Figure 1 - Representative surface of coupon prior to coating.
In the world of materials and surface engineering, achieving optimal performance and durability is a never-ending pursuit. Fortunately, advancements in surface treatment technologies have paved the way for groundbreaking solutions. In this blog post, we will delve into the realm of SilcoTek® coatings and their synergy with surface roughness. Discover how these two factors can work in harmony to elevate material performance across various industries.
Surface Roughness
Surface roughness refers to the irregularities and deviations present on the surface of a material. It is typically characterized by the variation in height between the highest peak and the lowest valley on the surface. Roughness can be measured and quantified using different parameters, such as Ra (arithmetical average roughness), Rz (maximum height of the roughness profile), Rq (root mean square roughness), etc. Surface roughness plays a crucial role in various applications and industries, including manufacturing, engineering, and science. It can impact the functionality, performance, and aesthetics of components. For example, in precision engineering, a smooth surface with low roughness is often desirable to reduce friction, wear, and improve the accuracy of mechanical parts.
SilcoTek CVD Coatings
SilcoTek is a company that specializes in providing high-performance coatings for a wide range of materials and applications. Our coatings are applied via chemical vapor deposition (CVD) process and are known for their ability to transform the surface properties of materials. SilcoTek coatings are often used to modify the surface characteristics of various substrates, including metals, glass, and ceramics.
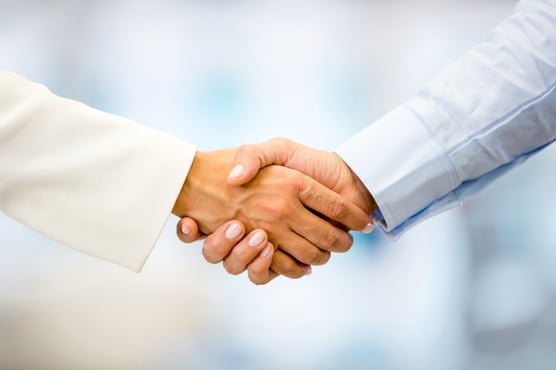
How Can We Use Them Together?
Discover the power of combining surface roughness and SilcoTek coatings. Learn how a smooth surface with low roughness, when layered with SilcoTek's chemically inert and corrosion-resistant coating, can amplify material performance.
-
Enhanced Corrosion Resistance: SilcoTek coatings are known for their exceptional corrosion resistance. When applied to a substrate with appropriate surface roughness, the combination creates a protective barrier against chemical attacks and harsh environments. Sensitive industries like semiconductor and biopharma often use electropolishing to smooth out the surface, which is only enhanced by our coatings. This is particularly beneficial in other industries such as oil and gas, chemical processing, and marine applications where materials are exposed to corrosive substances as well.
-
Improved Wear Resistance: A smooth surface with low roughness, when coated with SilcoTek's wear-resistant coating, can significantly enhance the material's ability to withstand abrasion and friction. This combination is especially advantageous in applications involving sliding or rolling components, such as precision gears, bearings, and valves, where wear resistance is critical for extended service life.
-
Reduced Friction and Energy Consumption: The pairing of low surface roughness and SilcoTek coatings with low friction properties can lead to reduced energy consumption and increased efficiency. In applications like automotive engines, pumps, and turbines, this can result in improved fuel efficiency and lower operational costs.
-
Chemical Inertness: SilcoTek coatings provide high chemical inertness, making them ideal for analytical equipment and laboratory instruments that handle aggressive chemicals and reactive substances. When combined with low surface roughness, the risk of sample contamination and reactivity is minimized, leading to accurate and reliable analysis.
-
Cleanability and Non-Stick Properties: The low surface energy provided by SilcoTek coatings results in excellent non-stick properties. This is beneficial in applications where the prevention of adhesion is crucial, such as in food processing equipment, medical devices, and mold release applications. SilcoTek can collaborate with customers to optimize the selection of surface roughness and our coatings to maximize the performance for their application. See the comparison below of hydrophobicity on rough vs. smooth surfaces.
Figure 2: Increased hydrophobicity and contact angle on rough surfaces with SilcoTek coatings.
-
High-Temperature Stability: SilcoTek coatings can withstand elevated temperatures, making them suitable for high-temperature applications, such as aerospace components and industrial furnaces. When used in conjunction with an optimized surface roughness, this combination ensures reliable performance under extreme temperature conditions.
-
Enhanced Biocompatibility: In biomedical applications, such as medical implants and surgical instruments, SilcoTek's Dursan coating can improve biocompatibility by reducing the chances of adverse reactions with bodily tissues. When combined with appropriate surface roughness, the potential for tissue adhesion and bacterial colonization is minimized, promoting better healing and reducing infection risks.
-
Versatility: The combination of SilcoTek coatings and surface roughness is versatile, as it can be applied to a wide range of substrates, including metals, glass, and ceramics. This adaptability allows for tailored solutions in various industries with diverse material requirements.
Tables 1 and 2 below show that there is very little difference in surface roughness as a result of coating. While different combinations of surface roughness and SilcoTek’s CVD coatings create a wide range of versatile performance characteristics, engineers don’t need to re-design products or change specifications to accommodate our coatings. Our coatings are all less than 2 microns thick, virtually adding no significant changes to part dimensions. To read the full report, click on the link below.
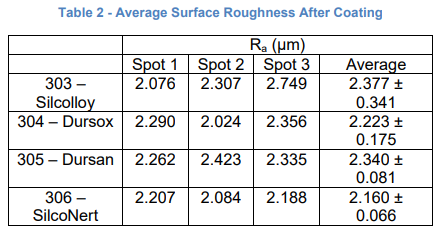

SilcoTek CVD coatings are thin and conformal, so in most cases customers do not have to account for changes in surface roughness in critical flowpaths.
This gives engineers and designers the ability to substantially improve the surface properties of parts while maximizing flexibility and ease of integration without impacting design.
SilcoTek coatings can be applied to most stainless steel, alloy, glass, and ceramic components like:
- Valves
- Flow meters
- Mass flow controllers
- Liners
- Compression and face seal fittings
- Electropolished components
- Instrument probes
- Sampling system components
Surface roughness and SilcoTek coatings stand as powerful allies. By understanding their significance and the benefits of using them together, industries can unlock new levels of material performance, reliability, and efficiency. Moving forward, a combination of these solutions promise to reshape industries and push the boundaries of what is possible. Contact us for more information!
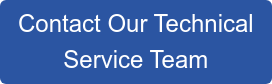