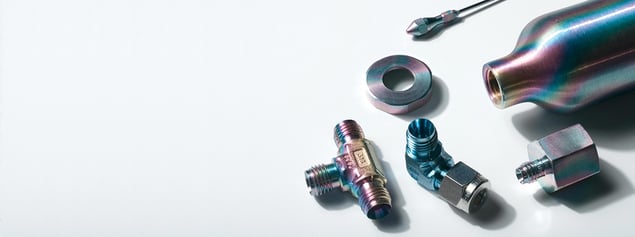
Ever wonder why SilcoTek coatings have a rainbow color and why the color appearance changes from part-to-part? Get the answer and more in our latest blog post.
What is the Acceptable Appearance of SilcoTek Coatings
SilcoTek’s Dursan® and SilcoNert® coating processes are known by our customers to improve surface inertness, durability, fouling, and corrosion resistance in a range of several industrial applications. If you have ever wondered why our coatings have a rainbow-like color, this blog post will explain the reason behind the appearance of our coatings and how the coating appearance falls into our specifications.
In this blog post you will learn:
- How SilcoTek's silicon chemical vapor deposition (CVD) process makes a part colorful.
- How coating thickness affects the coloration of the part.
- The acceptable range of color and how color relates to coating thickness specifications.
|
The CVD Coating Process and How a Thin Silicon Surface Makes Color
We bond silicon to metals, glass, or ceramics through a process called chemical vapor deposition (CVD). This process allows us to build a silicon layer on a surface one Angstrom (0.1 nanometer (nm)) at a time. A super thin layer of silicon is pretty clear, in fact you can see through a thin silicon layer. So how does the surface become so colorful? Well as the silicon thickness increases on say a stainless steel surface, light which travels through the silicon is bent. The light then reflects off the stainless surface and is bent again. All this light bending causes some wavelengths of light to cancel out each other while other wavelengths are reinforced.
Have a question about our coatings and how they can improve your products or process? Contact our Technical Service Team for a free no obligation consultation and get the CVD coating information you need.

The canceled (or interference) wavelengths of light aren't seen by your eye while the reinforced wavelengths hit your eye retina cones and are seen as color. Changing the color of a thin silicon surface is easy, a few nanometer change in silicon thickness can have a big impact on the colors you see.

The above image reflects the acceptable thickness spectrum that the Dursan® coating process may deposit. Dursan’s light refraction properties correlate with a coating thickness between 400 and 1600 nm. The refraction properties of the Dursan coating process are more subtle than our SilcoNert® coating, making it easy to distinguish between the two.
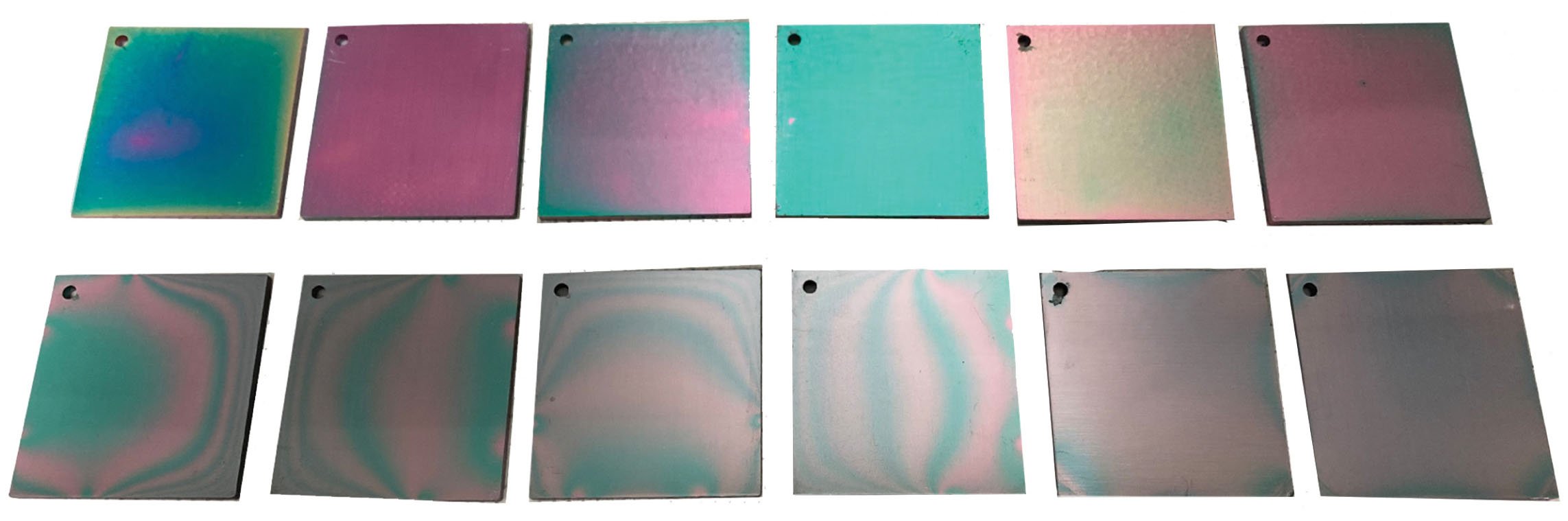
The above image reflects the acceptable thickness spectrum that the SilcoNert® coating process may deposit. SilcoNert’s light refraction properties above correlate with a coating thickness between 100 to 500 nm. The light spectrum produced by the SilcoNert coating process is more vibrant than Dursan and includes deep blues, purple, green, and gray. The coupons shown above are highly polished, resulting in a bright color spectrum. Rough and unpolished steel surfaces will subdue the colors.

Important Notes about Coating Appearance
The colors of SilcoTek’s coatings are the result of light absorption and/or refraction through the thin film of the coating on a substrate. A slight change in the thickness of the coating (a few nanometers) can have a big impact on the visible colors because that small change in thickness changes the interference pattern of the light. This process of light absorption and/or refraction gives our coatings their signature rainbow appearance. A few things to note regarding the coating appearance:
- As long as the deposition thickness (and therefore color) meets our specification, there's no impact on surface properties like inertness, hydrophobicity, and anti-fouling.
- The acceptable thickness range for SilcoNert 2000 is 100-500 nm.
- The acceptable thickness range for Dursan is 400-1600 nm.
- All of SilcoTek’s coating processes have specified acceptable thickness ranges that can be found on our coating specifications page.
What About Coating Thickness and Corrosion?
One surface property that can be affected by coating thickness is corrosion protection. SilcoTek has written a white paper on this relationship that can be found here.
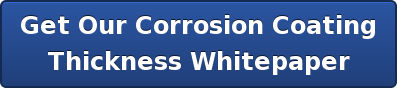
We have conducted experiments to investigate the impact of coating thickness on anti corrosion performance within our coatings’ current production thickness ranges. The table below compares our two corrosion resistant coatings, Silcolloy® 1000 and Dursan®, at the low end of their thickness output versus the median to high end thickness output, respectively. The test was done by immersing coated coupons in 6M hydrochloric acid under room temperature, for a preset amount of time (ASTM G31 guidelines).
Coating
|
Thickness range (nm)
|
Corrosion 24 hours (MPY)
|
Corrosion 168 hours (MPY)
|
Silcolloy 1000 (thin)
|
250 ~ 320
|
1.93
|
65.5
|
Silcolloy 1000 (median to high)
|
750 ~ 1200
|
0.94
|
30.8
|
Dursan (thin)
|
300 ~ 350
|
1.18
|
52.1
|
Dursan (median to high)
|
650 ~ 900
|
1.50
|
21.5
|
Do thicker coatings provide a better corrosion resistance to the surrounding environment?
With all things being equal in the coating, it can. A thicker coating will create a longer diffusion barrier and restrict corrosive compounds from interacting with the substrate causing rust to occur. However, creating a thicker coating has several potential issues including:
- Stresses induced as the film grows thicker which can lead to film cracking and delamination
- Creation of potential interfacial failure sites and the possibility of more stresses throughout the coating
- Particle generation
- Growth mechanisms that may impose an upper limit on coating thickness
- Extended deposition time that leads to metallurgical property change.
Need convincing? Watch our corrosion resistant coatings in action!
While overcoming these issues to develop thicker coatings is an option, SilcoTek® continues to take the less is more approach and continues to evolve our coatings to a higher quality and more consistent material to further improve the corrosion resistance of critical components and flow paths. By applying a thin high quality layer, SilcoTek takes advantage of both improved corrosion resistance and a better performing high durability surface.
Advantages of a thin high quality CVD coating:
- Order of magnitude improvement in corrosion resistance
- Maintain high dimensional tolerance
- Assures a leak free seal in critical flow paths
- Allows the amorphous silicon to bend or deflect with the steel surface without failure
Learn more about SilcoTek® corrosion resistant coatings.
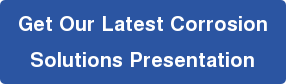
If you have a question about our coatings? Contact our Technical Service Team or get the latest information about our coatings by following us on LinkedIn.
