One of SilcoTek's most important strategic directives is to coat every part perfectly and on time, every day. This week, we wanted to discuss our receiving process and what happens to your parts once they are received at SilcoTek. We have a few tips that will help your order to move smoothly through the coating process.
SilcoTek's Tips for Sending Parts and Getting Them Into Process Quickly
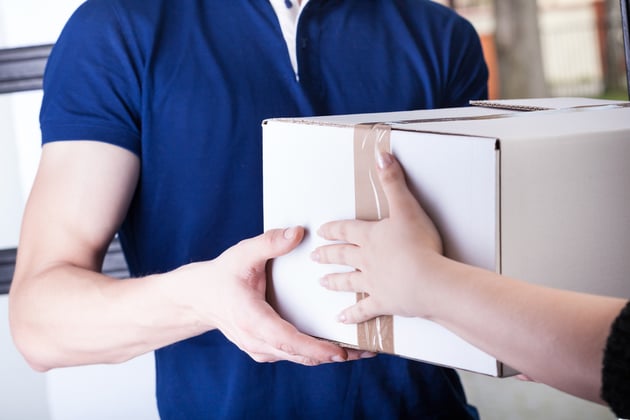
When we get your parts in house, we thoroughly inspect them and marry them up with an order in our system. We then generate the order number that will be used to track your parts throughout the coating process. We asked our receiving team what they see the most from incoming customer packages and any suggestions they have for helping our customers to get the best experience from doing business with SilcoTek. They were eager to share their thoughts.
Having Your Order Set up Beforehand
Best practices for sending your parts to SilcoTek for coating would be to contact us prior to shipping your parts. The quickest way to get your parts into our coating process is to have the order set up and ready to go as soon as your package hits our dock.
Incoming Paperwork
Going hand in hand with having the order set up beforehand, including the shipping documents with your package is very important. We use that to identify your order at receipt. By including the information, we're able to put your order directly into the process.
Package for Success
By using sufficient packaging, you're able to protect your parts in transit to SilcoTek. We will inform you of damaged packaging upon receipt at SilcoTek. Part to part contact is one of the biggest causes of damage that we've seen on incoming parts. To ensure that your parts will be safe, please properly package them. You can never be too safe when packaging valuable parts.
Importance of Cosmetics
Some customers are the end user and cosmetics aren't necessarily a priority, but for others it's very important. If you are selling your items, or definitely need them to be pristine, please give us a heads up and we will do our best to handle with extra care. We handle all orders with care, but some need extra care! If you have parts that you are aware of surface imperfections, please let us know so we don't stop your order to ask you about it. This saves valuable time in our process.
Damaged Items
We know sometimes damage can't be avoided. Our receiving technicians are trained to look closely for damage prior to entering parts into the process. Whether that's damage in transit, during machining, or when used items are in use, we know it can't always be avoided. If you know about any damage before you send us your parts, please inform us so we don't stop our process to ask if you'd like us to continue with the damaged parts. This can often add a day or more to process times by waiting for customer responses.
Critical Surfaces
If possible, including a drawing of your part identifying the critical surfaces, or letting us know before would be very helpful. Much like the importance of cosmetics, critical surfaces will determine how your parts are processed.
Unprocessed Parts
If there are parts that we're not coating, please omit them from the package if you can help it. We often receive nuts and ferrules with customer parts, which can be a time consuming task for our receiving staff to remove and could incur additional processing charges for our customers. By removing these prior to shipping your parts, you'll be saving precious processing time, and possibly some money. We do understand that there will be times that you need to include them and that's perfectly fine.
Correct Counts
We count every item that comes through our dock, so ensuring that you're sending the correct quantities of parts will help us to push your parts into production quickly. Sometimes miscounts do happen, and we understand that. If the quantity you're sending has changed since you received your quote, please let us know so we can update the quote and it won't be a surprise when we receive the parts.
All of these tips can help us to help you. We know that many times, problems can't be avoided and are often out of our control. When these situations arise, rest assured that our trained receiving technicians will help to clear up any questions before parts are moved into the coating process. Providing essential information prior to receipt at SilcoTek will just speed up our process and in return, you'll get your parts back faster.
If you have any questions about any of our coatings or our incoming inspection process, please reach out to us!
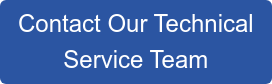