SilcoTek will be attending the Advanced Semiconductor Manufacturing Conference (ASMC) in Saratoga, NY on May 1-4. Look for these smiling faces to discuss how SilcoTek coatings can help in your semiconductor applications!
Meet With Us at ASMC 2023!
You can find Nik Snyder (left) and Jim Mattzela (right) at the Saratoga Hilton in Saratoga Springs, NY from May 1st to May 4th at ASMC. If you would like to schedule some time with our experts at the conference, we would love to hear from you. Contact us at Marketing@SilcoTek.com, or reach out to Jim or Nik.
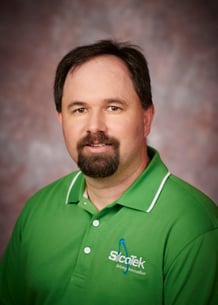
About ASMC
ASMC is the leading international technical conference for discussing solutions that improve the collective manufacturing expertise of the semiconductor industry. Solving the challenges presented by semiconductor manufacturing is a combined effort by device makers, equipment and materials suppliers, and academics. ASMC provides an unparalleled platform for semiconductor professionals to network and learn the latest in the practical application of advanced manufacturing strategies and methodologies. *
Who Should Attend:
- Academia
- Chief Technology Officers
- Fab Managers
- Equipment Manufacturers
- IC Manufacturers
- Materials Suppliers
- Operations Managers
- Process Engineers
- Product Managers
- Technical Experts
SilcoTek® Worked with Samsung to Improve Gas Abatement Systems
Last year, SilcoTek partnered with Samsung to improve their gas abatement systems (exhaust scrubbers). This is just one example of how SilcoTek coatings can improve semiconductor manufacturing applications, effectively causing reduced down time, fewer equipment failures, increased yield, and more reliable results, among others.
Game-Changing Benefits
The semiconductor manufacturing experts at SilcoTek knew that the new Siltride® coating technology could be a game-changing solution for Samsung’s corrosion problem. The silicon nitride composition creates an excellent barrier against the highly corrosive environment of a scrubber system. Samsung and SilcoTek partnered together to test and evaluate the performance against Samsung’s control quenching sleeves and distributors, and after only a few months determined the success of the Siltride coating technology.
A high-temperature application in a corrosive environment creates a perfect recipe for destroying machines, leading to inefficient production and compromising quality. The results below show just how game-changing the Siltride coating technology was for these scrubbers.
The images in Figure 1 (below) were taken after the parts had been in use for 42 days. Corrosion and degradation is evident all over the uncoated quenching sleeve, whereas the coated component shows only some minor stains. Additionally, the Siltride-coated parts measures with no mass loss and the control (uncoated) lost 10% of its mass after 42 days in operation.
Figure 2 (below) references continued on-site monitoring of the quenching sleeves after 70 days of operation. Siltride maintains its stellar results and shows no mass loss while the uncoated control part has lost 18% of its initial mass. This performance allows Samsung to operate at the highest level without worrying about contamination or stopping production to replace corroded parts.
SilcoTek’s Siltride coating process is the best way to keep your facility running at maximum efficiency, preventing down time, and ultimately saving manufactures from continuing to purchase costly replacements. For a detailed comparison of the Siltride vs uncoated control quenching sleeve, see below.
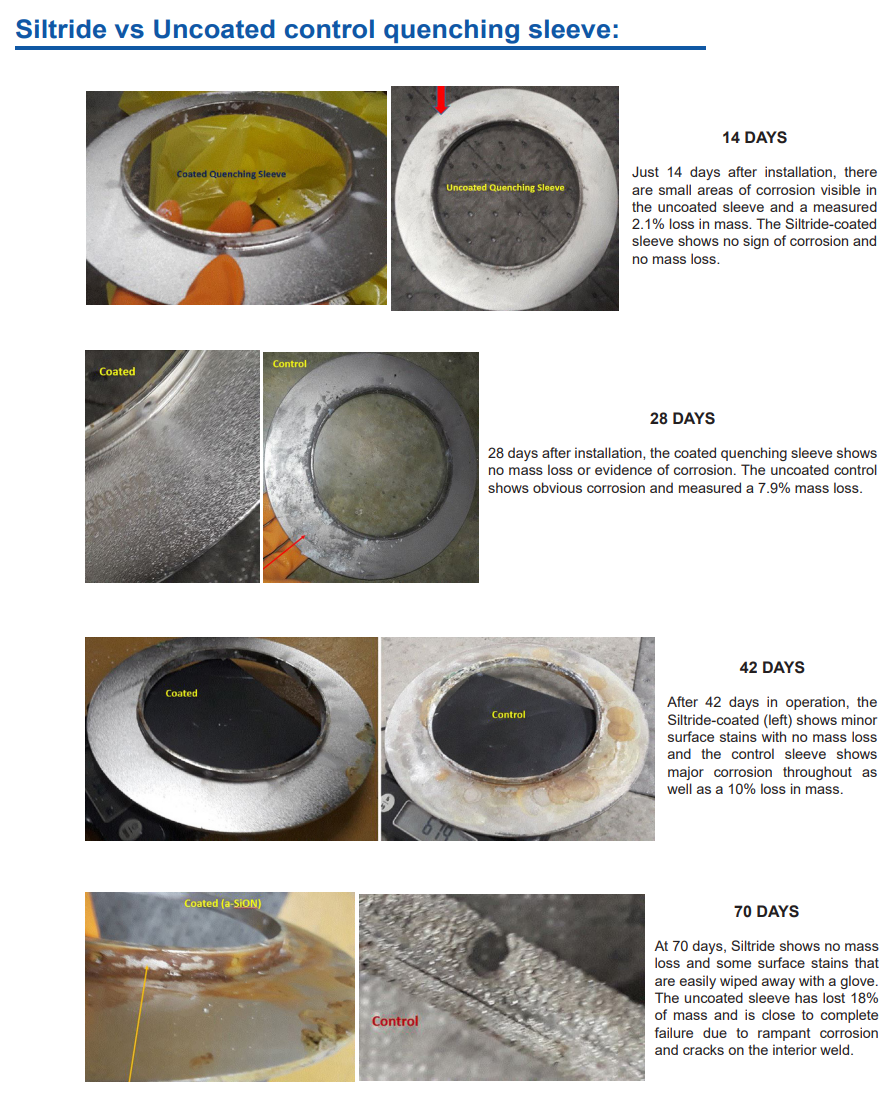
To read the entire Samsung case study or save a copy, please click the link below.

SilcoTek Coatings Can Help With:
- Improved corrosion resistance with less process contamination
- Low outgassing for improved vacuum pump down
- Less metal ion contamination and particulate generation, less fluid contamination for improved yield
- Improved durability and reliability for longer component life
- Consistent performance for improved regulatory compliance
Benefits of SilcoTek Coatings in Device Fabrication
- Solve corrosion contamination issues for semiconductor OEMs and Fabs beginning around the 22nm node.
- Remove metal ion contamination in semiconductor device fabrication.
- Reduce the cost of equipment oenership for the largest semiconductor Fabs in the world.
Customizing CVD Coatings for Semiconductor Manufacturing
Depending on our customers specific needs we can tailor the coating to achieve the properties that they are looking for. Coatings consist of a Base Layer and a Surface Layer. Amorphous, hydrogenated silicon can be used as a barrier coating for gas delivery in both etch and deposition environments.
If you would like to discuss our work with Samsung or learn about our CVD coating process, we look forward to speaking with you at the ASMC next week. If you won’t be in attendance, you can always reach our team at techservice@silcotek.com or click the button below.
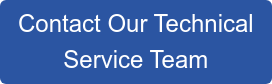
* Excerpt taken from https://www.semi.org/en/connect/events/advanced-semiconductor-manufacturing-conference-asmc