur to significantly alter test results. This can lead to inaccurate results and contamination of fuel cell catalysts.
Here are just some of the components that we recommend coating:
- Tubing
- Fittings
- Valves
- Regulators
- Fritted filters
- Sample Cylinders
Here's an example of how SilcoNert 2000 compared to PTFE, PFA, EP 316L, and SS 316L when analyzing ammonia adsorption.
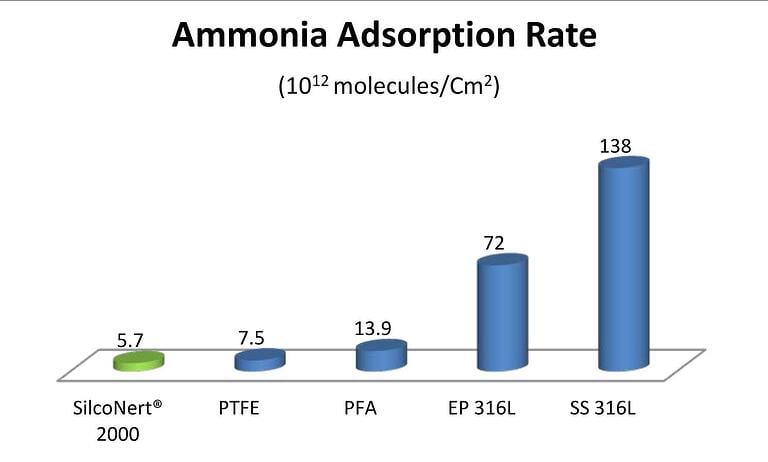
If you want to know more about how our coatings can help your application, we encourage you to reach out to our technical service team to discuss your application.
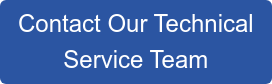
References:
Fuel Cell Basics. A basic overview of fuel cell technology. (2017). Retrieved October 21, 2022, from https://americanhistory.si.edu/fuelcells/basics.htm
Ohi, J. M., Vanderborgh, N., & Voecks Consultants , G. (2016, November 2). Energy Efficiency & Renewable Energy. Energy.gov. Retrieved October 21, 2022, from https://www.energy.gov/sites/prod/files/2016/11/f34/fcto_h2_fuel_quality_specs_pem_fc_road_vehicles.pdf