A recent paper presented at ASMC highlights how SilcoTek coatings can improve the corrosion resistance and lifetime of exhaust scrubber systems.
Improved Corrosion Resistance in Exhaust Scrubber Systems
Exhaust systems, gas abatement systems, and exhaust scrubbers can be exposed to a variety of corrosive and toxic substances. Even the most durable systems can suffer from corrosion, and may require costly maintenance or replacement, and may require frequent outages for repair. SilcoTek teamed up with Samsung to find a solution to their exhaust scrubber problem. The result? A significant reduction in several key system issues including:
- Improved corrosion resistance.
- Less scrap.
- Less metal contamination in their waste stream.
- Less employee exposure to potentially toxic exhaust scrubber environment.
- Less maintenance and component replacement.
- More uptime for the system.
- Lower overall cost of operation.
In this blog post we'll discuss a recent paper presented by Samsung at the Advanced Semiconductor Manufacturing Conference (ASMC) 2022 in Saratoga, NY.*
In this blog post you will learn:
- How to improve corrosion resistance of metal components used in scrubber exhaust systems.
- How to increase system uptime and reduce maintenance cost.
- Get corrosion resistance data and learn how SilcoTek® coatings can extend the life of scrubber and exhaust system components.
|
Background
The paper presented at ASMC discusses how Samsung improved the performance of their exhaust scrubber system. The discussion centers around a scrubber application in a semiconductor fabrication unit in Texas, but the underlying improvement in corrosion resistance has applications in a wide variety of exhaust systems where corrosion is a significant issue.

Ongoing shifts in semiconductor fabrication methods are resulting in processes and materials that can release toxic chemicals like silane (SiH4) and phosphine (PH3) into the waste stream. These effluents are removed (scrubbed) by a hybrid of wet and dry point-of-use systems. Most of the chemicals used in the semiconductor fabrication process (70% or more) will end up as waste that is vented to an exhaust scrubber system. A typical hybrid scrubber system will look something like the illustration below.**
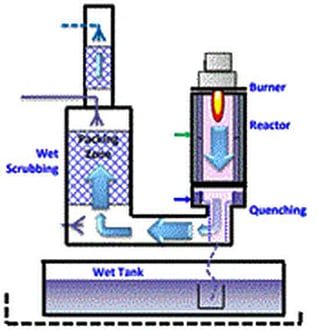
These systems are installed close to the manufacturing process in order to provide the most flexibility in effluent mitigation and to allow better point source monitoring. Consequently, the facility operated several scrubbers. Due to the challenging corrosive environment within the scrubber. Some key exhaust systems components were frequently corroding. This led to frequent line shut downs and high replacement/maintenance cost. The facility used various corrosion resistant alloys to extend the life of key components with limited success.
Unfortunately even nickel and chromium alloys like Inconel can experience severe corrosion in these systems. The systems can experience both dry and wet effluent exposure with high temperatures. This aggressive environment results in degradation of the exposed system parts and often can lead to an increase in heavy metal emissions in the waste stream. This can further complicate disposal of the solid waste. As the exposed scrubber parts corrode their structural integrity is degraded, causing failure and scrubber performance issues.
Corrosion in the exhaust stream can:
- Increase system maintenance
- Cause frequent system outages
- Complicate effluent disposal
- Degrade scrubber efficiency
- Expose workers to hazardous materials
Samsung worked with SilcoTek® to find a solution. SilcoTek's technical staff recommended 2 coating options which were evaluated. Samsung then wrote a paper with SilcoTek which was presented at ASMC.

Results
The paper shows a significant improvement in corrosion resistance and part longevity. The images below show SilcoTek coatings outperformed the uncoated alloy parts by a wide margin. The upper left photo shows a new quench sleeve. After 252 days of exposure, the coated quench sleeve (lower left) exhibits some surface rust but remains structurally viable. The uncoated quench sleeve was replaced after only 126 days. In fact 3 uncoated quench sleeves were installed (2 failed and one in use) during the same test period where only one coated sleeve was used.**
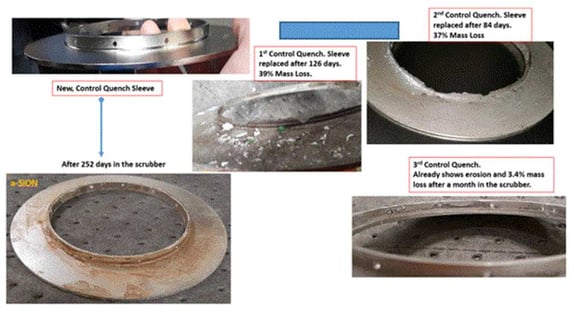
The reactor section of the scrubber (below) shows a similar result. After the test period, the corrosion zone of the SilcoTek coated reactor (top left and center images) shows some surface corrosion on the weld and flange section but remains structurally sound. The uncoated reactor body showed significant structural damage. The second uncoated control (bottom right) lost the entire flange section of the part due to severe corrosion.**
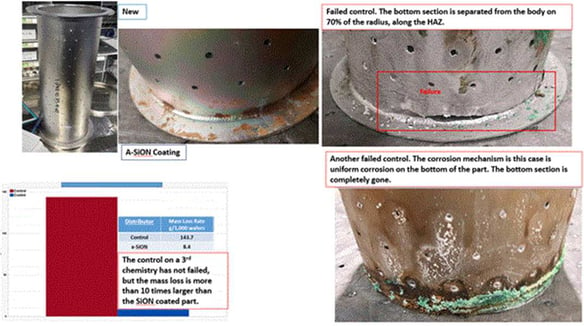
The mass loss graph below shows that 3 parts (red line) failed during the test period with over 40% mass loss, while the silicon coated part (blue line) remained structurally sound with less than 2% mass loss.**
Learn more about the study and get more information about the mechanism of corrosion in the test and how it relates to stress corrosion cracking, click the button below to read the report.

How SilcoTek® Coatings Perform in Other Corrosion Applications
SilcoTek coatings improve the corrosion resistance in a wide variety of corrosion resistance applications. Applications include:
- Analytical flow paths in GC and HPLC instrumentation.
- Canisters used in semiconductor fabs.
- Extrusion components used in plastics manufacturing.
- Sample flow paths and sample cylinders used in oil and gas extraction and hydrocarbon processing.
- Components used in renewable energy applications.
- Nozzles and components used in aerospace applications.
- Industrial exhaust systems and flare systems.
Want to meet with us to discuss your application? See us at one of several upcoming tradeshows. We'll be at Semicon West July 11-14th to discuss how we improve corrosion resistance and surface inertness.
ASTM immersion testing proves SilcoTek® coated stainless steel enhances corrosion resistance by orders of magnitude, matching the performance of super alloys in many applications. Even after immersion in concentrated hydrochloric acid (below) the Dursan® and Silcolloy® coated stainless steel coupons continue to perform with minimal corrosion, demonstrating performance comparable to super alloys.
/astm%20g31.png?t=1570811309696&width=419&name=astm%20g31.png)
SilcoTek® coatings perform in a variety of corrosive environments including sulfuric acid and bleach.
Comparative Corrosion Summary |
|
|
|
Stainless Steel Corrosion Rate (mpy) |
Dursan Coated Stainless Steel (mpy) |
6M Hydrochloric Acid, 24 hr exposure |
160 |
1 |
25% Sulfuric Acid, 24 hr exposure |
55 |
5 |
52 Week Salt Spray |
<0.01 |
<0.01 |
Bleach |
1.7 |
0.1 |
Learn more about how SilcoTek coatings can improve the corrosion resistance of your process, exhaust system, or gas abatement system. Go to our Applications page, follow us on LinkedIn, or subscribe to our blog.

*Specialty Coatings to Reduce Corrosion in Scrubber Components, Advanced Equipment Process and Materials; César M Garza and Cole Mann, Samsung Austin Semiconductor, LLC w.mann@samsung.com; Min Yuan, James Mattzela, Nik Snyder, SilcoTek Corp. nik.snyder@silcotek.com
**Image credit Samsung