*
A customer recently asked if you can tell if stainless steel tubing has been SilcoTek coated. In this blog we'll discuss coating stainless tubing and how to tell if the coating is there and working properly.
How to Tell if Stainless Tubing is SilcoNert Coated
In this blog post you will learn:
- How to identify coated and uncoated tubing.
- How to assure tubing is performing according to specification.
- How to keep your coated tubing performing at peak performance.
|
Identifying Coated Tubing
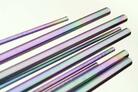
SilcoTek® applies silicon coatings to tubing in 2 ways:
-
- We can coat both outside and inside surfaces of straight tube sticks with a length up to 80".
- We can coat coiled tubing up to 2500 feet (see table below).
For tubing coated on the outside and inside it's relatively easy to tell if the tube is coated. The outside surface will either have an iridescent rainbow color or will be gray in appearance. Our nano-thin coating refracts light and results in a multi-color rainbow appearance that makes it easy to visually inspect the tubing for the coating. If the tubing color begins to change over time that means the coating is eroding and may be compromised. Get CVD coating information: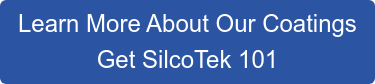
The different colors of the coating can be attributed to angstrom-level thickness variations across the surface. All SilcoTek coatings have a thickness of <1.5µm.
Certain coating processes (e.g. Silcolloy, SilcoGuard) result in a thicker layer and have a silver/matte gray appearance, while thinner coatings (e.g. SilcoNert) exhibit the ‘rainbow’ colors as seen below.

It's a different story for coiled tubing. Coiled tubing is coated on the inside only. Because our process involves heating parts prior to coating, the outside of coiled tubing will have varying degrees of mild heat oxidation that results in a light brown color on exterior surfaces.
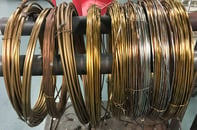
However having a brown surface only indicates the tube has been exposed to heat, not necessarily that the interior of the tubing is coated. To be sure the tube is coated internally you'll need to either section a small portion of the tube to visually inspect the interior of the tube or you should chemically test the tubing to be sure the surface is inert or non-reactive.
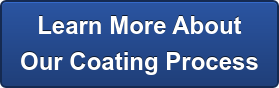
Assuring a Coating is Performing to Specification
Chemical testing can range from a calibration test (a test used by your company or specified by industry standard for the particular use of the tubing) or by challenging the tubing by flowing an known reactive compound that normally interacts with uncoated stainless steel but does not react with silicon coatings. Reactive compounds range from H2S, mercaptans, or other chromatography calibration standards. Click here to learn more about inertness testing.
More About Coating Coiled or Rolled Tubing
Coiled tubing can be coated internally only with a maximum continuous length that is ID dependent. See table below:
.jpg?width=319&name=Max%20coil%20length%20table%20(003).jpg)
Other tubing requirements:
- Maximum coil OD for tubing > 1/16" OD: 36"
- Maximum coil OD for tubing 1/16" OD or smaller: 18"
- Must be shipped on a metal spool or bound with metal wire. No spools made of wood, plastic, or other flammable materials.
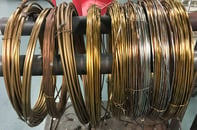
SilcoTek’s process for treating coiled tubing results in a uniform coating throughout the interior of the tubing from end to end. The exterior surface of coiled tubing is not coated, but it will exhibit a change in appearance after being oxidized by the high temperatures of our CVD coating process. This resulting external appearance will vary based on the specific elemental composition of the tubing substrate.
Can SilcoTek Coat Small Diameter Tubing?
Yes! Our unique chemical vapor deposition process is performed in the gas phase, so even the smallest channels and tightest tolerances will be adequately coated along with the rest of the part. We also have the ability to coat certain tube configurations internally-only.
Can I Tell if Small ID Tubing is Coated?
We proved this by coating a 1/16" OD, .4mm ID tube with multiple bends both internally and externally. After coating, the tube was cut open to examine the coating at the center-most point inside the tube. In addition to the external coating on the tube, a quick visual inspection shows the vibrant purple-colored SilcoTek coating inside the narrow bore.
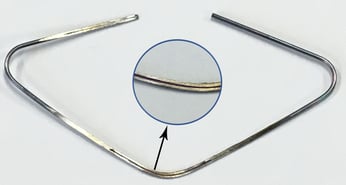
Measuring Coating Thickness in Tubing and Other Surfaces
The thickness of the coating throughout the tube was verified by a Filmetrics F40-Series Thin Film Analyzer and it was confirmed to meet our specifications. SilcoTek coatings are not applied with line-of-sight processes that lead to inconsistent deposition and uncoated areas. With our process, 100% of your parts are coated, even if the design is complex or the pathways are tortuous. Have a question about our coatings?
Go to our web page: CVD Coating Frequently Asked Questions
Corrosive Applications
We recommend all end users test SilcoTek® coatings in corrosive applications to better understand the performance and potential lifetime prior to installing coated parts into service. Since every corrosive application is different, several factors impact the coating's lifetime, like exposure duration, concentration, temperature, abrasion/agitation, galvanic action, etc. Testing the coating under conditions similar to the application will help to determine the coating performance over the life of service. SilcoTek has tested our coatings under several common corrosion environments. To learn more go to our latest corrosion presentation.
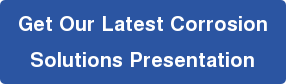
Our goal at SilcoTek® is to partner with you to help solve your corrosion problems, so we put a priority on helping you evaluate our coatings. This includes gathering relevant test data, providing samples, coating your test pieces, and putting our technical experts on your project to find a solution that works. Please contact us to discuss your application and establish a testing and validation plan.
Keep Coated Tubing Running at Peak Performance
The best way to keep coated tubing running at peak performance is to follow a few simple tips:
- Avoid abrasive damage by filtering the flow path.
- Don't steam clean tubing. Steam can carry particulates that can cause activity and may damage the surface. Steam can also make silicon surfaces reactive.
- Clean the surface periodically to remove trace contaminants.
Click on the thumbnail below to get CVD coating care tips to optimize performance and coating life.
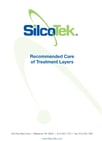
Keep in touch! Follow us on LinkedIn, ask us questions engage your insights!

*Image courtesy of New World Stainless