Measuring the Porosity (or lack thereof) of SilcoTek® Coatings
SilcoTek® provides thin film coatings deposited via Chemical Vapor Deposition (CVD). Customers often ask for the porosity of our coatings. SilcoTek offers coatings for a variety of industries and an even wider variety of applications. We often are asked “how porous are your coatings?” The short answer is “they are not porous”, but the long answer will be described here.
Coating Porosity
When measuring roughness, there are size domains, each with their own unit of measurement. For instance: which is rougher? The Rocky Mountains or the Appalachian Mountains, a piece of paper or a piece of sandpaper, a glass slide or a mirror polished metal sample? Each pair of comparisons would be measured in a different way and on a different scale. The same is true for porosity. Figure 1 shows various scales of porosity. They are sorted into 3 size domains: macroscopic, microscopic, and atomic. Examples of porosity are shown at each level. For instance, a sponge is obviously porous at the macroscopic level. This can be witnessed with the naked eye. A sintered metal disc does not appear to be porous until you examine it at the microscopic level. Finally, silica-like coatings, such as our Dursox® coating or a 2D silica coating on graphene as shown in the image, are not porous until you reach atomic levels. 1 The 5 Å sized pores in glass may allow small molecules such as hydrogen (2.9 Å kinetic diameter) to permeate through easily, but a molecule such as oxygen (3.5 Å kinetic diameter) would diffuse much slower, and a molecule like carbon tetrachloride (5.9 Å kinetic diameter) would struggle to penetrate at all.
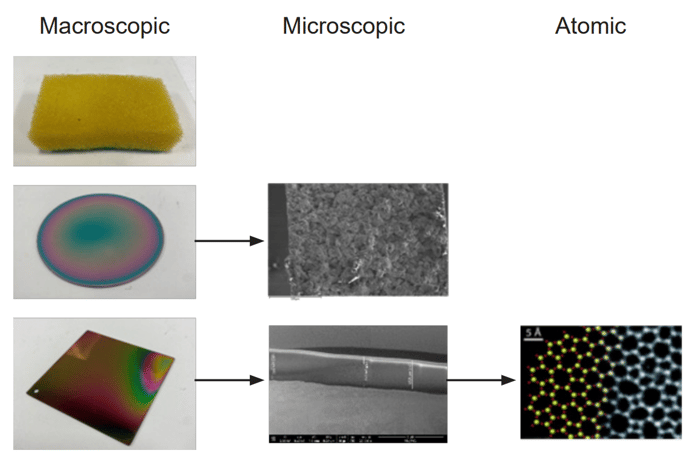
Figure 1: Various domains of porosity and examples of each.
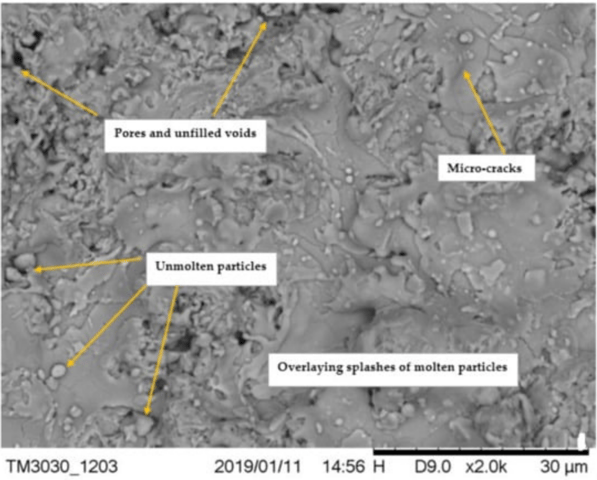
Figure 2: Example of a “typical” atmospheric plasma-sprayed coating of chromium oxide onto Q235 steel. Many anomalies in the coating are highlighted.
Most customers when asking about the porosity of our coatings are inquiring about the microscopic domain, which is why SilcoTek says our coatings are non-porous. Figure 2 shows an electron image of a typical plasma spray coating along with commonly found defects in such a coating. Figure 3 shows a focused ion beam cross section of two of our coatings (Dursox® and Silcolloy®) on stainless steel. Note that there is a porous carbon layer deposited onto the Silcolloy to protect it from ion milling performed during sample preparation, and is not a part of the SilcoTek coating. This coating is not a SilcoTek coating. Also note that Figure 3 was taken under a much higher magnification (12,500x) than Figure 2 (2,000x), yet no visible pores or other defects could be detected in the Dursox or Silcolloy coating.
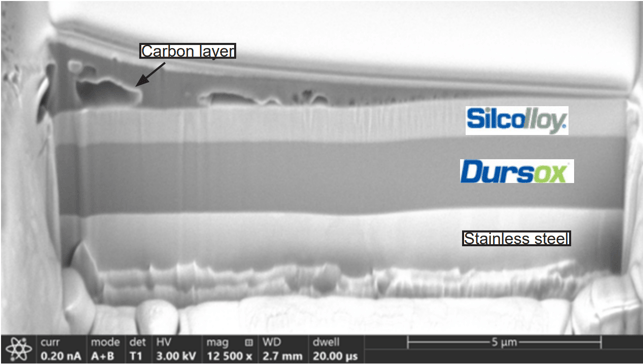
Figure 3: Cross sectional FIB-SEM of a stainless steel coupon coated with Dursox and then Silcolloy. There is no visible porosity in either coating. There is some “curtaining” which is a result of the milling process to expose the coated steel coupon.
SilcoTek’s coatings can be considered “non-porous” in comparison to similar protective technologies such as thermal or plasma spray coatings. A previous study using polarization resistance scan in 5% HCl solution has shown that the coatings are also pin-hole free providing complete protection to the base substrate.
To download this technical insight, click below:
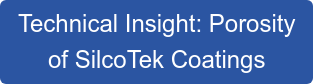
Coating Porous Materials with SilcoTek Coatings
On the other hand, what if your material itself is porous? Our coating technology won't plug filter media because our precision CVD deposition process distributes the coating without blinding of the filter surface or significantly impacting filter efficiency.
The high surface area of porous, sintered filtration media often leads to fouling, corrosion, and undesirable chemical reactions in any process system. SilcoTek coats filters from manufacturers serving a variety of industries, including coal gasification, petrochemical, chromatography, and more to extend service life and improve performance. SilcoTek CVD coatings eliminate unwanted chemical reactions and extend the lifetime of filters without clogging their pores. We're able to deposit a nanometers-thick coating layer by using gases rather than liquid, allowing for 100% coating of filter surfaces, even with complex geometries, blind holes, and delicate critical surfaces.
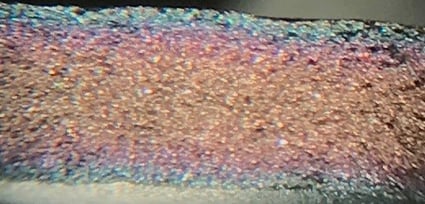
Figure 4: Cross-section of a SilcoNert 2000 coated frit.
Figure 4 shows a cross sectional photo of the coated frit after it has been broken in half. The frit above shows coating throughout without blocking the pores. There are three distinct colors in the frit: gold which measures ~50 nm, pink which measures ~65 nm, and blue which measures ~80 nm. Raman spectroscopy was performed to ensure that the material that was deposited on the inner most portion of the frit was the same as the material on the exterior, and it was confirmed that the coating is an amorphous silicon coating, which is what makes our SilcoNert® 2000.
Check out our technical insight on coating frits:

Conclusion
Whether you want to coat a porous material or wondering if our coatings will be porous, SilcoTek's CVD coatings can conformally coat your materials. We have a range of different coating options to meet your application's needs. Our coatings are an excellent barrier between the environment and the substrate, thin enough to not block any pores or cause back pressure issues, and are consistent through the entire frit.
Contact us today to get more information about SilcoTek's coating technology and how we can help your application!
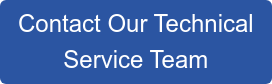
References:
1. Huang PY, Kurasch S, Srivastava A, Skakalova V, Kotakoski J, Krasheninnikov AV, Hovden R, Mao Q, Meyer JC, Smet J, Muller DA, Kaiser U. Direct imaging of a two-dimensional silica glass on graphene. Nano Lett. 2012 Feb 8;12(2):1081-6. doi: 10.1021/nl204423x.
2. Odhiambo, J.G.; Li, W.; Zhao, Y.; Li, C. Porosity and Its Significance in Plasma-Sprayed Coatings. Coatings 2019, 9, 460. https://doi.org/10.3390/coatings9070460