In a case that is local to SilcoTek, forty-one students at the North Star School District and Somerset County Technology Center in Somerset County, PA mysteriously fell sick in April of this year. When emergency personnel responded, it was found that many of these students were testing positive for carbon monoxide poisoning. Of course, the school district and the public wanted to know how this happened, so they went to work in search of a cause. Experts were brought in to sample the air quality in both buildings. Administrators were puzzled when initial and subsequent testing did not indicate elevated levels of carbon monoxide or carbon dioxide in the buildings. In the news reports, SilcoTek-coated products can be seen in use when investigators were measuring air quality within the school. Let's talk about how our coatings helped in this case.
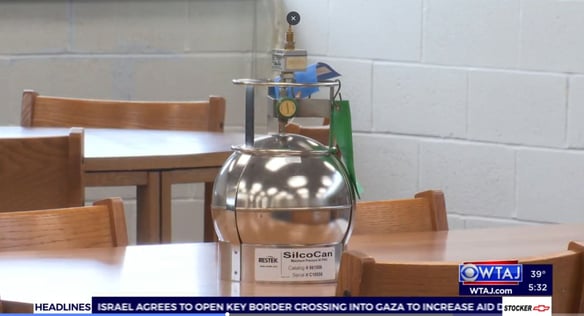
SilcoTek coated Restek SilcoCan, shown in the WTAJ coverage of this case.
What is Carbon Monoxide?
As defined by the Environmental Protection Agency (EPA), carbon monoxide (CO) is a colorless, practically odorless, and tasteless toxic gas or liquid that is the product of incomplete oxidation of carbon in combustion. The most common sources of CO are machinery that burn fossil fuels, particularly water heaters, furnaces or boilers, fireplaces, or gas stoves/ovens. Other sources include wildfires, vehicle emissions, barbeque grills, gas lanterns and outdoor heaters, and portable generators.
Here's your helpful tip for the day: make sure you double check that your carbon monoxide alarms are functioning properly! It could save you or a loved one's life!
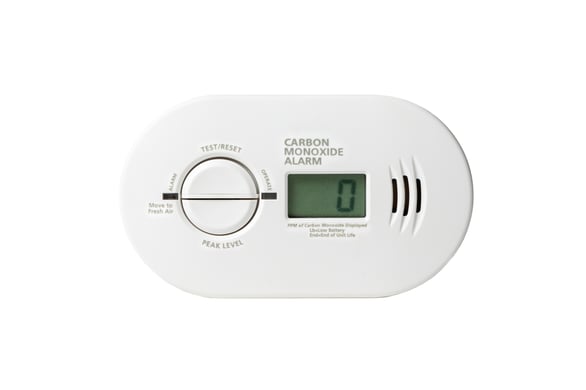
Why is Carbon Monoxide Harmful to Humans?
Exposure to carbon monoxide is detrimental to humans because it hinders the body's ability to carry oxygen to body tissues and vital organs. When inhaled, CO will combine with hemoglobin, producing carboxyhemoglobin (COHb). Hemoglobin is an iron-protein component of red blood cells, which carry oxygen throughout the body. According to the National Institutes of Health, hemoglobin combines with CO 220 times faster than it does with oxygen, making this an extremely dangerous combination.
Common symptoms of carbon monoxide poisoning include headache, nausea, confusion, dizziness, weakness, exhaustion, impaired vision, and rapid breathing. Prolonged exposure can lead to irreversible neurological problems, brain damage, heart damage, or death.
The most important treatment for CO poisoning is access to 100% oxygen as quickly as possible. In very serious cases, hyperbaric oxygen therapy (HBOT) should also be considered. HBOT is not confirmed to be helpful in all CO poisoning cases, but could prove to be important for those who are pregnant, unconscious, have a very high COHb concentration, or are experiencing cardiac problems.
Challenges of CO Sampling and Analysis
Carbon monoxide gas streams can cause corrosion and contamination of sensitive processes, like catalysts and semiconductor fabs, when exposed to metals that readily form oxides. The resulting corrosion formation is called a carbonyl group. Carbonyl groups are formed when the CO reacts with the metal surface to oxidize and corrode the surface. A typical formation reaction may look something like the aluminum/CO exposure reaction below:*
2Al(s) + 3CO(g) → Al2O3(s) + 3C(s)
Carbonyl formation can result from exposure to various metals like iron, nickel, cobalt, molybdenum, stainless steel, or aluminum. **
Examples of carbonyl formation are:
-
-
- Iron pentacarbonyl: Fe(CO)5
- Nickel tetracarbonyl: Ni(CO)4
- Chromium Hexacarbonyl: Cr(CO)6
- Tungsten hexacarbonyl: W(CO)6
- Molybdenum hexacarbonyl: Mo(CO)6
Carbonyl groups can be formed at relatively low temperatures, 200-300°C. Iron and nickel containing alloys in particular can be problematic. Those metals and alloys containing those metals can form carbonyl groups under high pressure at ambient temperature. Consequently, steel and stainless steel high pressure cylinders containing carbon monoxide are susceptible to carbonyl corrosion and contamination. This can shorten the life of high pressure cylinders and high pressure flow path components and can result in product contamination.
With sensitive applications like human health, it would be ideal to prevent corrosion or contamination before it occurs. Preventative measures against carbonyl corrosion and contamination have just a few options:
- Removing CO from the gas stream (not an option for users that need the CO as part of their process).
- Changing the material to those not susceptible to CO corrosion. Materials like brass won't form carbonyls, but brass is difficult to work with (soft) and is not durable. Plastic or glass lined products have their own durability issues.
- Apply barrier coatings designed to prevent surface interaction of the CO gas stream with the flow path material. Our corrosion resistant silicon coatings, like Dursan® and Silcolloy®, inhibit carbonyl formation.
Click below to see more about how SilcoTek's barrier coatings can help with even the most sensitive applications.
Advantage of SilcoTek Coatings vs. PFAS
Speaking of human health and air quality, per- and polyfluoroalkyl substances (PFAS) are a hot topic today. These “forever chemicals” don’t break down naturally in the environment and have been linked to birth defects and other human health issues, so government agencies around the world are starting to introduce regulations to reduce and eliminate the use of PFAS in both consumer and industrial applications. PFA is a popular example of a PFAS due to its remarkable chemical resistance, which is imparted primarily by the fluorinated or “forever chemical” component of this material. PFA is used in a variety of industrial and scientific applications, including for analyzing air samples like we describe above.
The study summarized in the table below exposed various tube surfaces to methanol at 50°C and 100°C and measured adsorption rate of the surfaces. Results show that an inert coating like SilcoNert coated stainless steel prevented adsorption and reaction with VOCs in critical flow paths.*
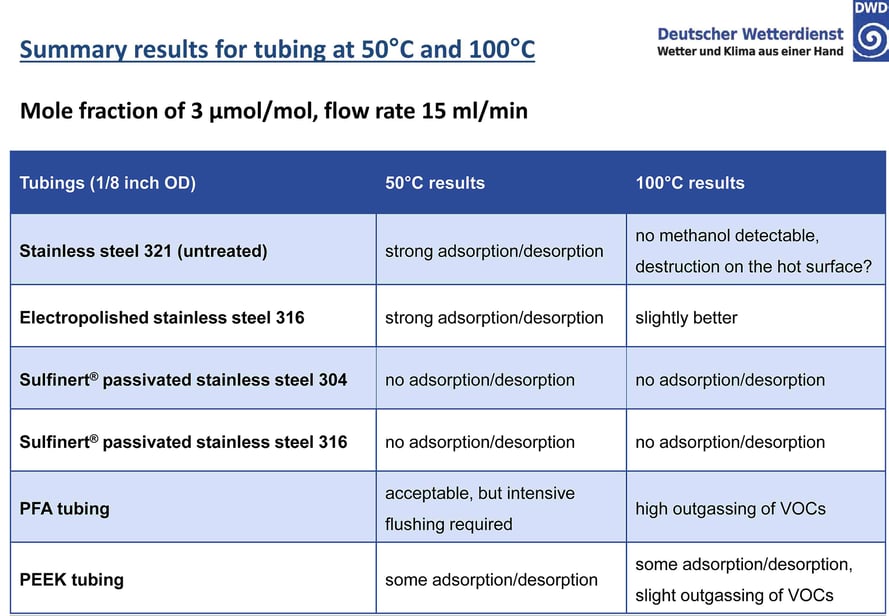
Untreated and even electropolished stainless steel, unsurprisingly, show significant adsorption of target compounds of interest. PFA requires careful management and intensive maintenance to achieve desired results, plus it is not stable at elevated temperatures – notice how the study reports high outgassing of volatile organic compounds (VOCs).
SilcoNert-coated stainless steel does not adsorb active compounds because the inert silicon CVD surface bonds to and diffuses into the stainless steel substrate, preventing interaction with reactive sites. The sputter depth profile (below) characterizes the diffusion zone of a typical SilcoTek CVD coating.
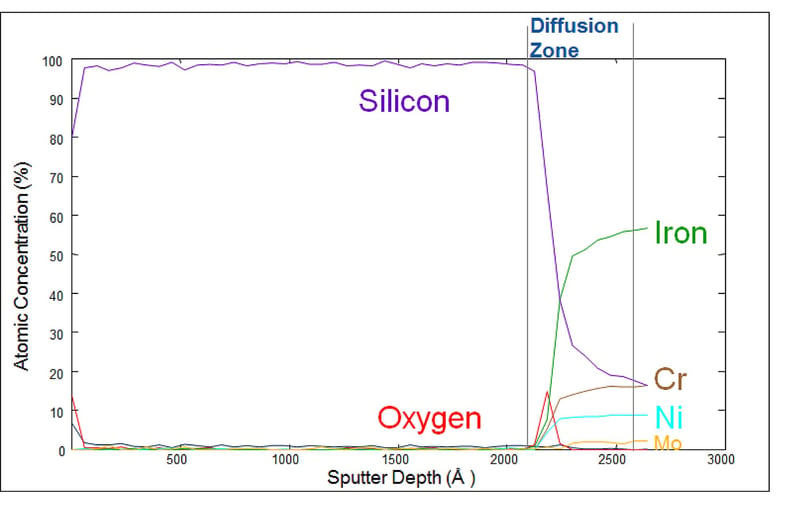
The Key Factor in VOC Analysis? An Inert Flow Path
Be sure to coat the entire flow path to prevent selective adsorption by reactive surfaces. Not coating a fitting or fritted filter can significantly impact analytical results and can cause calibration failures, increased system maintenance, false positive/negative results, frequent retesting, and potential regulatory compliance issues.
Coated flow path surfaces include:
- Whole air sampling canisters
- Regulators & mass flow control
- Valves
- Fittings
- Tubing
- Liners (yes we can coat glass)
- Fritted filters
- Sample cylinders
- GC, FTIR, and instrument components
Have questions about how SilcoTek's coating on analytical instruments can help your applications? Contact our coating experts!
* Images and data courtesy of The Dutch Metrology Institute (VSL) and the German Meteorological Office (DWD) presented at the Key VOC joint project April 21st 2016, in Paris, France.