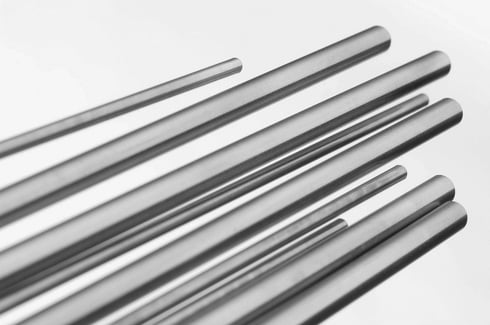
At SilcoTek, we coat lots of tubing with our inert, corrosion resistant coatings. But what's the longest straight tube or coiled tube I can have coated? And how do they perform?
About Coating Straight Tubing and Coiled Tubing
In this blog post you will learn:
- How SilcoTek coats straight tubing with their inert and corrosion resistant CVD coatings.
- Get information about the maximum length of coated straight and coiled tubing.
- Learn about how coated tubing is more inert and corrosion resistant than uncoated tubing.
|
About the SilcoTek® Coating Process
First let's talk about the tubing coating process. SilcoTek's CVD coating process is able to treat 2 tubing configurations, coiled rolled tubing and straight sticks. Our chemical vapor deposition process has some limitations relating to each tubing configuration which we'll highlight below.
Tubes are coated by a process called chemical vapor deposition (CVD). The CVD process starts by preparing the tubing surface for coating. Surfaces are optimized for the highest coating quality by cleaning the surface using proprietary methods that employ environmentally friendly cleaning solutions.
Want to learn more about effective cleaning and maintenance of process or analytical flow paths? Click on our link below to read a presentation from our coating care webinar.
After surface preparation, the tube is heated to enable the coating reaction. Then process gasses are injected either into the inner bore of the tubing (used when coating coiled tubing internally) or the process gas is injected into a reaction chamber which contains the tubing. This process is used to coat straight tubing on internal and external surfaces.
In order to reliably coat the internal tube surface, we limit the maximum straight tube or coil length as summarized below.
Coiled/Rolled Tubing 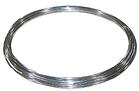
- Coated internally-only
- Maximum continuous length:
.jpg?width=435&name=Max%20coil%20length%20table%20(003).jpg)
We also have some general tube roll limitations to assure we're able to properly load tubing coils into our process ovens. We ask that coiled tubing be shipped either on metal spools or bound with metal wire to be sure we don't damage the coil while processing.
- Maximum coil OD for tubing > 1/16" OD: 36"
- Maximum coil OD for tubing 1/16" OD or smaller: 18"
- Must be shipped on a metal spool or bound with metal wire. No spools made of wood, plastic, or other flammable materials.
Have a question about coating tubing or other parts? You can discuss your application by using our chat box below. You'll be instantly connected with a coating expert who can answer all your questions. Not a fan of chat? You can email us be clicking on the box below.

Coating Straight Tubing
Because straight tubing is coated in a reaction chamber, tubing length is limited to the size of the coating reactor chamber. Our largest tubing reactor can accommodate a maximum tubing length of 80 inches (approximately 2 meters).
Coating Capabilities, Straight Tubing:
- Coated both internally and externally
- Maximum length: 80"
SilcoTek® is able to coat a range of tubing diameters from 1/16in up to diameters exceeding 6 inches. Contact our technical service team to learn more.
What About Coating Tubing Interior Diameters?
Our unique chemical vapor deposition process is performed in the gas phase, so even the smallest channels and tightest tolerances will be coated. We also have the ability to coat certain tube configurations internally-only. To summarize coating tubing ID, if we can get our process gasses into the tube we're able to coat the part. For long and extremely narrow tubes we'll limit the tube length to be sure we're able to achieve the desired coating performance.
Have a question about our coatings? Go to our Frequently Asked Questions page.

We proved coating aspect ratio capabilities by coating a 1/16" OD, .4mm ID tube with multiple bends both internally and externally. After coating, the tube was cut open to examine the coating at the center-most point inside the tube. A quick visual inspection shows the vibrant purple-colored SilcoTek coating inside the narrow bore.
The thickness of the coating throughout the tube was verified by a Filmetrics F40-Series Thin Film Analyzer and it was confirmed to meet our specifications. SilcoTek coatings are not applied with line-of-sight processes that lead to inconsistent deposition and uncoated areas. With our process, 100% of your parts are coated, even if the design is complex or the pathways are tortuous or not line-of-sight.
|
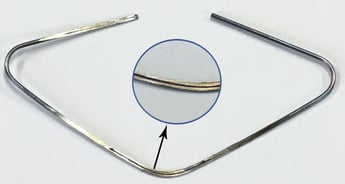
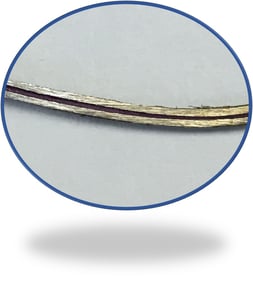
|
What About Joining Tubing?
You can join coated straight sticks or coiled tubing by using compression fittings (coated to assure a continuous coated flow path). You can also weld face seal flanges onto the tubing before coating if a face seal is desired.
Coated tubing can be welded; however, welding coated surfaces will remove the SilcoTek coating ~2-4mm in all directions from the heat affected zone. SilcoTek can coat over most high-quality welds and materials, for a complete material compatibility list, go to our material compatibility guide.
The Results- Tubing Inertness: Testing the Effectiveness of Coated Tubing
Comparative Testing shows SilcoTek® coatings improve performance & prevent common sampling and test problems such as:
- Lost peaks
- Peak tailing
- Calibration errors
- Ghost peaks
SilcoNert® 2000 coated tubing offers part-per-billion sensitivity without costly system redesign or new process development, saving labs time while improving quality. Comparative testing demonstrates the effectiveness of SilcoNert. Reactive flow paths (First GC chromatograph below) cause peak distortion, lost peaks, and can lead to retesting or test failures. SilcoNert coated flow paths (second chromatograph) assure complete peak resolution without distortion.
Uncoated Flow Path Surface: Lost Peaks and Poor Peak Shape
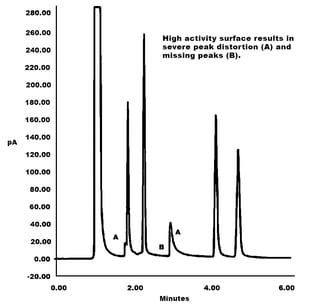
SilcoNert Flow Path (below): Prevent Peak Loss and Distortion Get Higher Quality Results
.png?width=295&name=GC%20SilcoNert%20Good%20Peaks%20(002).png)
Corrosion Resistance of Tubing
Can long tubes be coated to improve corrosion resistance? Yes! A CVD coating like Dursan®, for example, will improve the corrosion resistance and inertness of tubing, offering a multitude of benefits such as higher reliability and improved test sensitivity and quality (offering part-per-million test sensitivity).
The chemical vapor deposition process used to coat stainless steel flow paths will prevent corrosive disruption of grain boundaries and act as an inert barrier to aggressive and sticky compounds. Dursan coated analytical flow paths will prevent HCl, sulfuric acid, bleach, and other corrosives from pitting and attacking stainless steel surfaces. Here are some examples of how Dursan and Silcolloy® can improve corrosion resistance.
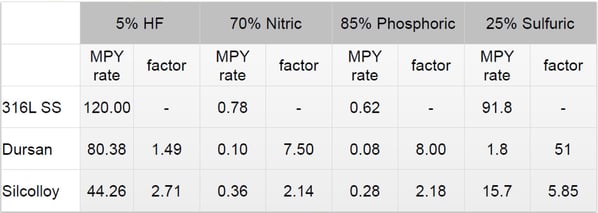
Dursan® can increase corrosion resistance by 10x or more through preventing interaction of the analyte or process fluid and the stainless steel surface. Dursan exceeds typical metal passivation capability. Immersion testing in 6M hydrochloric acid (HCl) shows that Dursan coated surfaces prevent surface attack and protect stainless steel from rust by orders of magnitude compared to passivated stainless steel, preventing gas supply system corrosion.
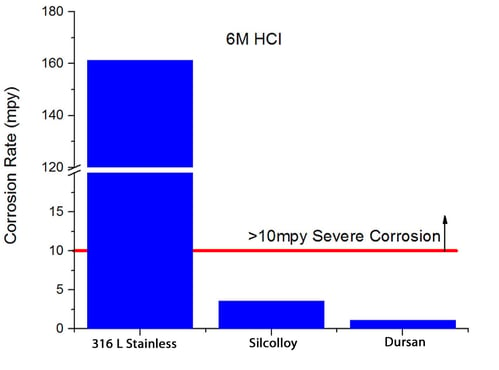
Click here to learn more about improving the corrosion resistance and durability of analytical systems.
Dursan offers inertness, durability, fouling, and carryover contamination benefits for process analytical, gas supply, process sampling, stack and flare sampling. Want to learn how our coatings improve purity and yields?

HBr corrosion resistance
Comparative HBr corrosion testing shows that Dursan® and Silcolloy® coated stainless steel surfaces improve flow path corrosion resistance by up to an order of magnitude over uncoated stainless steel. Virtually all stainless steel surfaces can be coated including small and large bore tubing, regulators, stainless steel frits, fittings and valves.
/hbr.png?width=499&name=hbr.png)
Get more corrosion application information and benefits for your process or products. Get our corrosion presentation.
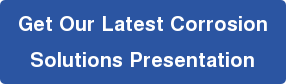
Conclusion
Protecting tubing flow paths from rust while making that tubing inert and non-reactive can revolutionize the reliability of process and analytical sampling. Contact our technical service team to discuss your application. Need an inert hydrophobic surface? How about an anti-fouling surface that's wear resistant? Our team can help match the best coating for your application. Follow us on LinkedIn to keep up with the latest in advanced coating technologies.
