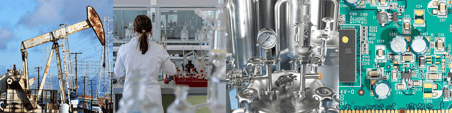
We tested and compared the corrosion resistance of coated, uncoated, and electropolished stainless steel. The results show a clear winner and supports the idea that more is more.
Corrosion Resistance of Electropolished and Coated Stainless Compared
This blog post compares the corrosion resistance of 304 stainless steel substrate with four different surface conditions: uncoated with a regular machine finish ( test item "A"), uncoated with electropolish and passivation (test item "B"), Silcolloy® coated with a regular machine finish (test item "C"), and Silcolloy coated with electropolish and passivation (test item "D"). The test was done in 5% hydrochloric acid (HCl) solution via linear polarization resistance. The results show corrosion resistance is highest for the combined coated and electropolished surface. Showing once again that more is in fact more. The order of improvement (worst performance to best) followed the ABC's as A << B < C << D.
In this blog post you will learn:
- How surface finish affects corrosion resistance.
- How corrosion resistant coatings like Silcolloy can significantly improve corrosion resistance.
- How a Silcolloy coated electropolished surface offers improved stainless steel corrosion resistance.
|
Electropolished Surface and SilcoTek Coating Background
The surface finish of a part has a significant impact on the surface properties of the part. In general, less surface area means less active metal sites, and correspondingly:
- Better inertness (i.e. anti-adsorption) properties.
- Shorter vacuum pump down times.
- Improved corrosion resistance.

For stainless steel, electropolishing (EP) is a well-known method to achieve a smooth surface finish and reduced surface area. Previous studies show that EP tubing outperformed conventional non-EP tubing, when uncoated, in both sulfur inertness analysis and moisture wet-up and dry-down response times in gas transfer and vacuum applications.
The same studies also found that SilcoTek’s SilcoNert® 2000 coating greatly enhanced performance, resulting in a final ranking from best to worst: SN2000-coated EP tubing > uncoated EP tubing > uncoated non-EP tubing.
Get the latest data on how to improve corrosion resistance. Watch our corrosion webinar.

The above studies combined two surface treatment techniques, EP and SilcoTek’s CVD coating (Silcolloy®), into one test piece to deliver the optimal end results. Some customers ask when used separately how coating vs. electropolish compare in corrosion applications. This blog post aims to provide insight in this regard, comparing corrosion resistance of 304 stainless steel coupons in diluted hydrochloric acid in four surface conditions as illustrated in Figure 1 below.
Figure 1: Illustration of the four surface conditions compared in this blog post.
Corrosion resistance is a parameter that bears relevance to the other surface properties such as inertness and moisture retention, as better corrosion resistance generally indicates a more passivated surface, improved barrier properties from the coating and/or less exposed active metal sites, all of which are beneficial to the other surface properties mentioned above.
Corrosion resistance of 304 SS flat coupons were measured by exposing individual testing surfaces to 5% hydrochlorica acid (HCl) solution for one hour, then conducting a linear polarization resistance scan on each sample. This is an accurate and rapid testing technique commonly used in real time corrosion monitoring of metallic samples, which can report the corrosion rate of the system at the time of the measurement.
To evaluate a corrosion resistant coating, the test essentially examines two “metal finish” conditions of 304 SS, with and without coating, yielding four final surface conditions. Instead of our inert coating, SilcoNert®2000, SilcoTek’s Silcolloy® coating was used in this study as corrosion resistance is one of the major functions of Silcolloy. Silcolloy shares the same amorphous silicon chemistry with SilcoNert but is a thicker coating and does not include the surface functionalization found in SilcoNert. For an in-depth analysis of how coated electropolished surfaces can improve inertness and corrosion resistance, read our blog.
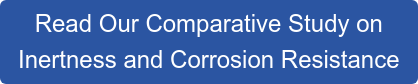
It should also be pointed out that the electropolish finish “EP finish” in this study included nitric acid passivation treatments post EP. This is because chemical passivation is often a follow up process after electropolishing to maximize the benefits of the electropolish process. The electropolish process focuses mainly on mechanical improvements of the surface by removing surface impurities and damage, and by smoothing the surface which reduces surface area and improves cleanability.
EP alone, however, does not achieve the Cr/Fe (i.e. chromium to iron) ratio that is attained by a chemical passivation process, which focuses primarily on improvements of the stainless steel metal’s surface chemistry, i.e. Cr/Fe ratio. By carrying out the EP and passivation processes in tandem, the present study ensures that we are comparing the coating to the most competitive metal finish condition that surpasses either EP or passivation treatment alone. Experimentally, the electropolish service was provided by a third-party vendor whereas the nitric acid passivation was carried out in-house at SilcoTek® per ASTM A967/A967M nitric 3 standard.
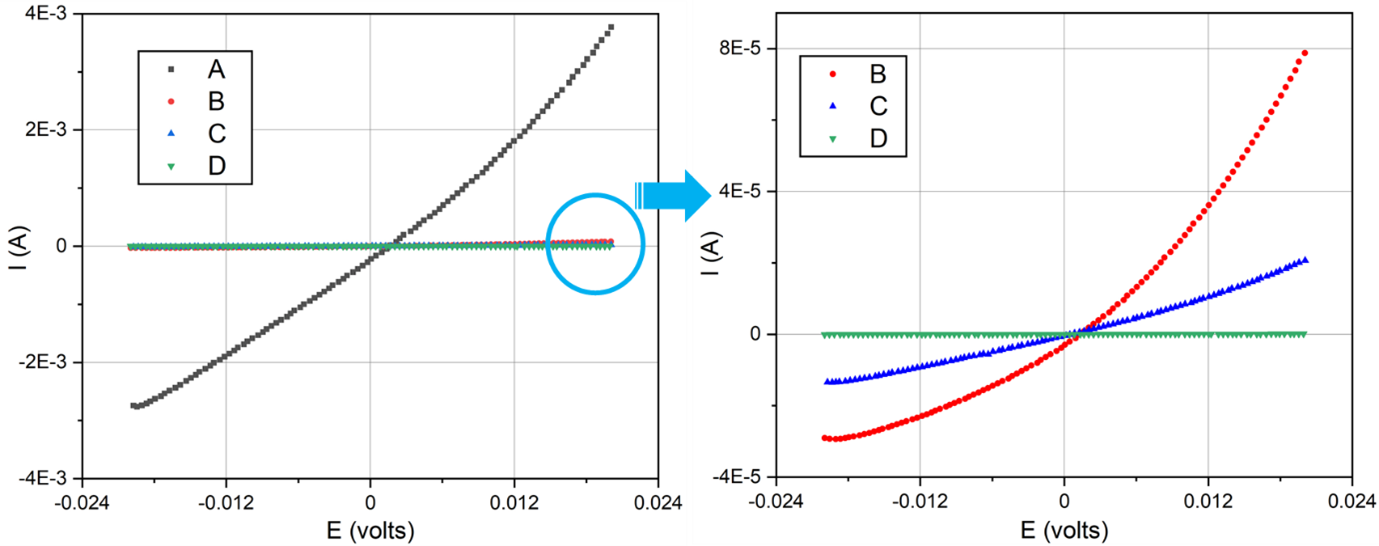
Figure 2: Linear polarization resistance scans of 304 SS coupons in four surface conditions after exposure to 5% HCl solution for one hour. The flatter the curve (i.e. closer to zero on the y-axis), the better the corrosion resistance. A: machine finish no coating; B: EP finish no coating; C: machine finish with Silcolloy; D: EP finish with Silcolloy
Figure 2 (above) shows the linear polarization resistance scans of the four surface conditions after immersion in 5% HCl solution for one hour. Table 1 summarizes the corrosion current and corrosion rate values calculated from the test. Condition A exhibited far worse corrosion rate than the other three conditions. The corrosion rate can be qualitatively assessed by the “flatness” of the curve, i.e. the slope of the curve indicates corrosion rate, so flatter curves correspond to slower corrosion rates. Figure 2 (right image) zooms in on conditions B-D to get a clearer comparison of the three. The results show that when used separately, the Silcolloy® coating is a superior surface treatment to EP + passivation, having a corrosion rate of only one third of the latter. When used in combination (Silcolloy coated electropolished surface), condition D, delivered the best performance by at least two orders of magnitude.
Figure 3 shows photos of coupons representing the four surface conditions after the polarization resistance scan experiment, with visible corrosion on sample A but no visual signs of corrosion on samples B-D (although B-D do have measurable differences in corrosion rates as shown in table 1 below).
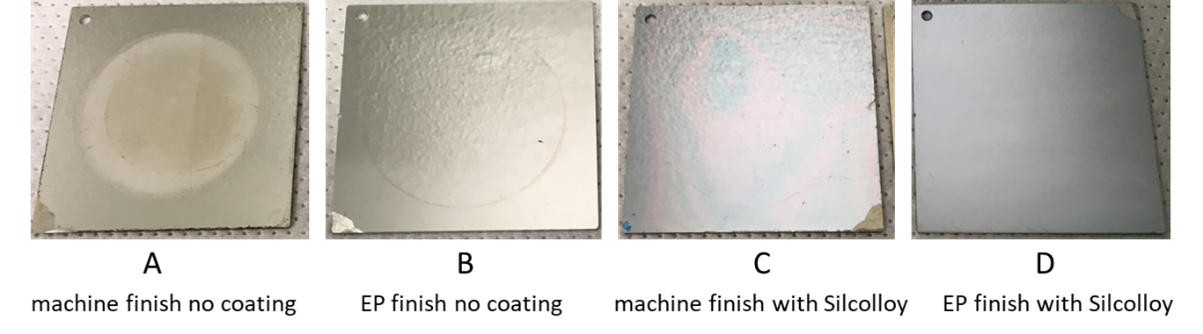
Figure 3: Photos of coupons show that the EP finish with Silcolloy (D) has the best appearance and provides the best corrosion resistance after the polarization resistance scan in 5% HCl solution (one-hour exposure to the acid)
Table 1 Corrosion Comparison
Sample
|
A
|
B
|
C
|
D
|
condition
|
machine finish no coating
|
EP finish no coating
|
machine finish with Silcolloy®
|
EP finish with Silcolloy®
|
corrosion current (µA)
|
4000
|
64
|
21
|
0.083
|
corrosion rate (mpy)
|
125.3
|
2.01
|
0.66
|
0.0025
|
Improvement factor
|
N. A.
|
62x
|
190x
|
50120x
|
Table 1: Corrosion current and corrosion rate values calculated from the linear polarization resistance scans
Summary:
This blog post summarized a corrosion resistance comparison study of 304 SS samples under four different surface conditions. Two metal finishes, i.e. regular machine finish vs. electropolishing and passivation were examined, with and without coating, yielding four final surface conditions (A-D as shown in Table 1). The results show that when used separately, coating is a superior surface treatment to EP + passivation, having a corrosion rate of only one third of the latter and significantly improving analytical flow path corrosion resistance. When used in combination, condition D delivered the best performance by at least two orders of magnitude. The overall corrosion performance in order of worst to best is A << B < C << D.
Have a question about how SilcoTek can improve the corrosion resistance of your products? Contact our Technical Service Team for a free no obligation consultation. To get the latest in advanced coatings Subscribe to get our technology updates.
To stay current with our team of scientists and technicians, follow us on LinkedIn.
