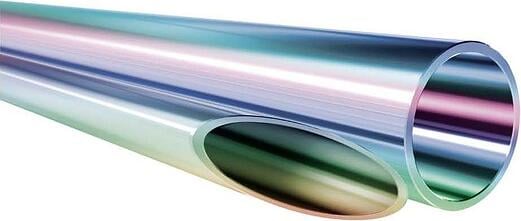
We discuss coating the internal surfaces of small bore tubing and needles. How is the coating applied? Does the coating perform? How small a bore can we coat?
Can Narrow Bore Tubing be Coated? What About Performance?
In this blog post we explore the topic of coating interior surfaces of needles, small diameter tubing, and passages. Chemical vapor deposition is the secret to applying a coating to hard to reach areas, but how does the coating perform? Let's review how we apply our coatings and discuss some relevant inertness, corrosion, and bio inertness data.
In this blog post you will learn:
- How CVD us used to apply silicon coatings to the interior of small bore tubing.
- Learn about the benefits of applying coatings like Dursan® (featured here), Silcolloy®, and SilcoNert® to precision components and hard-to-coat interior surfaces.
- Get coating performance data on inertness, corrosion resistance, and bio inertness for tubing and needles.
|
How are SilcoTek® Coatings Applied to the Interior of Needles and Small Bore Tubing?
Why is SilcoTek® able to coat small bore tubing and precision components? Because our unique chemical vapor deposition process is performed in a gas phase; consequently, the smallest channels and tightest tolerances will be coated. That's because the process gasses will diffuse into small bore tubing or can be pressure fed into the interior of tubing.
We also have the ability to coat certain tube configurations internally-only, so we can assure even long tube lengths are coated. Basically, if we can get our process gasses into the tube or expose the part surface to our process gas we're able to coat the part. For long but extremely narrow tubes we'll restrict the tube length to be sure we're able to achieve the desired coating performance. Even narrow bore needles can be coated because we're able to disperse our gases into the needle interior, assuring complete coverage of interior surfaces.

The Coating Process Details
SilcoTek's CVD coating process is able to treat 2 tubing configurations, coiled rolled tubing and straight sticks. Our chemical vapor deposition process has some limitations relating to each tubing configuration which we'll highlight below.
Tubes are coated by a process called chemical vapor deposition (CVD). The CVD process starts by preparing the tubing surface for coating by removing potential contaminants. Surfaces are optimized for the highest coating quality by cleaning the surface using proprietary methods that employ environmentally friendly cleaning solutions.
Want to learn more about effective cleaning and maintenance of process or analytical flow paths? Click on our link below to read a presentation from our coating care webinar.
After surface preparation, the tube is heated to enable the coating reaction. Then process gasses are injected either into the inner bore of the tubing (used when coating coiled tubing internally) or the process gas is injected into a reaction chamber which contains the tubing. This process is used to coat straight tubing on internal and external surfaces.
In order to reliably coat the internal tube surface, we limit the maximum straight tube or coil length as summarized below.
Coiled/Rolled Tubing 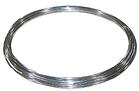
- Coated internally-only
- Maximum continuous length:
.jpg?width=355&name=Max%20coil%20length%20table%20(003).jpg)
We also have some general tube roll limitations to assure we're able to properly load tubing coils into our process ovens. We ask that coiled tubing be shipped either on metal spools or bound with metal wire to be sure we don't damage the coil while processing.
- Maximum coil OD for tubing > 1/16" OD: 36"
- Maximum coil OD for tubing 1/16" OD or smaller: 18"
- Must be shipped on a metal spool or bound with metal wire. No spools made of wood, plastic, or other flammable materials.
Have a question about coating tubing or other parts? You can discuss your application by using our chat box below. You'll be instantly connected with a coating expert who can answer all your questions. Not a fan of chat? You can email us be clicking on the box below.

Coating Straight Tubing
Because straight tubing is coated in a reaction chamber, tubing length is limited to the size of the coating reactor chamber. Our largest tubing reactor can accommodate a maximum tubing length of 80 inches (approximately 2 meters).
Coating Capabilities, Straight Tubing:
- Coated both internally and externally
- Maximum length: 80"
SilcoTek® is able to coat a range of tubing diameters from 1/16in up to diameters exceeding 6 inches. Contact our technical service team to learn more.

What About Coating Needles and Small Bores?
As we noted previously, our unique chemical vapor deposition process is performed in the gas phase, so the smallest channels and tightest tolerances will be coated, even the ID of needles can be coated. We do have some limitations on some coatings regarding minimum tube ID. Contact a Technical Service Representative to learn more.
How We Tested Our Coating in Small Tubes
We proved coating aspect ratio capabilities by coating a 1/16" OD, .4mm ID tube with multiple bends both internally and externally. After coating, the tube was cut open to examine the coating at the center-most point inside the tube. In addition to the external coating on the tube, a quick visual inspection shows the vibrant purple-colored SilcoTek coating inside the narrow bore.
The thickness of the coating throughout the tube was verified by a Filmetrics F40-Series Thin Film Analyzer and it was confirmed to meet our specifications. SilcoTek coatings are not applied with line-of-sight processes that lead to inconsistent deposition and uncoated areas. With our process, 100% of your parts are coated, even if the design is complex or the pathways or tortuous.
|
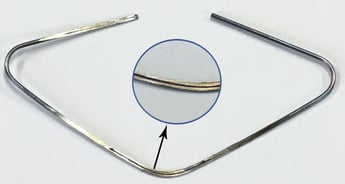
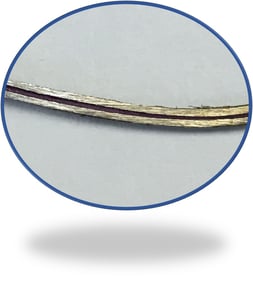
|
About Dursan and the Benefits of Coating Tubing Flow Paths
Our Dursan coating has proven benefits to analysts in medical diagnostic, HPLC, and IVD applications. The Dursan® process is a chemically inert, silicon-based coating that improves corrosion resistance and reduces protein carryover, promoting more accurate test results as well as more thorough cleaning, disinfection, and sterilization processing. Applying an inert, non reactive barrier coating to stainless steel surfaces prevents the interaction of stainless steel with potentially reactive or corrosive analyte materials.
SilcoTek® solves common problems in medical diagnostics with stainless steel flow path surfaces and probes like:
• Poor performance caused by carryover of proteins
• High cost due to corrosion, especially from bleach
• Contamination from leaching of metal ions out of equipment
• Poor analytical sensitivity for challenging samples
• Downtime caused by frequent maintenance and cleaning
Learn more about how our coatings can benefit your process or products. Read our introduction to CVD coatings.
SilcoTek’s Dursan technology has been rigorously tested to ensure proper performance and earned an NSF Certification and a USP Class VI Certification. Performance benefits of a Dursan® coated surface for invitro diagnostic applications include:
- Improve Cleaning - Dursan’s inert barrier reduces contamination and buildup of biological material, while making standard rinsing easier and more effective.
- Easy Integration - Run processes as normal while enjoying the coating benefits. SilcoTek coatings hold up to steam and conform to parts, creating no appreciable changes to tolerances or surface morphology.
- Enhance Performance - Improve diagnostic sensitivity by reducing non-specific protein binding and carryover.
- Increase Efficiency - By improving corrosion and contamination problems, cleaning will be more effective and parts will need to be replaced less often.
- Reduce Contamination - An inert barrier will prevent contamination commonly caused by the sample, the reagent, or ions leaching from probe metal.
Supporting Data
Dursan® has been tested under real world conditions and has shown consistent performance gains in inertness, contamination prevention, and corrosion resistance.
We tested Dursan on commonly used substrates including alloy MP35N and stainless steel to demonstrate how a coated part will perform under various test conditions. We found the Dursan coated surface reduced material binding, ion contamination, corrosion, and substrate adsorption when applied to common HPLC, medical diagnostic, and IVD flow paths surfaces. Let's review some of the data.
Prevent Biologics and Protein Sticking on Metal
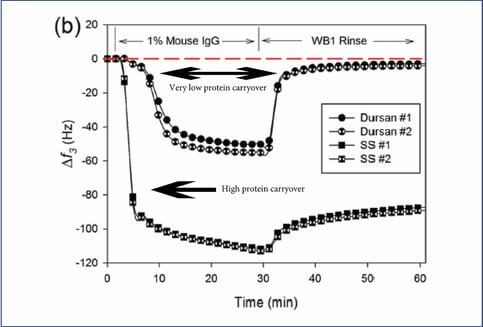
When trying to eliminate biologic material from a surface, Dursan showed a more effective reduction of protein loss than stainless steel and when combined with a washing step using a non-ionic surfactant, 100% of tested proteins were removed.

Reduce Metal Ion Leaching and Contamination
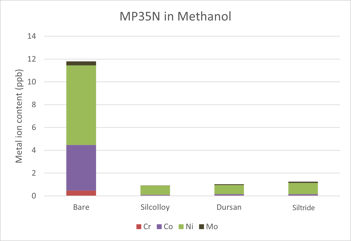
SilcoTek measured metal ions leaching in methanol after a month of soaking to compare MP35N and SilcoTek coatings performance. Coated samples all showed less than 1 ppb metal ion content leached into the methanol, while MP35N measured significantly worse at roughly 12 ppb of metal ions.

Prevent Bleach Corrosion and Variability
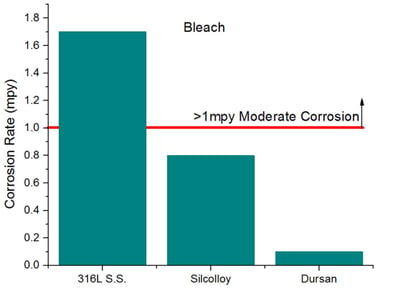
ASTM G31 72 hour comparative bleach immersion studies prove that Dursan significantly reduces the risk of corrosion in diagnostic probes, thus reducing any variability.

Ensure Sensitive, Fast and Accurate Analysis
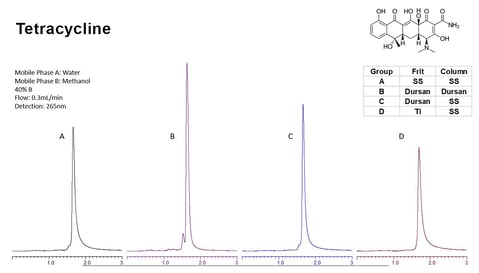
These chromatograms show Dursan-coated hardware outperforming stainless steel and titanium while measuring a tricky, chelating agent. In image B, the analysis is more sensitive and accurate while maintaining a faster response.

Performance After Steam Sterilization
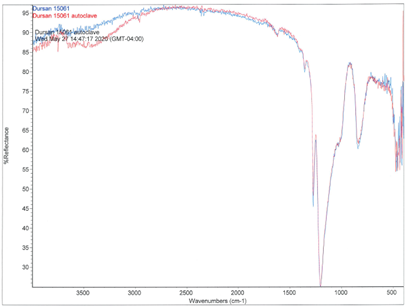
FTIR analysis shows there was little significant change in material composition observable before (blue line) and after the autoclave exposure (red line) for the Dursan surface. A slight increase in Si-OH functional groups accounts for ~10° decrease in DI water contact angle.
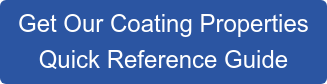
The data show that SilcoTek® is able to effectively coat the internal surfaces of small bore tubing and intricate parts. Additionally studies show that Dursan® coated surface help to prevent carryover, contamination, and surface corrosion while improving test resolution. We offer many other coatings designed to improve the performance of your products and process. If our standard coatings don't fit your material performance needs, our technology group can tailor fit a coating for your application.
SilcoTek specializes in customizing our coatings for your application. Instrument manufacturers only have to contact our Technical Service Team and discuss your performance needs. Our staff will evaluate your needs and determine the best coating fit for your application.
Want to keep up with the latest in coating technology? Subscribe to our blog or follow us on LinkedIn.
