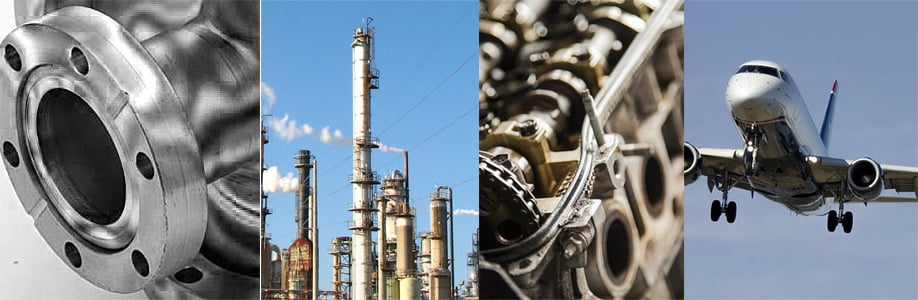
We apologize for the inconvenience and would do just about anything to avoid asking our customers to disassemble parts. But it's for a good reason, quality.
Let's get this straight right off the bat. We don't like asking our customers to disassemble their parts prior to shipping to us for chemical vapor deposition (CVD) coating service any more than you like doing the disassembly. You may ask, why do parts have to be disassembled and, more importantly, why do I have to do the disassembly? To answer those questions we'll need to discuss some chemical vapor deposition process details that make it necessary to disassemble parts. In the end I think you'll agree that disassembly is important to assure coating quality for any CVD process. As for the question about why do I have to disassemble the part; well there are ways around that.
In this blog post you will learn:
- 4 reasons why it's important to disassemble parts before coating
- Why quality can be adversely affected if parts are not disassembled
- Ways you can avoid disassembling/assembling parts when applying a CVD coating
|
Why It's Important to Disassemble Parts
In order to meet quality and performance expectations, it's important to disassemble your parts. But why exactly? Here are some really good reasons:
1. To be sure the parts can be coated.
You see we coat parts at relatively high temperatures; high enough to melt plastic, o-rings, most seals and some metals. Often parts like valves, regulators, flow controllers, etc. will have internal seals that will be damaged during the heating cycle of the coating deposition process. So we need to be sure there are no internal components that can fail during processing. Also some internal parts may not be compatible with our process. It's possible that components may be plated or be made of materials that can react with our deposition gas or will melt in our reactor. So we need to confirm all parts are compatible with processing. The best way to confirm compatibility is by thoroughly examining all components before coating. For example we'll confirm the metallurgy of parts and verify there are no o-rings hidden within the part. That way we're sure not to damage your part.
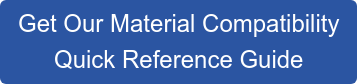
2. To be sure our surface preparation process is effective.
Parts that have internal components also have crevices, small holes, or complex internal areas that can make cleaning and surface preparation difficult. If the surface is not properly prepared, the coating can fail, not meet inertness standards, or fail visual inspection (ie, just plain look bad). In fact proper surface preparation is the foundation of a good coating. That goes for any coating process. So if you deal with a shop that is not clean or is not fanatical about cleaning, you might want to find another shop. Every part should be properly cleaned and inspected to be sure the coating will be effective. To get a better idea of how to properly prepare a surface for coating, get our surface preparation tips.

3. To be sure parts are properly coated.
Our CVD coating process involves injecting specialty gases into a process reactor. The gas reacts with exposed surfaces to bond an inert silicon coating to the part. In order to achieve a consistent high quality coating, parts must be evenly exposed to the process gas. That's why we pay special attention to part fixturing and process conditions. An improperly fixtured part may not get the right amount of coating gas for an effective coating. This can lead to premature failure of the coating.
4. To be sure parts can be properly inspected after processing.
We have exceptional coating quality but occasionally parts fail our post coating inspection process. If we can't inspect the part, we're not able to assure coating quality. So if for some reason a part were to be coated assembled, we'd want to disassemble the part to be sure we coated it properly. I'm sure you'd want that too.
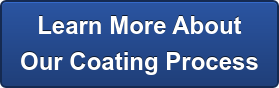
How to Avoid Disassembling and Reassembling Parts
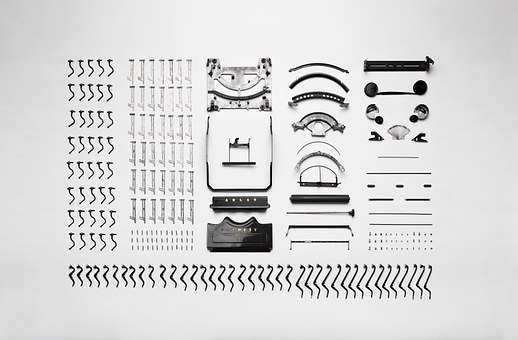
Hopefully you're convinced that disassembly is necessary. But why do you have to disassemble your part?
I guess we should ask this question: Who would you want to disassemble your part? It's a tall order to ask a third party to disassemble a part. Here's why.
- Most shops are not experts in component disassembly. For example we're experts in CVD coatings and know a lot about valves, regulators and other assemblies because we see them every day but we're not trained by the factory to disassemble or assemble them. It would be very difficult for a shop be qualified in disassembling all parts made from all vendors.
- Taking apart all sorts of valves, regulators or other components can lead to some mistakes. Mistakes you don't want us to make with your parts.
- Disassembly and reassembly would only add cost to the process. We want our customers to pay for our high quality coatings not disassembly or assembly.
- Finally there's the L word. Liability. We don't want to delve willy nilly into tearing down someone's property if there's a chance of a failure.
Why do you have to disassemble? First if you understand how to take the component apart, you'll be better at reassembly so there's that. It does sound a bit like getting advice from that perfectly fit friend telling you that you'd be better off going to the gym. It's true but still not going to happen. I'm here to tell you that you don't have to go to the gym. Have that doughnut! And you don't have to disassemble or assemble the part at all! Here are some tips:
1. Go to our Buy Coated Products page and purchase coated parts directly from the manufacturer. You'll get parts that are coated and assembled by qualified factory technicians. The downside? It may take additional time if the part is not in stock, so plan delivery times with the vendor. Buying coated parts is a bit like entering a bike race, but you have an electric bike. You most certainly win but without the sweat!
2. Contract a vendor to disassemble the part. Yes I just said it's a tall order to get someone to disassemble a part, but there are specialty machine shops that are qualified to disassemble/assemble parts. Outsourcing will add to lead time and increase cost but it can be worth it for companies with limited internal resources.
3. Contract with the manufacturer and ask them to send the disassembled part to us for coating. We'll send it back to the manufacturer and they'll reassemble the part for you. This can add additional cycle time but is a good option to achieve your goal of getting the material performance you need without the headache of managing part disassembly/assembly. We have many customers who go with this option, especially larger, high volume users.
Hopefully you're convinced that we're not asking you to disassemble a part just to be a pain. Also know that you have options to minimize the headaches and get a great coating.
Have other questions about our coatings? Go to our FAQ page, or ask the experts.
