In today's dynamic landscape, the raw material supply chain plays an important role in meeting increasing global demand. The need for enhanced material purity has never been more critical, particularly in semiconductor manufacturing, where the standards for gas delivery purity are important for successful production. Modern production faces challenges in achieving purity, especially between reactive metal surfaces like stainless steel. Additionally, the escalating cost and scarcity of inert exotic alloys further complicate the need for purity. Particularly, where Halogens are concerned.
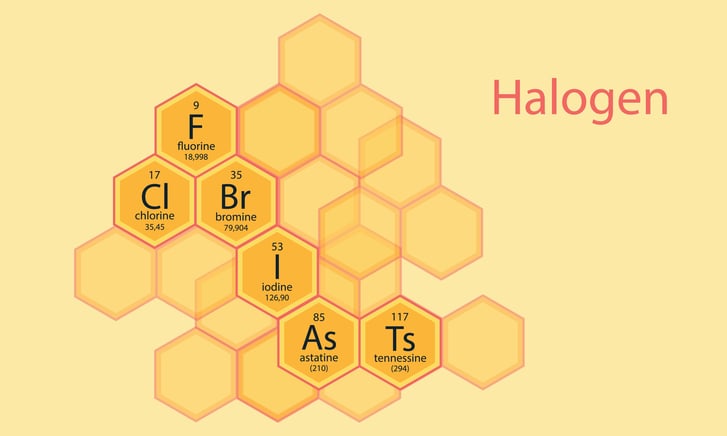
This is where SilcoTek steps in as an industry leader, offering game-changing coatings that deliver a metal-free surface and offsetting increasing manufacturing costs. Let's explore how SilcoTek coatings revolutionize gas delivery systems:
1. Meeting Purity Standards:
- In semiconductor manufacturing, adherence to stringent purity standards is crucial. SilcoTek coatings address the challenge of achieving purity in modern production settings, where reactive metal surfaces and the limitations of exotic alloys pose obstacles.
2. Preventing Metal Contamination:
- SilcoTek's advanced coatings are inert, metal-free, chemical vapor deposition (CVD) coatings, that prevent 99% of metal ion contamination in liquid precursor canisters. This ensures a clean and uncontaminated process, essential for many applications.
3. Cost Reduction and Extended Equipment Lifespan:
- By preventing metal contamination and improving corrosion resistance, SilcoTek coatings contribute to a significant reduction in the cost of equipment ownership. The extended lifespan of coated parts results in fewer replacements, translating to lower manufacturing costs compared to exotic alloys.
4. Chemical Compatibility and Purity:
- SilcoTek's chemically compatible amorphous silicon structure produces a chemically pure layer, improving compatibility between equipment and process streams. The coatings ensure that the process or analytical stream remains uncontaminated by metals, providing consistent performance.
5. Hydrophobicity and Corrosion Resistance:
- SilcoTek coatings offer improved hydrophobicity over uncoated stainless steel. The coating process produces a continuous, pinhole-free corrosion barrier, especially effective in aggressive acidic conditions.
6. Uniformity and Protective Layer:
- The SilcoTek process ensures uniformity in coating application, creating an inert, amorphous silicon surface. This not only maintains precision tolerances but also establishes a protective barrier layer that shields parts from corrosion and metal ion leaching.
How SilcoTek Helps
When dealing with halogens like Chlorine, Bromine, and Fluorine, SilcoTek's coatings provide a barrier between the sample and the substrate, leaving little room for metal contamination, corrosion, and moisture.
Chlorine
SilcoTek has conducted comparison studies between our coatings and other alloys to show how they perform against HCl. Take a look at how they compare to commonly used super alloys like Hastelloy, Monel, and Inconel.
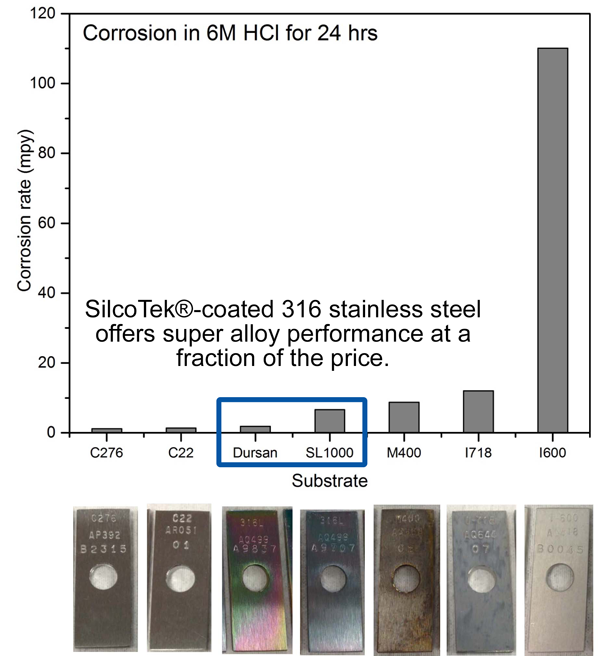
Bromine
Silcolloy and Dursan were both compared to 316 stainless steel when immersed in HBr solution. A 24-hour immersion study shows that Silcolloy and Dursan reduce corrosion rates by an order of magnitude. After immersion, the Silcolloy and Dursan test coupons remain corrosion free.
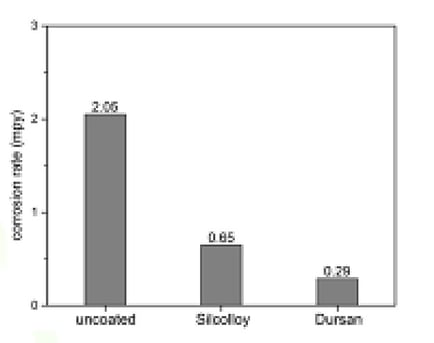
Fluorine
HF's corrosive nature can make it very difficult to combat. Using SilcoTek's CVD coatings can help to reduce and slow the progression of corrosion. Our coatings provide 5X improvement over uncoated stainless steel at a fraction of the price of exotic alloys.
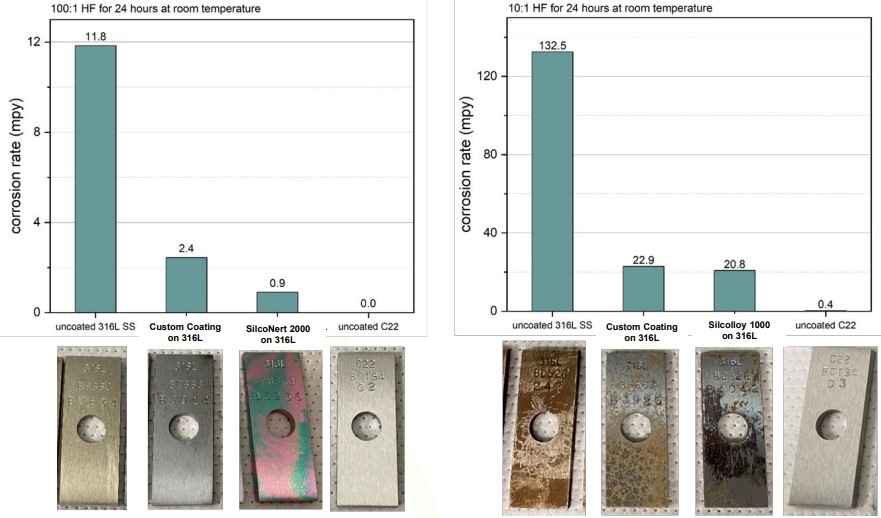
The SilcoTek process produces a uniform, inert, amorphous silicon surface. The TEM EDS image below shows a cross section of the coating (red) applied to the substrate surface (blue). The profile shows a uniform silicon layer which will minimize disruption to flow path surfaces.
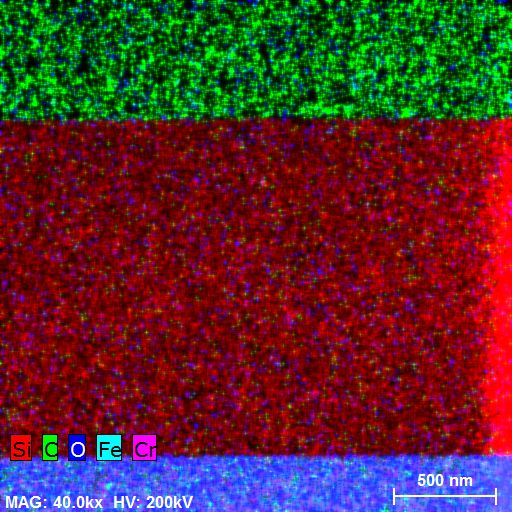
Conclusion
In essence, SilcoTek coatings go beyond conventional solutions, providing a comprehensive and effective approach to enhancing gas delivery system performance. From preventing metal ion contamination to improving corrosion resistance, SilcoTek's innovative coatings contribute to the production of higher quality, longer-lasting end products in semiconductor manufacturing and beyond.