Corrosion can lead to a host of problems like expensive maintenance, component replacements, process contamination, sample probe damage and failure, and loss of productivity due to down time. SilcoTek offers several coatings designed to protect against corrosion, each with its own specific properties and applications. The best coating for corrosion resistance depends on factors such as the type of corrosive environment, temperature, pressure, and the material being protected.
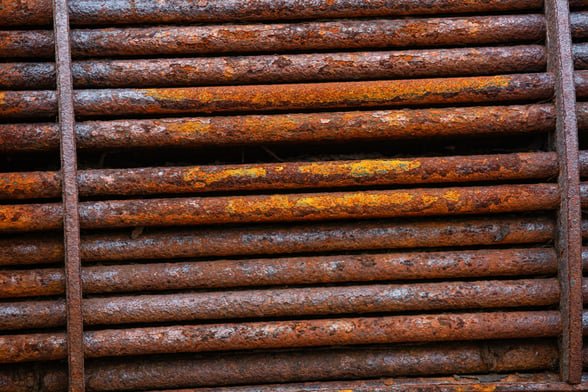
Some of SilcoTek's coatings that are commonly used for corrosion resistance include:
-
Dursan®: This coating is known for its excellent corrosion resistance in highly acidic or alkaline environments. It is often used in applications where stainless steel is not sufficiently resistant to corrosion.
- Siltride®: Siltride is SilcoTek's most versatile corrosion resistant coating that features high temperature stability and greater wear resistance when combatting corrosion.
-
Silcolloy®: Silcolloy provides corrosion resistance in many harsh chemical environments. It is particularly effective in acidic or chloride-rich conditions, plus it is our most stable offering for high temperature applications up to 800° C.
-
SilcoNert®: SilcoNert is a silicon-based coating that provides inertness and corrosion resistance, making it suitable for use in gas chromatography and other analytical instruments. Although SilcoNert coatings are designed to improve the sensitivity and performance of analytical instrumentation rather than prevent corrosion, adding this sub-micron layer of amorphous silicon will still improve stainless steel’s inherent corrosion resistance. As illustrated further below in our comparison to electropolished stainless steel, SilcoNert coatings can provide more than 100x reduction in corrosion rate.
Save Money on Replacement Equipment
Did you know that according to a study conducted by NACE International, corrosion accounts for approximately $2.5 TRILLION globally every year? They arrived at this figure in 2013, so we can imagine it's only grown since then! If you are like most of our customers who deal with corrosion, you know what a pain in the backside it can be to replace equipment due to corrosion. With SilcoTek coatings, you can extend the life of your parts with proper corrosion protection. It's a pretty simple concept, really. The less your equipment breaks or fails, the less money and time you have to spend fixing or replacing it. Check out the difference in the coated vs. control quenching sleeve from our work with Samsung Austin below! Read the full case here!
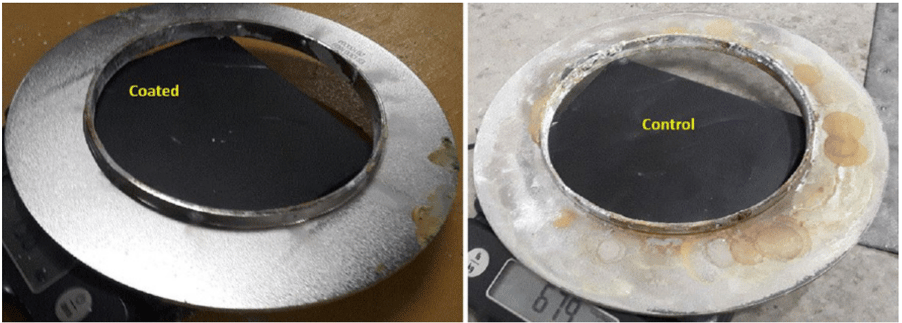
Material Selection
Selecting the right material for the job can be both difficult and expensive in a lot of corrosive applications. At the top of many of those lists are stainless steel alloys. 304 and 316L stainless steel substrates are prevalent in various industries, but the critical distinction lies in the addition of 2~3% molybdenum to the 316L family. This addition dramatically improves corrosion and oxidation resistance, particularly in environments exposed to saline or chloride-containing chemicals. See our material compatibility guide below to help you decide which material would fit best in your application.
Metal Ion Contamination Protection
What about the corrosion you can't see? Metal ion leaching is of interest to a variety of industries. Chemical exposure to solutions, such as organic solvents, deionized water, acids or bleach, can cause a significant amount of metal ions to dissolve into the liquid, causing product contamination, system corrosion, and test problems in analytical and high purity processes including semiconductor manufacturing, biopharmaceutical production, medical diagnostics, precision cleaning, food and beverage processing, and HPLC analytical flow paths.
SilcoTek offers CVD coating solutions to make your process, analytical, and sampling systems perform better. Our chemically inert coatings improve test accuracy and reliability by preventing contamination from metal ion leaching caused by chemical reactions between the sample and flow path surface. The summary below demonstrates how metal ions can be readily leached into flow path solutions and how coated surfaces (right column, green) prevent contamination under all conditions tested.
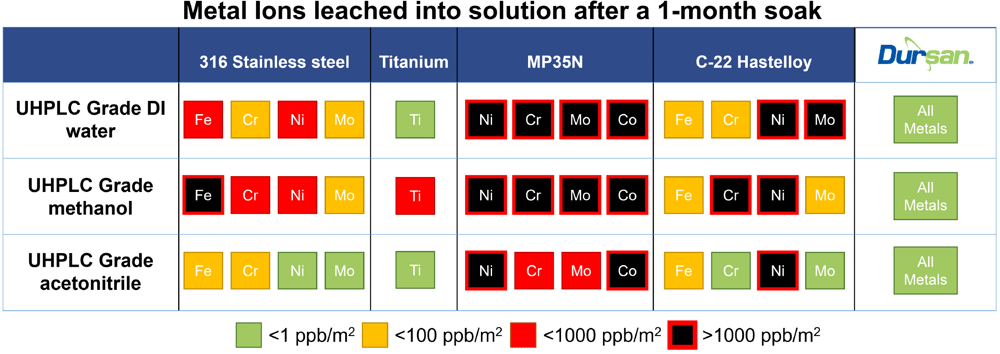
SilcoTek has conducted several studies relating to effectiveness of our CVD coatings in preventing metal ion leaching from various surfaces when exposed to organic solvents and deionized water. Read the 6 part series on metal ion leaching that includes studies on organic solvent exposure of pure methanol, ultrapure DI water, and acetonitrile on substrates such as titanium, 316L stainless steel, Hastelloy (C-22), and MP35N in comparison to our Dursan coating.
Electropolish Comparison
The coating provides excellent corrosion resistance, protecting the underlying material from degradation caused by harsh chemicals, moisture, or corrosive gases. This extends the lifespan of the components and ensures the integrity of the transfer system over time. SilcoNert 2000 provides a good corrosion barrier for 5% HCl, as shown in the chart below each coupon type:
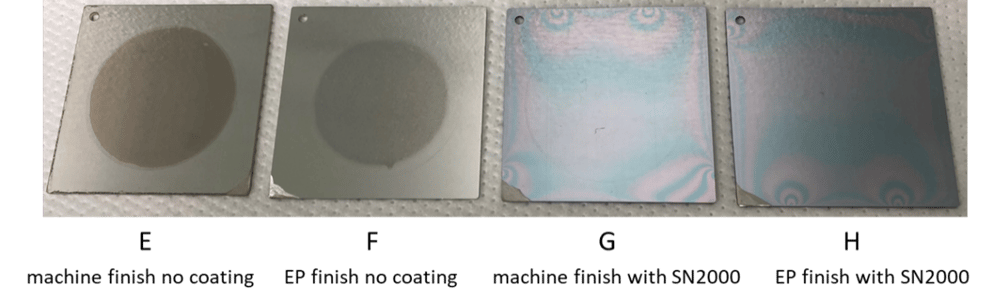

Coating stainless steel with SilcoNert 2000 shows better inertness for trace levels of H2S and MeSH, faster dry down speeds, and improved corrosion resistance when compared to an electropolished stainless steel. Many gas and fluid transfer systems could benefit from the CVD coating technology due to its superior performance, shorter lead times, and lower price when compared to electropolished tubing.
Have questions about your corrosion applications? Contact our knowledgeable coating experts today!
Follow Us on Social Media!
