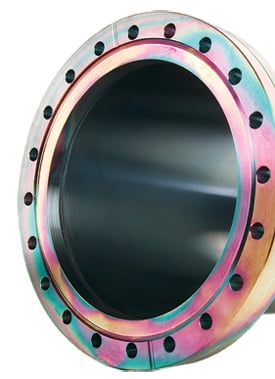
We offer coatings that prevent corrosion, improve analytical sensitivity, repel water, and prevent fouling. But did you know we also offer barrier coatings for research, UHV, and semiconductor applications?
Silcotek® coatings are used to enhance the surface and material properties of instrumentation throughout industry. But there's one coating property that has many applications for research, ultra high vacuum (UHV) and semiconductor fabs that's not discussed vary often; that's high purity, specifically high purity silicon.
In this blog post you will learn:
- How high purity CVD coatings improve the performance of UHV, semiconductor, and research systems.
- Benefits of barrier coatings in precision contamination free environments.
- How improving corrosion resistance can improve yield.
- How low surface energy coatings improve hydrophobicity.
- How to determine the composition of coatings.
|
Let's discuss the benefits and applications of a high purity coating.
Vacuum Systems
SilcoTek® barrier coatings dramatically reduce outgassing of stainless steel surfaces, improving pump down efficiency and virtually eliminating surface burn-in requirements. Coated vacuum and critical flow path surfaces improve process efficiency and productivity.
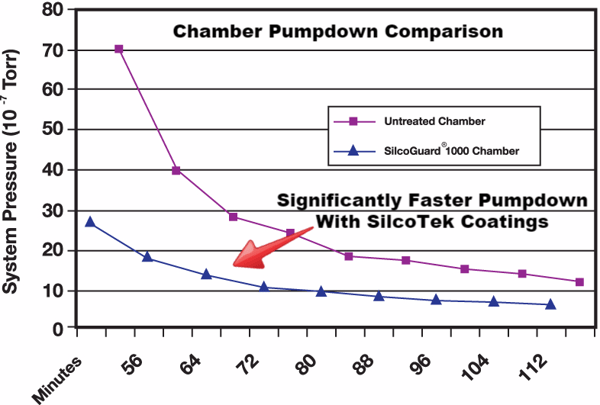
How do they work? SilcoTek® high purity silicon coatings do not adsorb moisture or other system contaminants. Our high durability silicon coatings bond securely to chamber and even flexible bellows surfaces, so the entire chamber and seal areas are coated in a moisture repelling non stick and non reactive coating. Because the UHV chamber is coated by a chemical vapor deposition (CVD, see previous blog posts about CVD) the coating will flex with metal surfaces while remaining tough and durable, allowing leak free face seal and conflat sealing. The pump down graph above shows how a coated chamber can benefit from a high purity coating. The uncoated chamber will take about 70% longer to achieve a similar base pressure compared to the coated chamber.
Benefits of a high purity coating in reactors:
- No contamination from metals
- Faster chamber pump down
- Easier chamber cleanup
- Improved process control
- Minimal burn-in
Interested in testing our coatings? Get free test coupons or contact our Technical Service Staff to arrange a coating trial.

Coating Solutions for Process & Gas Delivery
Anhydrous and aqueous semiconductor process chemicals can be highly reactive and corrosive to stainless steel gas delivery systems; causing yield robbing particulate contamination and premature system failure. High purity corrosion resistant silicon barrier coatings, like Dursox®, prevent surface reactivity and metal ion contamination caused by corrosion. Get a list of chemical compatibility and corrosion resistance by going to our our Semicon Coating Compatibility Page.
Go To Semicon Coating
Compatibility Page
Common process chemicals like hydrochloric acid can corrode flow paths and cause contamination. High purity Dursox®, our corrosion resistant CVD coating for high purity applications, can improve system corrosion resistance 3x or more. The graph below highlights the corrosion resistance of Dursox coated stainless steel. ASTM G31 72 hour immersion in concentrated hydrochloric acid showed a 10x improvement in corrosion rate compared to uncoated stainless steel.
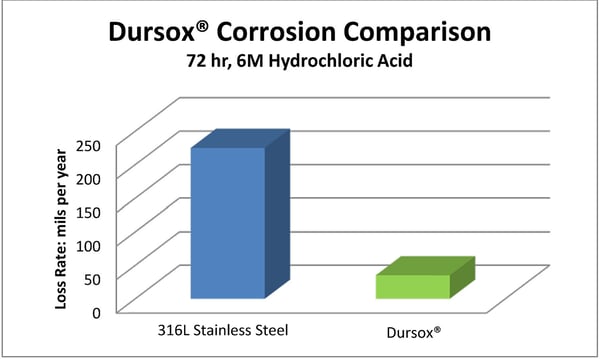
How do coatings prevent corrosion? SilcoTek high tolerance, precision CVD silicon coatings protect and improve critical surfaces throughout semiconductor process systems. Coating all critical flow path surfaces will prevent ion and particulate contamination & improve process yield. Coat the entire flow path to assure maximum performance.
Gas system benefits:
- Significantly improve corrosion resistance.
- Eliminate surface reactivity of stainless steel.
- Improve process yield.
- Maintain purity of process and calibration gases.
Want to evaluate a coating for purity and inertness? Read our blog post, "How to Test an Inert Coating for Reactivity and Purity".
Product Testing
If sophisticated analytical tools like scanning electron microscopes are used for quality control, analysts can increase process throughput and prevent product adulteration during testing by coating chamber and critical flow path surfaces with a contaminant free non reactive surface. Moisture and other contaminants don't stick to SilcoTek® coatings, improving SEM pumpdown and preventing product contamination.
The moisture repelling comparison below highlights the hydrophobic characteristics of various silicon surfaces. Our most hydrophobic surface, Notak™, is a polymer based material that is bonded to the surface.
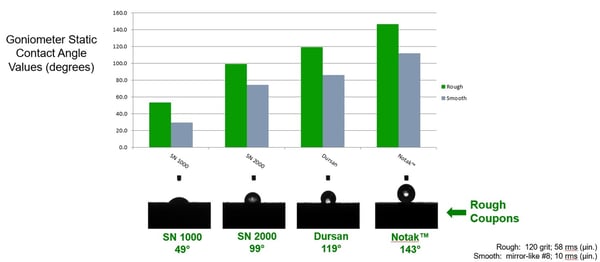
How do Dursan® and Notak™ improve moisture resistance? They feature a low surface energy high contact angle surface that is bonded to all wetted surfaces by chemical vapor deposition. Moisture contact angles of over 140° can be achieved. That means water and other contaminants won't bond to flow path surfaces, preventing product contamination .
Product Testing Benefits
- Rapid contaminant free testing
- Higher productivity
- Fewer test failures
Etch & Deposition
Corrosion in semiconductor process flow paths can result in yield robbing particulates and metal ion release. SilcoTek corrosion resistant barrier coatings can be bonded to the most intricate internal flow path surfaces to dramatically improve the corrosion resistance of stainless steel and metal alloy surfaces. Exposure to severe corrosives like HBr and hydrochloric acid in semiconductor applications can be devastating to stainless steel surfaces. Silcolloy® or Dursan® coated stainless steel improves corrosion resistance by orders of magnitude. Improving yields in sensitive 10nm and 14nm applications and improving performance over Yttria coatings.
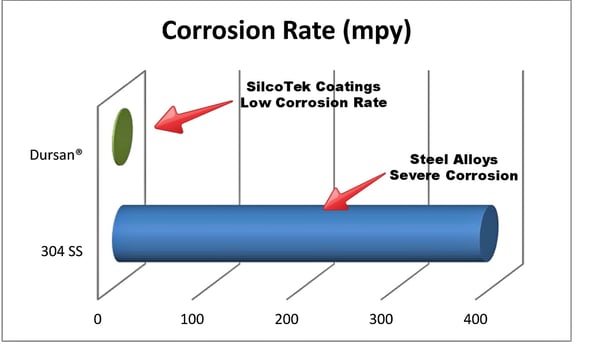
The benefit of a CVD applied high purity, corrosion resistant, thermally stable silicon barrier coating.
- Etch: Eliminate barrier contamination, increase life, eliminate burn-in
- ALD: Enhance purity, reduce carryover and corrosion
- EPI: Eliminate particulate generation, improve stainless steel corrosion resistance
- Ozone: Stable flow path
- OLED: Improve yield and efficiency
What are these coatings made of?
Most of our coatings are made of silicon. We functionalize (or "dope") the surface for specific inertness performance but our Silcolloy coating and SilcoNert 1000 coatings are made of silicon with a native oxide surface. Non reactive silicon makes an excellent barrier which prevents contamination from the base metal, glass, or ceramic surface. The Auger Electron Spectroscopy (AES) diagram below of a SilcoNert surface shows the coating contains silicon and oxygen. Note the diffusion zone where the silicon is bonded to the stainless steel base.
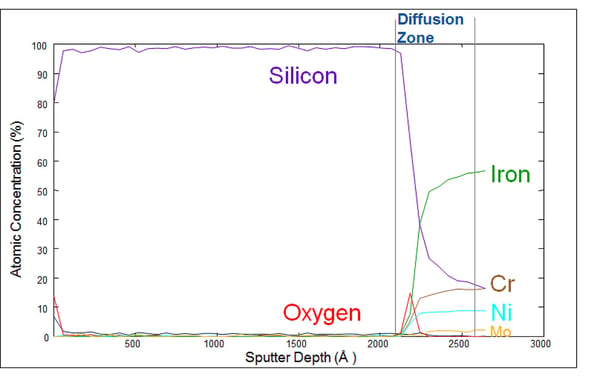
Dursan® is a different coating consisting of silicon, oxygen and carbon. The Auger plot below shows the coating depth and a similar diffusion zone to SilcoNert.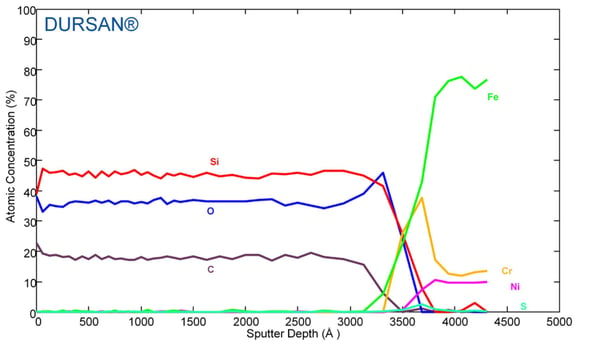
Dursox is similar to Dursan in that it contains oxygen, carbon and silicon, although concentrations are different. The X-ray Photoelectron Spectroscopy (XPS) data below shows no metal signals in the coating.
Want to learn more about how our coatings improve the performance of your products?
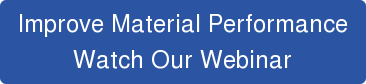