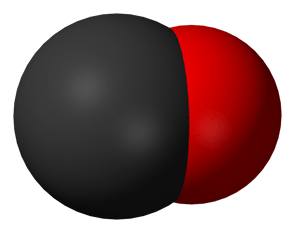
In this blog post we'll discuss how Dursan® and Silcolloy® can be used to inhibit carbonyl formation in carbon monoxide gas streams.
Inhibiting Carbonyl Formation in Carbon Monoxide Gas Streams
In this blog post you will learn:
- How carbon monoxide gas streams can react with steel surfaces to form carbonyl corrosion.
- How silicon barrier coatings, like Dursan® and Silcolloy®, can prevent surface exposure to CO, preventing corrosion
- Impact of carbon monoxide (CO) corrosion in industry.
|
Background
Carbon monoxide (CO) gas streams can cause corrosion and contamination of sensitive processes, like catalysts and semiconductor fabs, when exposed to metals that readily form oxides The resulting corrosion formation is called a carbonyl group. Carbonyl groups are formed when the CO reacts with the metal surface to oxidize and corrode the surface. A typical formation reaction may look something like the aluminum/CO exposure reaction below:*
2Al(s) + 3CO(g) → Al2O3(s) + 3C(s)
Carbonyl formation can result from exposure to various metals like iron, nickel, cobalt, molybdenum, stainless steel, or aluminum. **
Examples of carbonyl formation are:
-
-
- Iron pentacarbonyl: Fe(CO)5
- Nickel tetracarbonyl: Ni(CO)4
- Chromium Hexacarbonyl: Cr(CO)6
- Tungsten hexacarbonyl: W(CO)6
- Molybdenum hexacarbonyl: Mo(CO)6
Carbonyl groups can be formed at relatively low temperatures, 200-300°C. Iron and nickel containing alloys in particular can be problematic. Those metals and alloys containing those metals can form carbonyl groups under high pressure at ambient temperature. Consequently, steel and stainless steel high pressure cylinders containing carbon monoxide are susceptible to carbonyl corrosion and contamination. This can shorten the life of high pressure cylinders and high pressure flow path components and can result in product contamination.

Effects of Carbon Monoxide Corrosion and Carbonyl Contamination
Carbonyl contamination can have detrimental effects (contamination) on catalysts used in hydrogen production and oil refining processes. Other processes sensitive to metal ion contamination, like research facilities, or semiconductor wafer fabrication processes can sustain critical damage due to low product yield or lose valuable data due to poor analytical results.
In oil refining operations the carbonyl related corrosion can poison catalysts and increase corrosion related maintenance. In synthetic gas production or hydrogen production, CO contamination and resulting carbonyl group formation can lead to further degradation of the catalyst, resulting in more frequent catalyst replacement and higher cost.
In calibration gas or high purity gas systems exposed to CO, the resulting oxidation and corrosion can contaminate gas systems and damage system components including:
- High pressure cylinders
- Cylinder valves
- Isolation valves
- Tubing
- Metal filters
- Orifice fittings
- Fittings
- Mass flow controllers and flow devices
- Regulators
- System probes
|
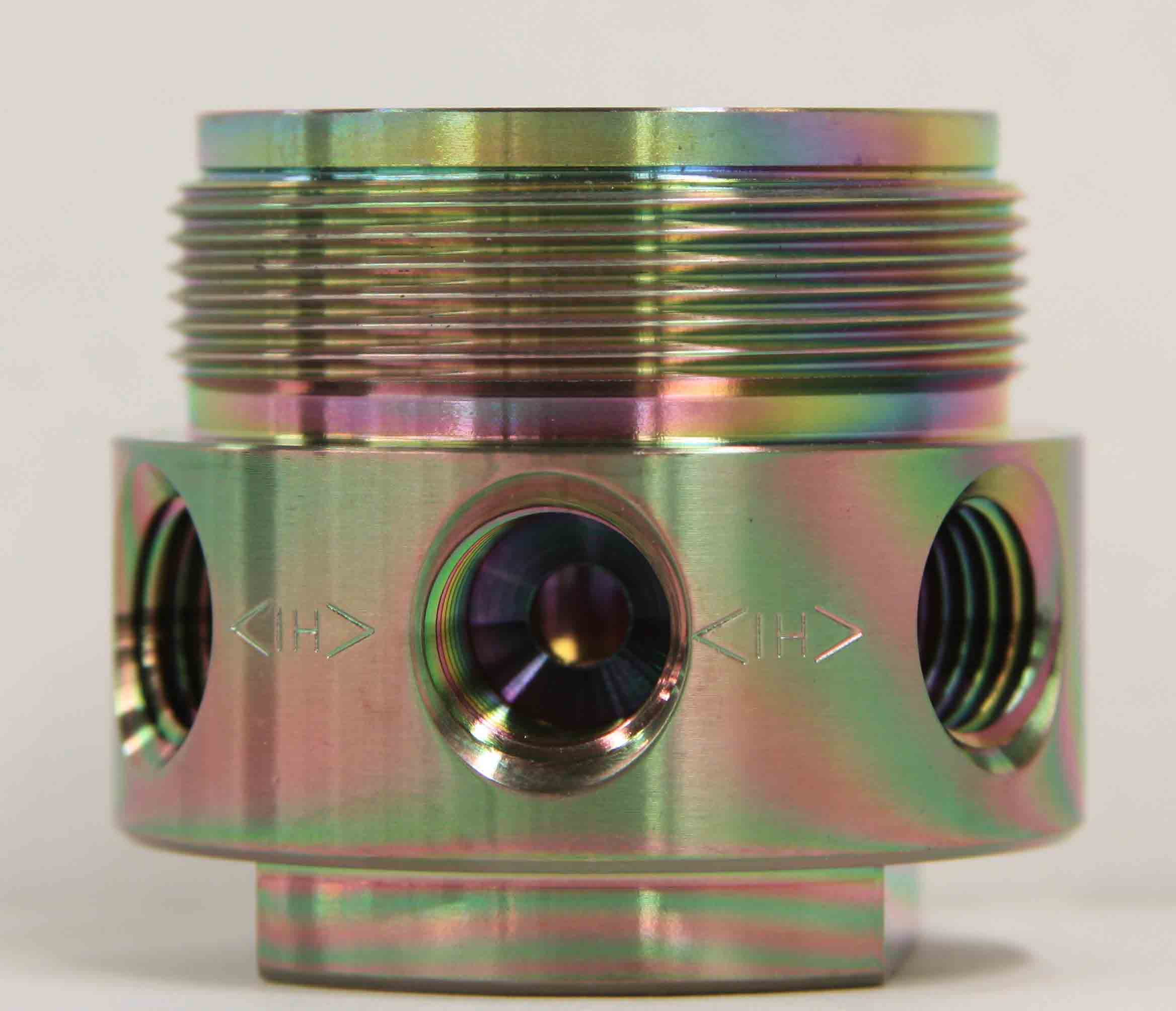 |
Options to Prevent Carbon Monoxide Corrosion
Users concerned about carbonyl formation have limited options to prevent contamination and corrosion. Prevention options range from:
- Removing CO from the gas stream (not an option for users that need the CO as part of their process).
- Changing the material to those not susceptible to CO corrosion. Materials like brass won't form carbonyls but brass is difficult to work with (soft) and is not durable. Plastic or glass lined products have their own durability issues.
- Apply barrier coatings designed to prevent surface interaction of the CO gas stream with the flow path material. Our corrosion resistant silicon coatings, like Dursan® and Silcolloy®, inhibit carbonyl formation.
Read more about using our coatings in challenging sampling and process environments. Read our e-book.

High Temperature Corrosion Resistant Coatings Performance
Dursan® and Silcolloy® are silicon barrier coatings applied by chemical vapor deposition to stainless steel, aluminum, and other metal alloy surfaces. Silicon is non-reactive and resists the interaction of carbon monoxide and many other process gases and liquids. A recent US patent (CYLINDER VALVES AND METHODS FOR INHIBITING THE FORMATION OF CONTAMINANTS IN CYLNDERS AND CYLINDER VALVES) highlights the use of Dursan and Silcolloy in cylinder gas valves and high pressure gas cylinders, specifically for the prevention of carbonyl corrosion and contamination.
SilcoTek® coatings, like Dursan and Silcolloy improve corrosion resistance by orders of magnitude. Laboratory corrosion tests prove that silicon coatings are an effective barrier to gas and liquid exposure, especially in systems where high purity is required.
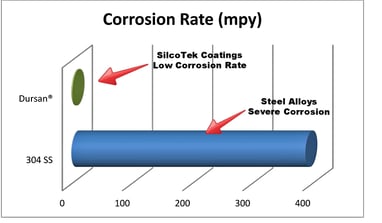
Additional Reading
If you'd like to learn more about corrosion and contamination, SilcoTek® offers a wealth of information found in our website Learning Center.
https://energyeducation.ca/encyclopedia/Carbon_monoxide
https://onepetro.org/NACECORR/proceedings-abstract/CORR98/All-CORR98/NACE-98407/127847
https://www.osti.gov/servlets/purl/5000553
To stay in touch with the latest in coatings and coating science, subscribe to our email and blog, or follow us on LinkedIn.

*Corrosion Control, second edition, Samuel A. Bradford, Ph.D.;P. Eng. CASTI Publishing Inc., ASTM International.
**Image Credit, wikipedia.org, https://en.wikipedia.org/wiki/Iron_pentacarbonyl