The semiconductor industry is experiencing rapid advancements, with projections indicating a 15% growth in 2025, driven by innovations in chip design, AI integration, and the expansion of 5G technologies. As manufacturers strive to meet the escalating demand for high-performance and reliable components, the significance of material integrity and contamination control has never been more critical.
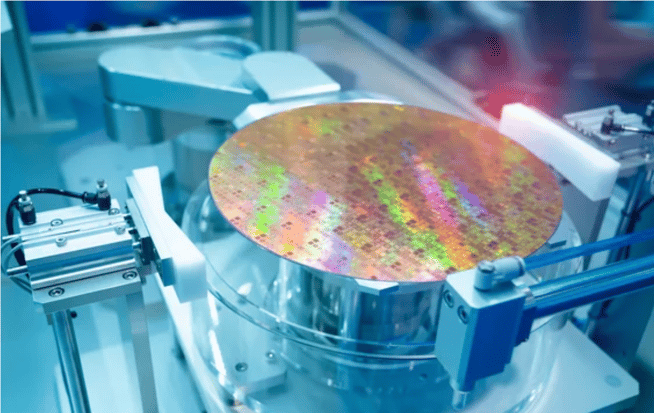
The Role of SilcoTek® Coatings in Semiconductor Manufacturing
SilcoTek's chemical vapor deposition (CVD) silicon barrier coatings are engineered to enhance the performance and longevity of semiconductor manufacturing equipment. By providing a protective layer, these coatings prevent ion and particulate contamination, which improves process yields and ensures product purity.
As memory continues to add layers, etch becomes an ever increasingly important step and SilcoTek coatings help maintain the process purity required to achieve new, faster, and smaller devices. With market demand increasing, SilcoTek's coatings will be more important than ever to keep up. New, emerging technology will require even more precise manufacturing with little room for error.
Key Benefits of SilcoTek Coatings:
-
Corrosion Resistance: In semiconductor fabrication, equipment is frequently exposed to corrosive gases and chemicals. SilcoTek's coatings, such as Siltride® and Dursan®, offer protection against corrosion, reducing maintenance time and costs.
Above is a photo of a Siltride coated quench sleeve (left) in comparison to an uncoated quench sleeve (right).The considerable reduction in waste throughout the whole semiconductor manufacturing process is incredibly significant in sub-fab operations all over the world.
The mass loss graph above shows that 3 parts (red dotted line) failed during the test period with over 40% mass loss, while the Siltride coated part (blue line) remained structurally sound with less than 2% mass loss. Read about our study with Samsung Austin at the link below:
Applications in Semiconductor Processes:
-
Etch: During the etching process, equipment is susceptible to metal corrosion from etch gases resulting in metal ions contaminating the process stream and potentially the wafer surface. Applying SilcoTek coatings to critical flow paths prevents such contamination, ensuring the integrity of the etched features.
-
Atomic Layer Deposition (ALD): Maintaining ultimate purity in ALD processes is essential and new, extremely volatile precursors are making this more and more difficultis essential and new, extremely volatile precursors are making this more and more difficult. Coating exposed surfaces with SilcoTek solutions reduces carryover and corrosion, ensuring consistent and defect-free thin films.
-
Epitaxy: Epitaxial growth processes require pristine environments to prevent defects. SilcoTek coatings significantly reduce contamination and maintenance caused by corrosion, facilitating high-quality crystal growth.
- Gas Transfer: Ensure the high purity of gases by using coatings that serve as barriers against impurities, which is crucial for maintaining the purity required for semiconductor processes. Eliminate surface reactions by applying inert coatings that prevent unwanted chemical interactions, thereby preserving the pristine condition of equipment surfaces.
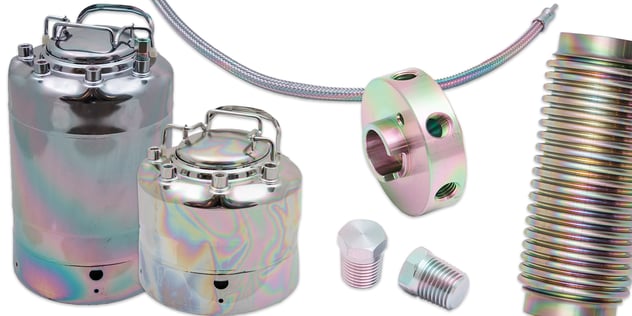
Supporting Sustainable Manufacturing
In addition to performance enhancements, SilcoTek coatings contribute to the sustainability of semiconductor manufacturing. By protecting equipment from corrosion and contamination, these coatings reduce the frequency of part replacements and maintenance interventions, leading to decreased material consumption and waste generation. Coatings can also be used to create the possibility of part refurbishment to save even more beyond part replacement. SilcoTek also offers cleanroom ISO Class 6 post-coating precision rinsing, drying, helium leak check, vacuum packaging, and custom labeling to meet strict semiconductor industry standards.
Conclusion
As the semiconductor industry continues to innovate, the demand for high-purity, reliable, and efficient manufacturing processes intensifies. SilcoTek's advanced CVD coatings offer a proven solution to the challenges of corrosion, contamination, and troublesome maintenance challenges, allowing manufacturers to achieve superior product quality and maintain operational standards.
Have questions about SilcoTek's coatings? Reach out to our coating experts!