From November 13-15, SilcoTek's Dr. Jesse Bischof attended the Eastern Analytical Symposium (EAS) at the Crowne Plaza Conference Center in Plainsboro, NJ. At the show, he spoke about Replacing Electropolished Stainless Steel Tubing with a Silicon Based CVD Coating for Higher Inertness, Faster Dry Down Performance, and Greater Corrosion Resistance for Gas and Fluid Transfer. We wanted to share his main points of the talk.
Dr. Jesse Bischof
About EAS
First, the EAS is a prominent annual conference and exhibition dedicated to analytical chemistry and its related fields. It is one of the largest analytical chemistry conferences held in the United States, typically taking place in the northeastern region.
EAS aims to bring together scientists, researchers, academics, industry professionals, and exhibitors to share knowledge, discuss recent developments, and explore advancements in analytical chemistry, instrumentation, and related technologies. The symposium covers a wide range of topics, including but not limited to chromatography, spectroscopy, mass spectrometry, electrochemistry, and other analytical techniques.
During the symposium, attendees had the opportunity to participate in various activities such as keynote presentations, technical sessions, workshops, poster sessions, and exhibitions where companies showcase their latest instruments, equipment, and technologies in the analytical sciences.
EAS provides a platform for networking, collaboration, and learning, offering insights into the latest research, applications, and methodologies in analytical chemistry and related disciplines. This event serves as a valuable resource for professionals and students involved in analytical chemistry and its various applications in industry, academia, and research.
SilcoTek attended to build relationships with industry professionals in need of a solution.
Technical Talk
In his poster presentation, Dr. Bischof discussed replacing electropolished stainless steel tubing with a silicon-based chemical vapor deposition (CVD) coated steel tube for higher inertness, faster dry down performance, and greater corrosion resistance for gas and fluid transfer. During his presentation of the poster, he talked about the differences in adsorption rates when comparing SilcoNert 2000 coated tubing versus electropolished tubing.
Inertness Comparison
The coating created through CVD by SilcoTek creates an inert surface, meaning it's less reactive with the substances it comes into contact with. This reduces the chances of chemical reactions or adsorption, making it ideal for handling sensitive materials or samples without contamination.For this experiment, tubing was filled with 100 psi of nitrogen that contained 20 ppb of hydrogen sulfide (H2S), carbonyl sulfide (COS), and methyl mercaptan (MeSH). It was monitored over 4 days. COS is not a molecule that adsorbs easily and was used as an internal reference. The GC chromatograms are shown below:
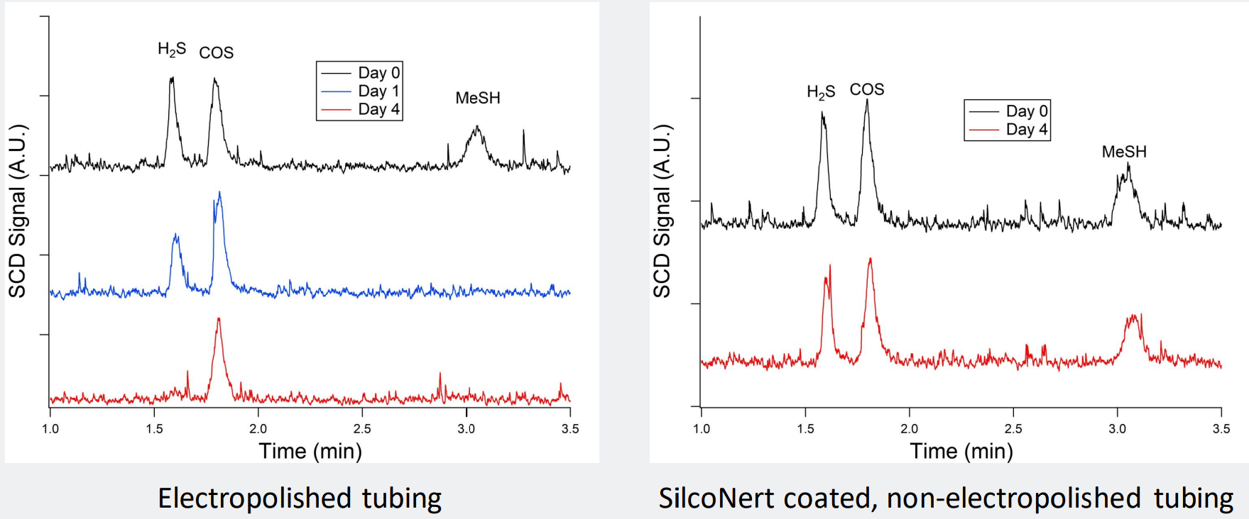
The active compounds, hydrogen sulfide (H2S), carbonyl sulfide (COS), and methyl mercaptan (MeSH), show slow and immediate loss of signal due to adsorption to the surface of the steel, even with electropolishing. Similar results are shown in the full study on non-electropolished tubing. Only the SilcoNert 2000 coating allows the preservation of the active sulfur compounds.
Boost Dry Down Performance
The inert and hydrophobic nature of the coating helps in faster drying of fluids by reducing the adhesion of liquid molecules to the surface. This property can be especially useful in analytical instruments or applications where maintaining sample purity or minimizing carryover is crucial. The electropolishing of the tube shows a minimal impact to dry down times while the application of SilcoNert 2000 to non-electropolished tubes cuts the dry down time nearly in half.
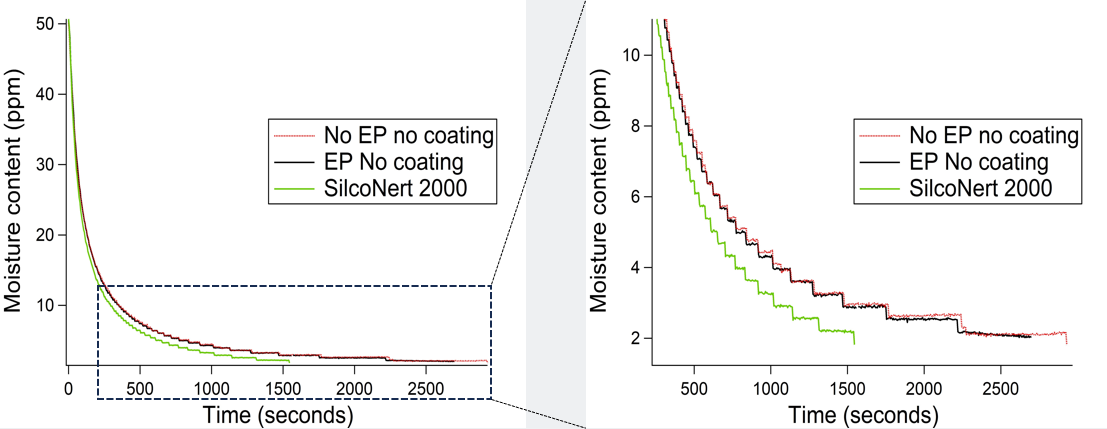
Better Corrosion Resistance
The coating provides excellent corrosion resistance, protecting the underlying material from degradation caused by harsh chemicals, moisture, or corrosive gases. This extends the lifespan of the components and ensures the integrity of the transfer system over time. SilcoNert 2000 provides a good corrosion barrier for 5% HCl, as shown in the chart below each coupon type:
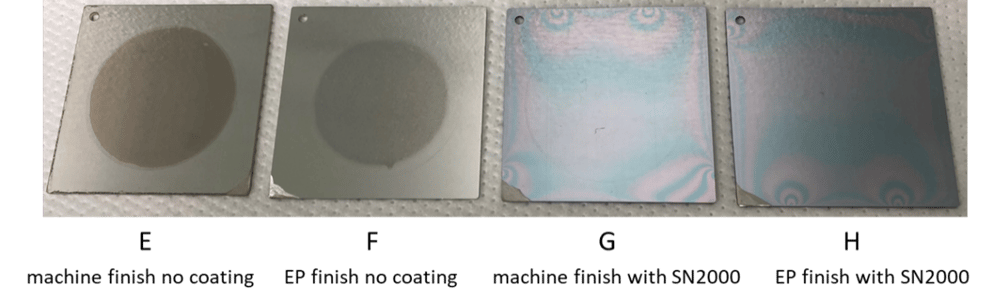

Coating stainless steel with SilcoNert 2000 shows better inertness for trace levels of H2S and MeSH, faster dry down speeds, and improved corrosion resistance when compared to an electropolished stainless steel. Many gas and fluid transfer systems could benefit from the CVD coating technology due to its superior performance, shorter lead times, and lower price when compared to electropolished tubing.
7 Steps to Implementing SilcoTek Coatings Into Your Application
When considering the implementation of SilcoTek coatings or similar technologies in gas and fluid transfer systems, here are some valuable tips to enhance the process:
-
Application Suitability Assessment: Understand the specific requirements of your application. Not all coatings may be suitable for every use case. Assess factors such as the types of substances being transferred, operating conditions (pressure, temperature), and the expected lifespan of the components.
-
Consultation and Expert Advice: Engage with SilcoTek's experts to discuss your system's needs. We can provide guidance on the most suitable coating options and expected performance under your system's conditions.
- Testing and Validation: Conduct preliminary testing or trials with the coated components before full-scale implementation. This allows for validation of the coating's performance in your specific environment and ensures compatibility with your system's requirements.
-
Integration Considerations: Evaluate the ease of integration of coated components into your existing system. Consider factors such as compatibility with other materials and any special handling requirements.
-
Monitoring and Maintenance: Establish a maintenance schedule to monitor the coated components periodically. While these coatings offer enhanced durability, regular inspections can help identify any degradation or wear, allowing for timely maintenance or replacement.
-
Cost-Benefit Analysis: Assess the overall cost-effectiveness of implementing the coatings. Consider factors beyond the initial cost, such as potential savings from reduced corrosion-related maintenance, longer component lifespan, and improved system performance.
By paying attention to these implementation considerations, you can ensure a smoother integration of SilcoTek coatings into your gas and fluid transfer systems, maximizing the benefits and optimizing system performance over time!
For more information about SilcoTek's coatings, please contact our technical service team!
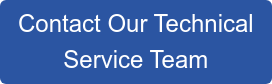